Tungsten ore beneficiation plays a vital role in the efficient utilization of tungsten resources. Through scientific beneficiation technology, the recovery rate of tungsten ore can be greatly improved and resource waste can be reduced. Wolframite and scheelite are the main types of tungsten ores. Due to their different mineral properties, the ore beneficiation processes are also different. Wolframite is usually processed by combined processes such as gravity separation, flotation, and magnetic separation. Scheelite is usually treated by a combination of gravity separation and flotation to obtain higher concentrate quality because of its complex symbiosis with gangue minerals. These technologies are continuously optimized in practical applications to ensure the maximum utilization of tungsten ore resources. The following article will introduce you to the ore beneficiation technology of scheelite and wolframite to help you understand the beneficiation of tungsten ore.
Use the table of contents below to navigate through the guide:
01Scheelite ore beneficiation technology
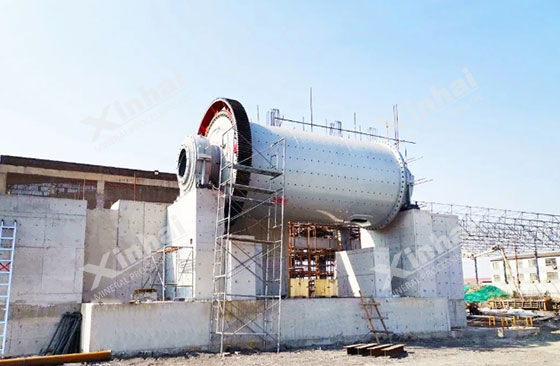
Skarn type is the most common type of scheelite. This type of ore has a finer particle size and is often associated or coexisted with a variety of molybdenum sulfide ores. According to different ore types, scheelite can be divided into two categories: scheelite-quartz type and scheelite calcite-fluorite type. Among them, scheelite-quartz type tungsten ore is easier to recover, while scheelite-calcite-fluorite type tungsten ore is more difficult to recover. The main reason is that the floatability of scheelite is similar to that of its coexisting calcium-containing gangue minerals, and tungsten ore is brittle and is prone to mudification during the crushing and grinding process, resulting in a large amount of tungsten ore lost in tungsten fine mud. For this fine-grained scheelite, domestic and foreign ore beneficiation plants choose to use flotation columns for processing, especially for the ability to efficiently recover micro-fine-grained scheelite, so flotation columns have been widely used in scheelite flotation plants. Its working principle is to use microbubbles to enhance the capture effect of fine-grained minerals, and use foam to wash water to reduce the inclusion of gangue minerals to improve the grade of concentrate.
02Roughing and concentrating of scheelite flotation
The flotation of scheelite can be roughly divided into two parts: roughing and concentrating. The roughing stage is mainly to maximize the recovery rate of scheelite, while the purpose of concentrating is to obtain qualified tungsten concentrate. From this we can see that the flotation process of scheelite requires the formulation of strict roughing and concentrating process flow, and multiple concentrating is required in the process to achieve the expected effect.
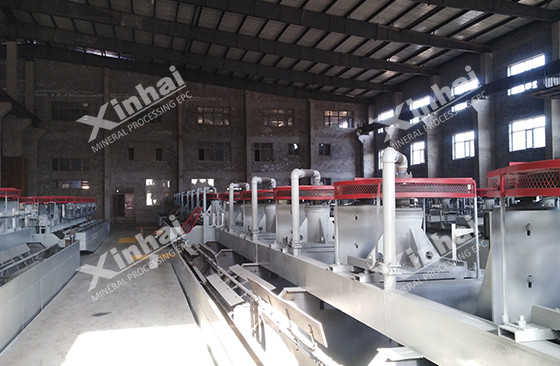
1. Roughing of scheelite: The main purpose is to maximize the recovery of scheelite. The roughing method can be divided into lime flotation and sodium carbonate flotation. Although lime and sodium carbonate are both pH adjusters, their principles are different. Sodium carbonate can be used as a dispersant for slurry while acting as a pH adjuster. Sodium carbonate can also settle metal ions that have an adverse effect on flotation, thereby improving the flotation index of tungsten ore.
2. Concentration of scheelite: The main purpose is to maximize the separation of tungsten ore and gangue minerals and improve the grade of tungsten concentrate. Heating flotation and room temperature flotation are two commonly used flotation and concentration technologies for treating scheelite. The room temperature method is mainly used in quartz vein mines, and the heating method is suitable for treating ores with high calcium content and low tungsten content.
03Wolframite ore beneficiation technology
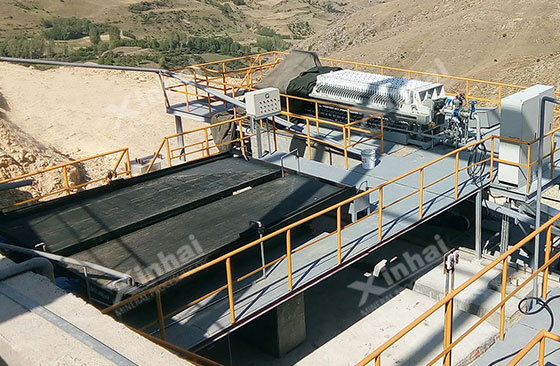
Most wolframite is quartz vein type, and its mineral composition is relatively simple. However, due to the coarse particle size of wolframite, it is an easy-to-select mineral compared to scheelite. Compared with other symbiotic gangue minerals, wolframite has a higher density, so wolframite is generally pre-enriched by gravity separation. The wolframite gravity separation process can be divided into early collection by jigging, tailings discarded by shaking table, multi-stage jigging, and multi-stage shaking table. The above gravity separation process plus the re-grinding of middlings and the separate treatment of wolframite fine mud are the core of wolframite treatment.
In addition, wolframite has weak magnetism and can also be recovered by magnetic separation. Due to the over-exploitation and utilization of wolframite, high-grade and high-grade wolframite is increasingly exhausted, and low-grade wolframite coexists with polymetallics, so the process requirements for the treatment of this kind of wolframite are higher.
04Wolframite fine mud ore beneficiation process
Similar to scheelite, wolframite is brittle and easy to crush. It is easy to be over-crushed during the crushing and grinding process, resulting in the loss of wolframite. The recovery of wolframite fine mud requires a more demanding beneficiation process, which is generally designed around flotation, gravity separation and magnetic separation.
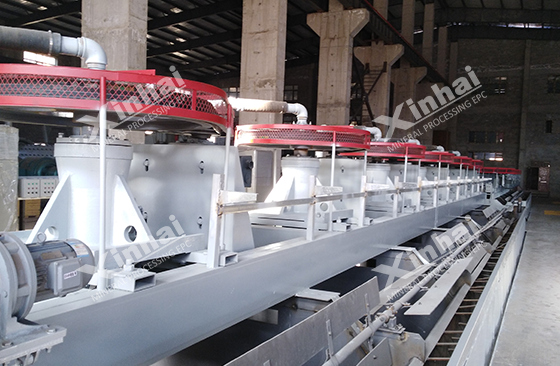
In general, the ore beneficiation processes of scheelite and wolframite have different focuses due to their different mineral properties. Scheelite beneficiation technology mainly relies on flotation columns to process fine-grained scheelite, and adopts strict roughing and concentrating process flow to maximize the recovery rate and concentrate grade. Wolframite, on the other hand, tends to be processed using gravity separation and magnetic separation processes, especially for ores with coarse embedded particle sizes, through multi-stage processes such as jigging, shaking tables and middling regrinding to achieve efficient resource recovery. With the deepening of resource development, it is particularly important to optimize and upgrade these technical means to cope with the increasingly complex low-grade ore processing needs and ensure the full utilization of tungsten ore resources.