As the main equipment of the mineral processing industry, the grinding equipment can be divided into four kinds: rod mill, energy-saving ball mill, grid-type ball mill, overflow type ball mill.
Use the table of contents below to navigate through the guide:
01Grinding Equipment One: Rod Mill
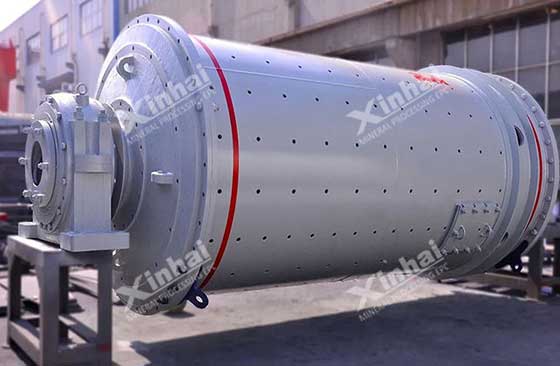
1. Application of rod mill:
Rod mill adopts advanced controllable feeding and discharging technology and uses a suitable grinding medium by combining it with the actual grinding material. It changes the traditional face-to-face contact into line-to-line contact, which makes the particle size more uniform, and the yield higher. So, the rod mill is widely used in those industries that have high requirements for grinding results, such as refractory material, chemical industry, metallurgy, and glass.
2. Working Process of rod mill:
The cylinder of the rod mill is fitted with the suitable grinding medium- steel rod. Under the action of centrifugal force and friction force, the grinding medium is lifted to a certain height and then falls down in a state of throwing or discharging. The materials are continuously sent into the cylinder from the ore feeding port, then crushed by the moving grinding medium, and discharged by the overflow and the continuous ore feeding.
02Grinding Equipment Two: Energy-saving ball mill
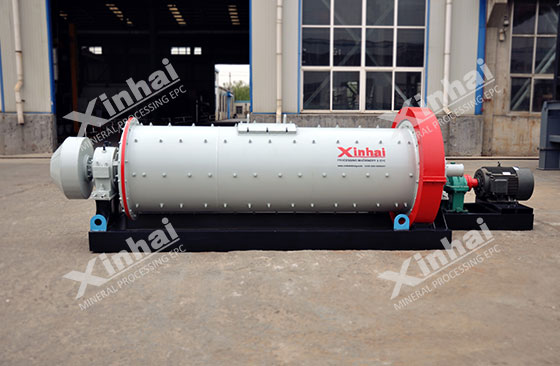
1. Structure of energy-saving grid ball mill:
Energy-saving grid ball mill design consists of a feeding part, discharging part, rotary part, transmission part (reducer, small gear, motors, electrical control), and other major parts. The hollow shaft is steel castings, and the liner is detachable. Rotary gear is processed by casting hobbing. The cylinder is lined with a wear-resistant liner plate with good resistance to wear. This machine works stably.
2. Working principle of energy-saving ball mill:
After the crushing process by the jaw crusher or the two-stage closed circuit crushing system composed of jaw crushers, the materials are uniformly fed into the energy-saving ball mill by the ore feeder and then sent to classifying equipment for classifying treatment. That unqualified ore that does not meet the suitable particle size will return to the ball mill for re-grinding.
03Grinding Equipment Three: Grid-type ball mill
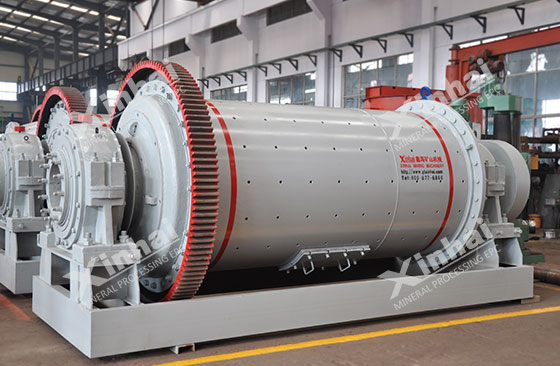
1. Advantages of grid-type ball mill:
• Fast discharging speed, which can reduce the over-crushing problem and increase per-unit capacity;
• The discharging port of the grid ball mill adopts a cone design, which not only increases the volume but also forces the classification of the steel ball at the end of the cone. The closer to the discharging port, the smaller the diameter of the steel ball is, which increases the effect of repeated grinding and further improves the fineness of the material;
• The grid-type ball mill adopts the grooved ring-type lining plate, which increases the contact surface between steel ball and ore, strengthens the grinding effect, and reduces the power;
• The particle size of a grid-type ball mill should be 0.2 ~ 0.3mm, so it is commonly used in the first stage of grinding. What's more, the grid-type ball mill can timely discharge the qualified products, and reduce over-crushing. Its processing capacity is about 15% higher than the overflow-type ball mill with the same specifications. If the particle size needs to be ground to 48 ~ 65 mesh, the grid-type ball mill is better.
04Grinding Equipment Four: Overflow-type ball mill
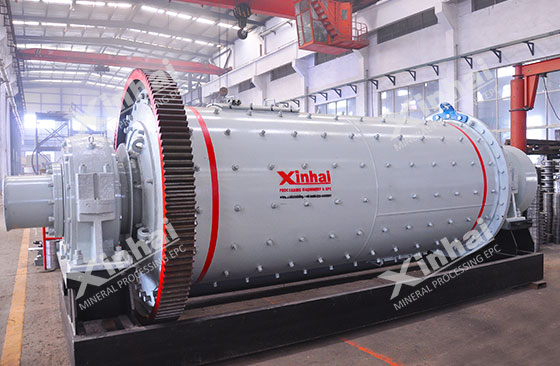
1. Advantages of overflow ball mill:
• The jack-up device, is easy maintenance;
• The hydrostatic and hydrodynamic bearings ensure the smooth operation;
• Low-speed transmission is easy for starting and maintenance;
• The oil-mist lubrication device guarantees reliable performance of bearings;
• The gas clutch adopts the flexible start-up model.
2. Application of overflow ball mill:
Overflow type ball mill is usually used for fine grinding of mineral materials. Generally, it forms a two-stage closed-circuit grinding system with a type of ball mill.