As a commonly used solid-liquid separation equipment, the filter press machine often feeds the slurry into the filter chamber under the action of the feed pump pressure and imposes certain pressure on the slurry through the filter medium to make the liquid dialysis out.
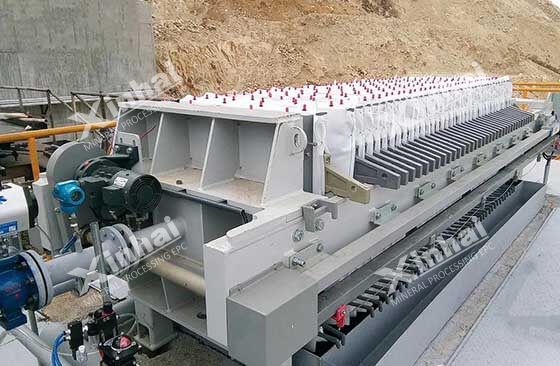
In the production process, the filter dewatering effect of the filter press machine is mainly related to the slurry properties, filter cake, pressure difference, and the vacuum degree on both sides of the filter medium and the filter medium. Below, take you to understand how to effectively improve the filtration and dehydration effect of filter press machine from the above aspects.
Use the table of contents below to navigate through the guide:
01Improve the slurry properties
Slurry properties mainly involve slurry concentration, slurry temperature, solid material, particle size composition, and flotation reagent contained in slurry.
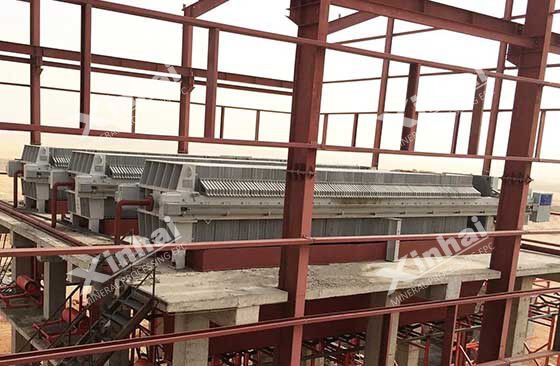
Increase the slurry concentration appropriately
In a certain range, the productivity of the filter press machine will be improved with the increase of slurry concentration. Therefore, properly increasing the slurry concentration can enhance the productivity of the filter press and reduce the moisture content of the filter cake. Generally, most concentrators require a slurry concentration is greater than 40%.
Raise the slurry temperature
The slurry temperature is increased while its viscosity decrease, so as to speed up the dehydration speed and improve the productivity of the filter press. In actual production, it is not economical to heat all slurry, and only a few minerals need to heat the slurry due to technological requirements.
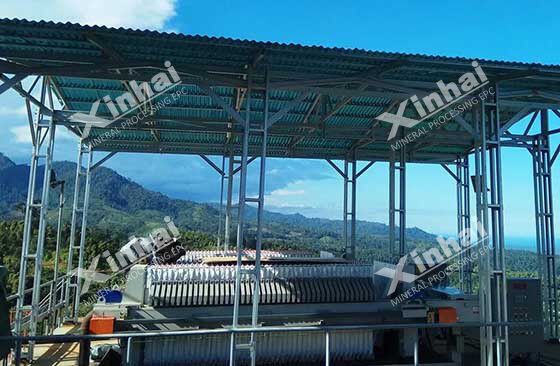
Pay attention to the solid material in the slurry
The solid material in the slurry also has a great influence on the filtering effect of the filter press. For coarse material, the filter cake formed by the pore is large, the filter cake resistance is small, which is conducive to the filtrate through, and the productivity of the filter press is relatively high, the filter cake moisture is low. For the fine-grained materials, the slurry is easy to block the filter hole during filtration, resulting in filtration difficulties, thus affecting the productivity of the filter press machine.
Solve the problem that the fine material is not easy to filter
If there are more fine particles in the slurry, the filtration property of the slurry is poor. In production practice, on the one hand, the filter aid can be added, that is, the coarse material can be mixed into the fine-grained slurry, so as to change the particle size composition of filter cake of filter press and improve water permeability; On the other hand, the fine ore particles can be agglomerated into flocs by means of coagulant, forming loose filter cake on the surface of the press cloth. The filter cake has good air permeability, so as to obtain good filtration and dehydration effect.
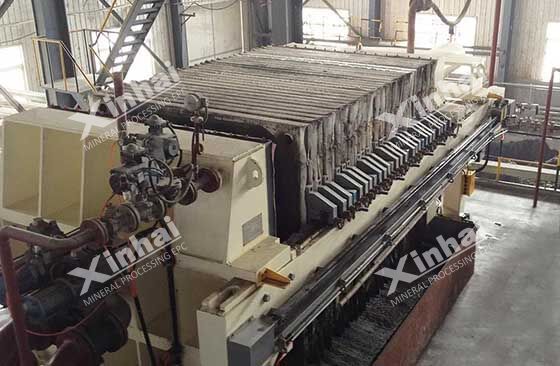
Specifically, analyze the properties of flotation reagent
The flotation reagents contained in the slurry are more complicated. Most flotation reagents can reduce the filterability of pulp, only a few flotation reagents can improve the filterability. Therefore, the effect of flotation reagent on filter dehydration effect of filter press should be judged according to the type, nature, and dosage of flotation reagent used.
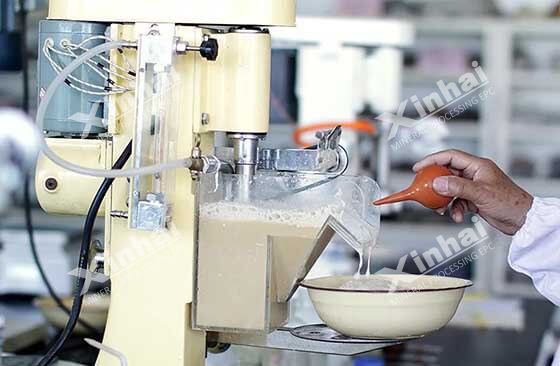
02Change the properties of filter cake
The properties of filter cake mainly include porosity, resistance, and cracking of filter cake.
The higher the porosity of filter cake, the lower the moisture content of filter cake. And the porosity of filter cake is related to the particle size and composition of filter material. Therefore, it is necessary to ensure material granularity and a narrow granular range.
The cake resistance can affect the dehydration speed of the filter press machine, which mainly depends on cake porosity, thickness, and slurry viscosity. In the daily operation, it is necessary to keep the even thickness of each part of the cake layer, so that the resistance of the filter cake is evenly distributed. The uneven thickness will result in uneven resistance of each part of the filter cake. The relatively thin position has small resistance and rapid precipitation of filtrate, thus forming many holes, and affecting the speed and effect of filtration and dehydration.
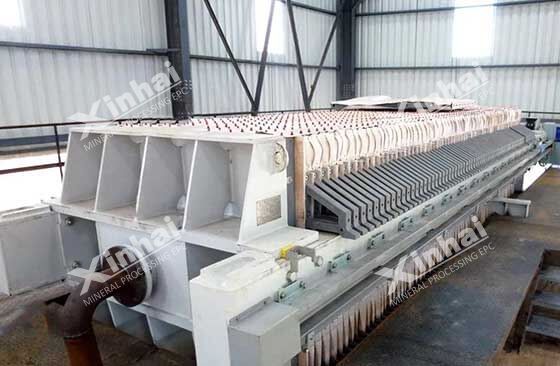
03Use a suitable pressure differential
Generally speaking, the finer the particle size of the material in the slurry, the greater the required pressure, but too high a pressure difference will accelerate the damage of the filter medium and increase the power consumption. For the fine material slurry, increasing the pressure difference easily leads to the fine material drilling into the filter hole, resulting in serious blockage and reducing the filtration dehydration speed.
Therefore, in the filtration and dehydration process of ultrafine material slurry, it is suggested to adopt a small pressure difference (ensure that the filtrate can get the necessary speed and help to reach a certain water content), thin layer filter cake, or appropriately extend the filtration and dehydration time.
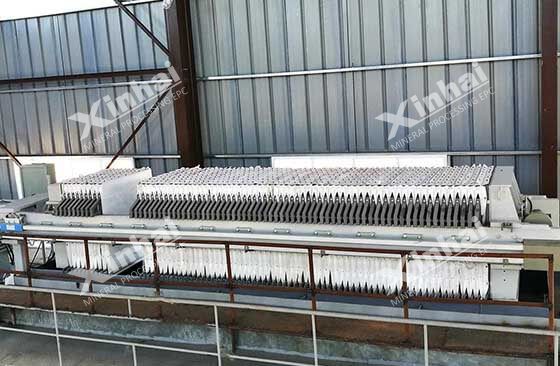
04Reasonably select the filter media
Generally, the filter medium is usually made of cotton cloth or fiber cloth. In the process of filtration and dehydration, clogging of filter cloth will inevitably affect the productivity of the filter press. The reasons why the filter cloth is clogged are the fine particles enter the filter hole, and the precipitates generated by chemical reactions cause the clogging. If the fiber cloth is seriously blocked and even affects productivity, the filter cloth must be cleaned or replaced in time.
Therefore, it is recommended that the filtering medium be selected according to the following requirements in order to improve the filtering dehydration effect of the filter press machine:
The high recovery rate of filtered materials;
Small filtration resistance;
Meet certain mechanical strength requirements;
Not easy to plug, easy to clean;
Easy to install and disassemble, and the thickening of filter cake can be firmly attached, and the filter cake is easy to unload when removing.
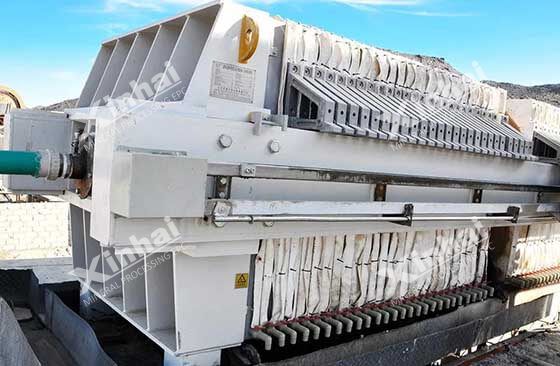
These are the four measures to improve the dehydration effect of the press filter machine. In the filtering process, there are still many factors that affect the filtering effect of the filter press machine. The operator needs to analyze the reasons according to the actual production situation on the site and come up with scientific and reasonable solutions to guide the production on the site, so as to obtain the ideal filtration and dehydration effect.