Flotation separation process is a widely used mineral processing process to separate valuable minerals or particles from other materials. There are many influencing factors in the flotation process. In order to ensure a good flotation effect, these flotation influencing factors should be understood. This article will introduce the influencing factors of the flotation process from three aspects: ore characteristics, reagent selection, stirring and aeration of pulp.
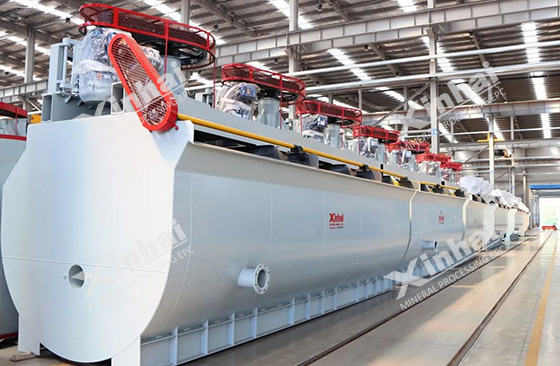
Use the table of contents below to navigate through the guide:
01Influence of Ore Properties on Flotation Separation
The properties of the ore being processed have a significant impact on flotation. Mainly manifested in the following aspects:
1. Ore composition: Some ores may contain valuable metallic minerals, while others may be primarily non-metallic minerals. Differences in the composition of different ores affect the selectivity of flotation, that is, the recovery and purity of specific minerals in the flotation process.
2. Ore particle size distribution: The size of ore particles is related to the bubble-particle collision and attachment during the flotation process. Smaller particles tend to have a larger specific surface area, which is easy to contact and attach to air bubbles, so the flotation effect may be better. Coarser particles may require stronger agitation and larger air bubbles for effective flotation.
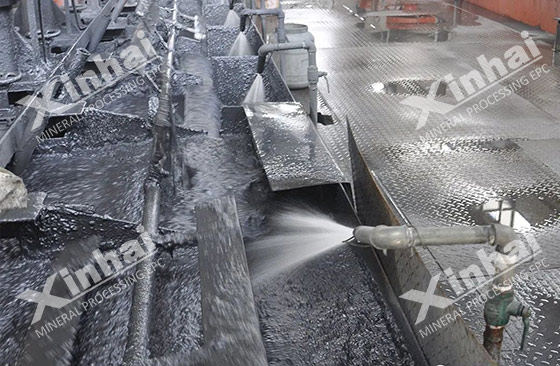
3. Degree of ore dissociation: If the dissociation degree of valuable minerals and gangue minerals is high, that is, they are relatively easy to separate, the selectivity in the flotation process may be better.
4. Ore surface properties: The properties of the ore surface are crucial to the flotation process. Especially the hydrophilic or hydrophobic character of ore particles. Hydrophilic minerals are often difficult to contact and attach to air bubbles, while hydrophobic minerals are more likely to form attachments to air bubbles. By selecting appropriate flotation agents and adjusting flotation conditions, the properties of the ore surface can be changed, thereby affecting the flotation effect.
02Influence of Reagent Selection on Flotation Separation
The selection and dosage of reagents selected and added in the flotation process have a key influence on the flotation effect. The following are some key aspects related to agent selection:
1. Collector selection: used to improve the adhesion of valuable minerals and air bubbles. Different types of ore may respond differently to different collectors. Choosing an appropriate collector can improve the flotation effect and increase the ore recovery rate.
2. Selection of foaming agent: The foaming agent is a kind of agent that can generate and stabilize air bubbles during the flotation process. Choosing a suitable foaming agent can produce bubbles of suitable size and stability, thereby promoting the contact and attachment of ore and bubbles.
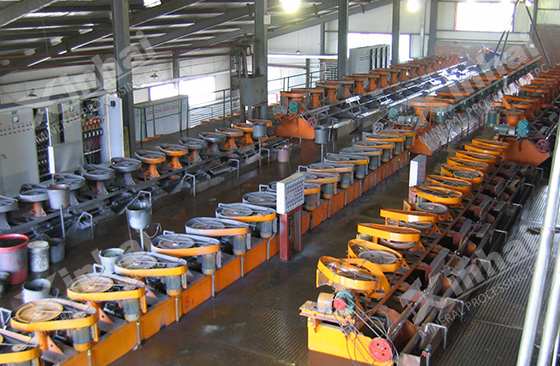
3. Modifier selection: The modifier can adjust the properties of the ore surface and change the interaction between the ore and the air bubbles. By choosing a suitable modifier, the adhesion ability of some minerals and air bubbles can be enhanced or inhibited, and the selectivity of flotation can be improved.
4. Inhibitor selection: Inhibitors are used to inhibit the attachment of certain minerals and air bubbles, so as to better selectively float valuable minerals. Choosing the right inhibitor can reduce the flotation of impurity minerals, thereby improving the grade of valuable minerals.
03Effect of Agitation and Aeration on Flotation Separation
The agitation and aeration of the flotation pulp help the dispersion of air bubbles, promote the attachment of particles to the bubbles, and help to stabilize the formation of foam. Agitation intensity and distribution as well as aeration rate are important parameters for optimization. Agitation and aeration play an important role in the flotation process and have an impact on the flotation effect.
1. Agitation: Agitation helps to disperse air bubbles evenly into the flotation slurry. Stirring can increase the collision chance between air bubbles and solid particles, and promote the adhesion of particles and air bubbles. Stirring can also improve the uniformity of the slurry, avoid agglomeration and sedimentation, thereby improving the efficiency and recovery of flotation.
2. Aeration: Aeration is to inject air or gas into the flotation machine, which will generate air bubbles and interact with the mineral particles in the flotation slurry. Bubbles carry gas and mineral particles separated from water to rise to the liquid surface to form foam. Ventilation can achieve the following effects:
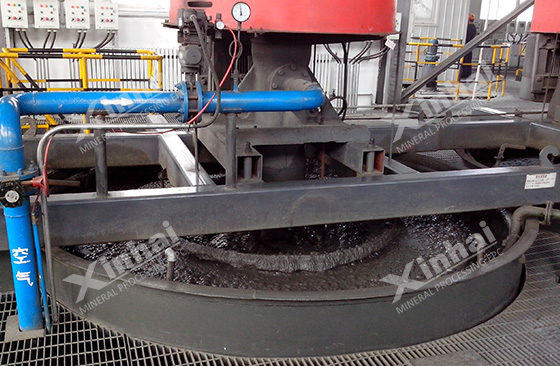
(1) Attachment: After the air bubbles generated by ventilation contact with solid particles, through attachment, the mineral particles are brought to the liquid surface to form foam. Good ventilation helps to increase the chance of contact between air bubbles and particles, thereby improving the flotation recovery rate.
(2) Foam stability: Ventilation affects the stability and persistence of foam. Proper aeration produces stable foam, prevents foam collapse and particle shedding from the foam, and ensures that mineral particles remain in the foam during liquid level rise.
(3) Foam velocity: Ventilation controls the bubble generation rate, thereby affecting the rise velocity of the foam. Proper aeration rate can keep the foam at an appropriate speed, so that the mineral particles have enough time to effectively attach to the air bubbles.
The above are the three factors that affect the flotation separation effect. In actual production, the selection of flotation equipment, the adjustment of pH value, the water quality, and the flotation process will also have an impact on the flotation effect. Therefore, many factors should be considered when designing the flotation beneficiation process. Xinhai Mining suggested to design the ore flotation process flow and equip flotation equipment according to the mineral processing test results, so as to obtain higher flotation effect and improve economic benefits.