Flotation machine is one of the most common mineral processing equipment used for separating copper, lead, zinc, nickel, gold, which can be divided into mechanical agitation flotation machine and air inflation flotation machine. The working principle of flotation machine is that the v-belts of rotating motor drives the impeller to rotate and form the negative pressure, so the air mixes with pulp and reagent, then forming the fining foam. The mineral adheres on the foam, and generates the mineralized foam layer on the surface of the pulp and then the foam is scraped by the scraper blade under the certain height of the control page.
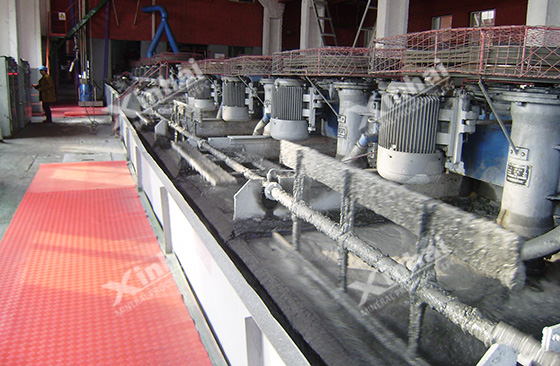
As the main equipment of the concentrator, the floatation machine is featured with high power and long-running time, which needs maintenance to guarantee the stable running of the flotation machine. Therefore, the flotation machine operator should maintain it as follows:
Use the table of contents below to navigate through the guide:
01Learn about the structure of the flotation machine
Different types and models of the flotation machine have different structures. But in general, the flotation machine includes motor, bearing, scraper, central tube, tank, steady flow, diversion pipe, impeller, cover plate and suction pipe. For the flotation concentrator, the flotation machine operator should clear the configuration details of the flotation machine, making sure that problems can be timely found out and avoiding the loss of economic benefit.
02Learn about the operation notes of the flotation machine
1. Pre-operation of the flotation machine
(1) Before the operation, check whether there are sundries in the flotation tank to prevent the sundries from blocking the impeller or the circulation hole and channel. If necessary, open the ore discharge gate to flush.
(2) Check the flexibility of the ore discharge valve and the liquid level control device, which should adjust the ore discharge according to the separation requirements to maintain the constant height of the slurry level.
(3) Check the scraper, triangle transmission belt and box lining rubber to keep it smooth. Check whether the false bottom, steady flow plate and baffle are complete and steady.
(4) Check whether the air pipeline of the flotation machine is unblocked. If it is blocked, the air pipeline should be dredged in time.
(5) Check whether the oiler of the flotation machine is filled with lubricating oil and whether the bearing of the flotation machine is filled with grease.
(6) check whether the fastener of the flotation machine is loose.
(7) Check whether the vertical spindle of belt pulley rotates flexibly and whether the impeller collides or frictions.
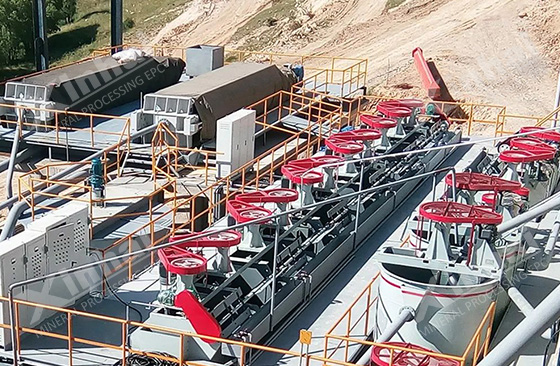
2. Start of the flotation machine
The start of the flotation machine has two conditions, one starts it with an empty tank, another starts it with a full tank after the shutdown. These two conditions are different in the operation sequence.
When starting the flotation machine with the empty tank, the flotation machine operator should feed the ore first, and start the agitation tank, then start the flotation machine that connects with the feeding box. After the slurry completely submerges the cover plate, start the next flotation machine.
When starting the flotation machine with a full tank after shutdown, the flotation machine of this phase should be started after the next stage of equipment is started according to the flow direction of the slurry. Open the agitation tank, start it, and open the feeding pipe to injecting the pulp until the overflow. Note that start from the last tank to the first tank one after another.
3. Shut-down of the flotation machine
As with startup, there are two conditions of shut-down for the flotation machine, one is shut-down without the pulp, another is shut-down with a full tank.
For the shut-down without the pulp, the feeding shall be stopped first. When the feeding is completely stopped, the gate of the middle tail box shall be opened and the agitation tank shall be stopped. Keeping the normal running of the flotation machine until the cover plate can be seen, then stop the motor of the flotation machine, and open the discharging valve to discharging the rest of the pulp in the tank.
The steps are relatively simple for the shut-down with a full tank. Stop the ore feeding first, then stop the agitation tank according to the flow direction of slurry, and stop the flotation machine backward successively from the first tank of the flotation machine.
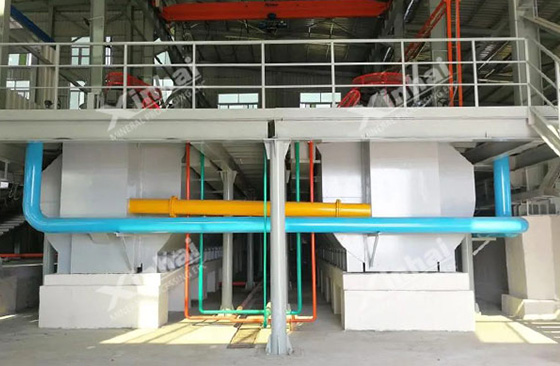
03Keep the daily inspection of the flotation machine
The daily inspection of the flotation machine should be equipped with professional personnel who are familiar with the operation of the flotation machine. Usually, a careful inspection of the flotation machine should be carried every 3 to 4 months, the new flotation machine need to be inspected regularly in the initial work of the time. Besides, those easy-to-damage parts should be reserved so that they can be replaced timely once damaged.
The daily inspection of the flotation machine mainly includes:
1. Whether the bolts of each part are loose, whether the triangle belt is complete, and whether the safety cover is complete and firm.
2. Whether the temperature of the motor and motor bearing is normal.
3. Whether the inspiratory volume is normal.
4. Whether the lubrication points are lubricant and whether the lubricating oil is sufficient.
5. Whether the ore drawing valve and the box body are straight.
6. Whether the tank leaks ore.
7. Whether the scraper parts are in good condition.
The above is daily maintenance should be done for the flotation machine. The flotation machine operator should be responsible for the daily maintenance, timely find problems and take the corresponding measure.