In the process of producing zinc, zinc leaching slag will be produced, which contains a large amount of precious metals silver, copper, lead, zinc and other non-ferrous metals. After the silver in the zinc concentrate is roasted and leached in the hydrometallurgical zinc smelting process, almost all of it is enriched in the leaching residue. As precious metals and non-ferrous metal resources become increasingly scarce, comprehensive silver recovery from these leaching residues is one of the solutions. The following will introduce you to several methods for recovering silver from zinc leaching slag.
Use the table of contents below to navigate through the guide:
01Direct leaching method of zinc leaching residue
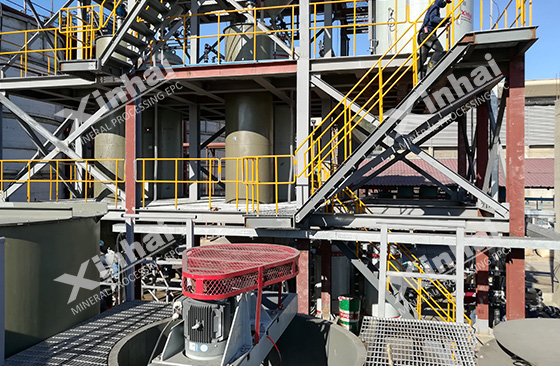
The principle of the direct leaching method is to use certain substances to react with gold, silver and precious metals to generate complex ions of precious metals and enter the solution to achieve separation. According to different chemicals, direct leaching methods can be divided into: cyanide method, thiourea method, chloride salt method, sodium thiosulfate method, etc. Among them, the cyanide method uses highly toxic cyanide, which causes a lot of interference from impurities during the leaching process. It is generally used when processing flotation silver concentrates. Several other methods have the advantages of being non-toxic and fast in leaching.
02Zinc leaching residue pretreatment-leaching method
Different types of zinc leaching slag have greatly different properties and contain harmful impurities that affect the leaching of silver and other valuable metals. Therefore, proper pretreatment and selection of appropriate leaching methods can obtain better indicators. Two methods are listed below:
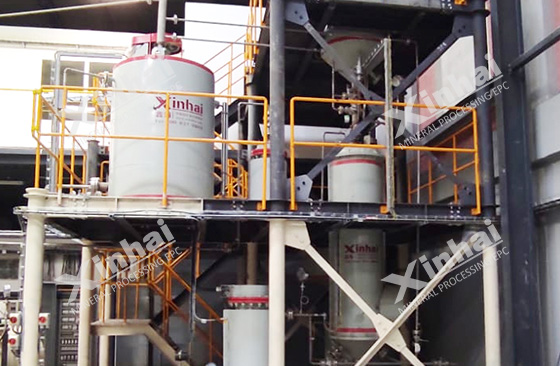
(1) Acid leaching pretreatment-chlorination leaching process: Manganese dioxide and potassium chlorate are used as oxidants when leaching zinc slag, and calcium chloride and sulfuric acid solution are used to leach at a temperature of 90°C. The leaching time is 2 hours.
(2) Sulfation roasting - water immersion dezincification of iron - chloride leaching - cooling and crystallization of lead chloride - lead sheet replacement immersion silver process: zinc leaching residue is sulfated and roasted - water leached and then leached by chlorination, and then cooled and crystallized Coarse silver powder is obtained by replacing lead sheets, and valuable metals such as zinc, iron, and lead in zinc slag are leached with high acid at the same time.
After zinc leaching residue is pretreated, it can be effectively treated and the recovery rate of silver can be increased.
03Zinc leaching residue flotation method
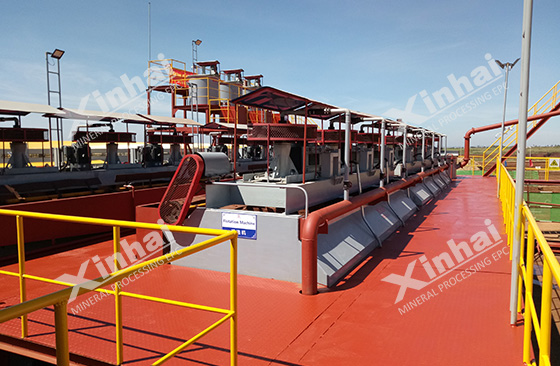
The zinc leaching residue flotation process has a simple process, low equipment requirements, and stable production. Because of these advantages, this process is widely used in mineral processing processes. Depending on the silver content in the zinc leaching residue and the different processes of zinc smelting, different flotation processes and flotation agent combinations can be selected. Flotation can effectively recover other valuable metals from zinc leaching residue. However, it is difficult to recover the soluble galactic vitriol compound-coated silver in the leaching residue by direct flotation. Certain pretreatment is required or combined with the leaching process to improve the recovery index.
04Combined zinc leaching slag selection and smelting method
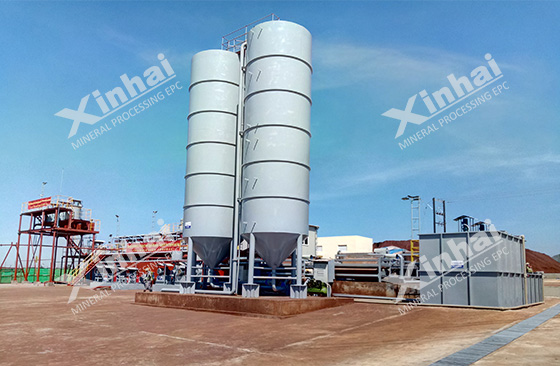
The combined treatment process of beneficiation and smelting has been widely used in actual production. The main methods are: neutral leaching-acid leaching-heated acid leaching-flotation combined process, leaching and flotation combined process, sulfation roasting-flotation combined process, thermal Acid leaching-flotation combined process, etc. Different combined processes are used to process different types of zinc leaching residues. Choosing a suitable combined process can improve the recovery and utilization rate of silver, and other valuable metals can also be comprehensively recovered to a certain extent.
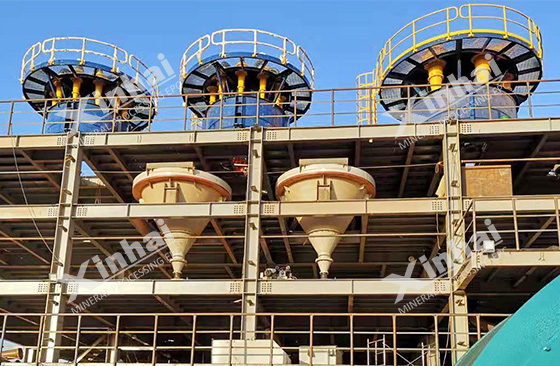
The above are four methods for recovering silver from leaching slag, each of which has its own advantages and disadvantages. Among them, the flotation method is widely used in actual production, but it is necessary to pretreat the zinc leaching residue or increase leaching before flotation, which can improve the comprehensive recovery index of silver. When recovering silver from zinc leaching slag, it is also necessary to select a suitable silver recovery method based on the properties of the leaching slag and the characteristics of the production process. Xinhai Mining recommends conducting mineral processing test analysis to determine the appropriate method of recovering silver. Xinhai Mining can customize a mineral processing plan for you. Welcome to consult.