The Grinding mill is essential equipment in the concentrator, whose purpose is to grind out as many qualified granular materials as possible with small power consumption and light crushing.
In the practice, the factors affecting the grinding efficiency of ball mill can be summarized into three aspects: material characteristics, equipment performance, and operating conditions.Let's discuss in detail the above three aspects that affect the grinding efficiency of ball mill.
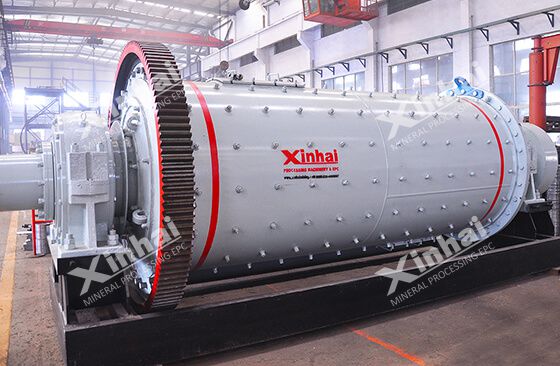
Use the table of contents below to navigate through the guide:
01Material characteristics
The effect of material on grinding efficiency of ball mill is mainly reflected in three aspects: ore property, feeding size, and product size.
Ore property
The properties of ore (eg. mechanical strength, dissemination characteristic, and grinding ratio) will directly affect the grindability index of ore. The harder the ore is, the smaller the grindability index is, the more energy consumption is, and the lower the processing capacity of the ball mill is.
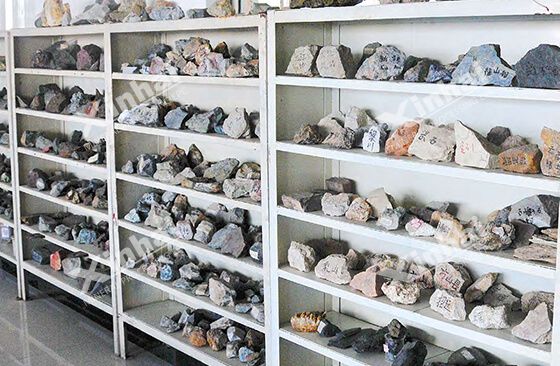
In addition, the nature of each mineral in the ore is also different, it can be divided into easy-to-grind and hard-to-grind parts, which cause the selective grinding phenomenon, that is, one part has not been ground, but another part has been crushed. For those ores that are fear of over-crushing (such as tungsten, tin ore), it is necessary to screen out the ground materials in time.
Feeding size
The coarser the ore, the longer the grinding time, the more power consumption taken to the specified fineness, and the lower the grinding efficiency.
The effect of feeding size on the grinding efficiency of the ball mill is related to ore properties and fineness. In production, the ideal ore feeding size depends on the result of technical and economic calculations. Fine feeding size means the high cost of crushing operation; coarse feeding size means low crushing operation cost, but the high grinding operation cost.
In the case of combining crushing and grinding costs, the total cost of both is the lowest under a certain feeding size, which is the ideal ore feeding size of the ball mill.
Product size
The particle size of grinding products directly affects the final separation index. If the particle size of grinding products is too coarse, the useful minerals and gangue are not fully dissociated. If the particle size of grinding products is too fine, the serious over-grinding phenomenon is produced. Both of which will reduce the grinding efficiency of the ball mill.
Generally, the harder the ore, the coarser the ore feeding, the finer the product, and the lower the grinding efficiency of the ball mill, the higher the grinding efficiency index calculated by (KW • h/t).
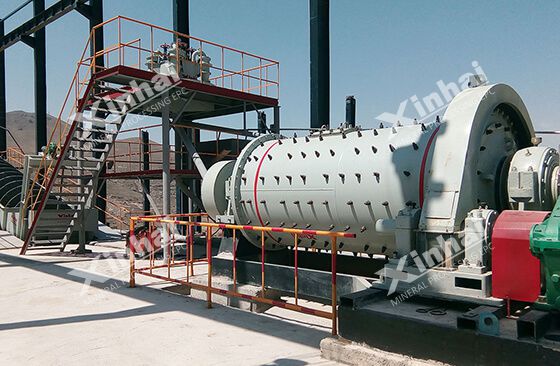
02Equipment performance
Except for the material nature, the performance of the ball mill is a major factor affecting its grinding efficiency, including the type of ball mill, the diameter, and length of the ball mill, speed of the ball mill.
Type of ball mill
Different types of ball mills have different equipment characteristics and structures. At present, most concentrators often use grid ball mill and overflow ball mill. Among them, the grid ball mill adopts the low-level discharge, the storage of pulp in the ball mill is less, and fine ore particles that have been ground can be discharged in time, and the over-grinding phenomenon of grid ball mill is less than that of overflow type ball mill, the grinding efficiency is 10%-15% higher than that of overflow type ball mill, sometimes even 25%.
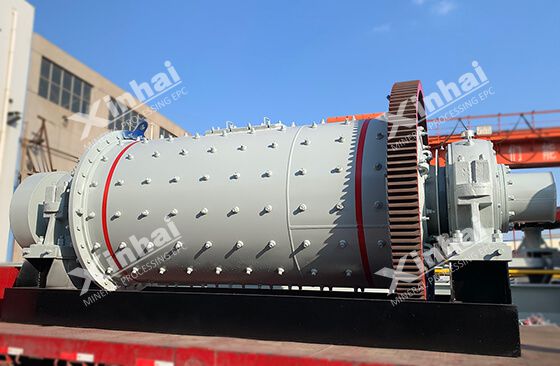
Diameter and length of ball mill
For the same type of ball mill, its power consumption, grinding efficiency, and grinding effect are related to the diameter and length of the ball mill. Among them, the length mainly affects the grinding time and then affects the grinding fineness. If the ball mill is too short, it will fail to complete the specified grinding fineness, while if the ball mill is too long, it will increase power consumption and produce over-grinding. In production, the ratio of length to the diameter of most ball mills is in the range of 0.78-2.
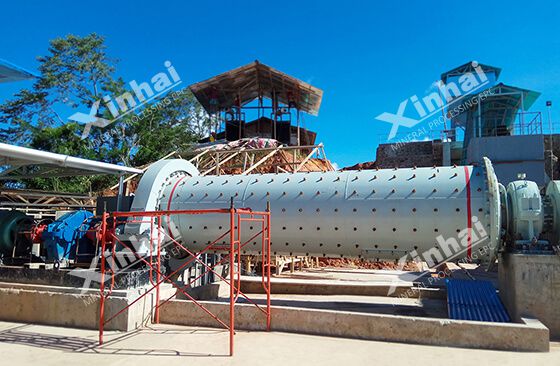
Speed of ball mill
The speed of the ball mill is closely related to the ball loading rate. There are two different situations: work below the critical speed and work over the supercritical speed. So far, most ball mills operate below the critical speed. The useful power varies with the rotation rate when the ball rate is kept constant. When the rotation rate is a suitable value, the useful power can reach an ideal value. At present, the rotation rate of the ball mill is roughly 66-85%, most of which are below 80%. It is difficult to achieve a high grinding efficiency when the speed is slightly lower.
03Operating condition
In the daily operation process, the ball mill operator should be familiar with the equipment structure, performance, and working principle, and closely observe the key parameters of the operation, such as ball loading system, grinding concentration, and feeding speed, so as to ensure that the grinding efficiency meets the mineral processing requirements.
Ball loading system
The ball loading system affects the grinding efficiency of the ball mill mainly includes two aspects: ball loading rate and ball type.
■ Ball loading rate: Different ball mill speed has the different limit of ball loading rate. When operating within the critical speed, the ball mill loading rate is usually 40-50%.
■ Ball type: The size of the steel ball should be appropriate to the thickness of the ore particle, and the weight ratio of various ball diameters should be suitable for the particle size characteristics of the grinding material. When the ball mill is started for the first time, three kinds of balls are needed to be proportioned. When the ball mill is running normally, there is no need to add small steel balls. However, if the particle size of useful minerals isn’t achieved monomer separation, and the grinding fineness cannot meet the separation requirements (especially the flotation separation requirements), the appropriate amount of small steel balls can be added.
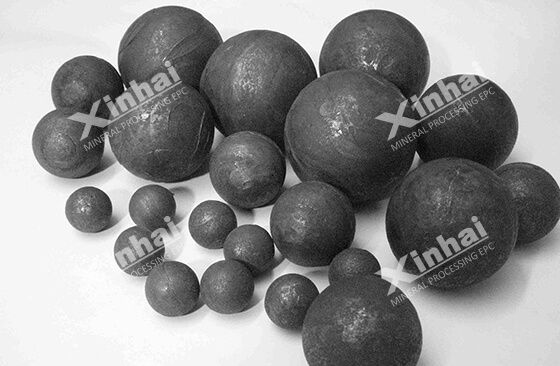
Grinding concentration
The grinding concentration is usually expressed as a percentage of the weight of the ore in the ball mill to the weight of the entire pulp. The thicker the pulp, the greater its viscosity, the less fluidity, and the slower speed through the ball mill.
In general, the pulp concentration depends on the nature of the ore. For coarse ore feeding and processing of ores with high hardness and heavy ratio, the concentrated pulp should be used, whereas dilute pulp should be used. Take the medium speed ball mill as an example, the coarse grinding (product fineness is above 0.15mm) or the heavy ore are ground, the grinding concentration should be larger, about 75-82% (solid). The Fine grinding (product fineness is 0.10-0.075mm) or the ore with small gravity is ground, the grinding concentration should be lower, usually 65-75% (solid).
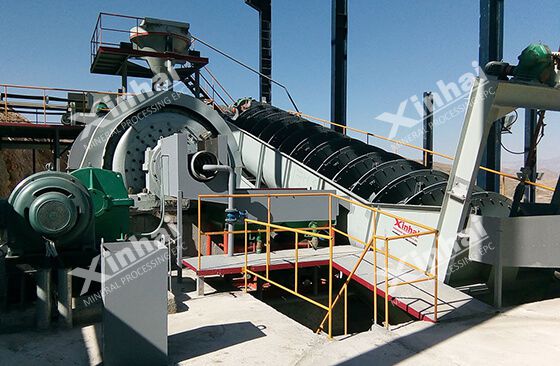
In addition, if there is a small amount of primary slime in the pulp, the dispersant or coagulant can be appropriately added to change the fluidity and stability of the pulp. Commonly, the chemicals are sodium silicate, sodium carbonate, and lime.
Feeding speed
Feeding speed is the amount of ore passing through the ball mill in unit time. When the feeding speed is very low, the amount of ore in the ball mill is small, the grinding efficiency is low, which aggravates the wear and over-grinding phenomenon. With the increase of ore feeding speed, the content of qualified particles in the discharge mineral decreases, the number of qualified particles increases, the specific power consumption decreases, and the grinding efficiency increases significantly. But if the feeding speed exceeds a specific operating system of a quota, the ball mill will be overloaded, and the steel balls, large ore will spit out and the slurry will be poured out. Therefore, the ore feeding must be continuous and uniform, without large fluctuations (avoid more or less).
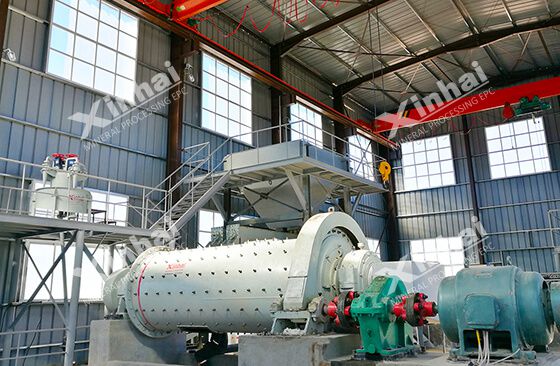
Those are factors that affect the grinding efficiency of the ball mill. In general, achieving the energy-saving and high yield of ball mill is a system engineering, each link is related to each other, but also restrict each other. Only by taking everything into consideration can achieve the ideal grinding effect of the ball mill.