Lithium is a valuable element used in various industries, especially in the production of lithium-ion batteries. Spodumene is an important lithium ore, usually found in lithium-rich feldspar deposits, and because spodumene is rich in lithium, it is an important ore for lithium extraction. The process involves crushing ore and then treating it by methods such as gravity separation, flotation or calcination to produce lithium concentrate. These concentrates are further processed to obtain lithium carbonate or lithium hydroxide. With the expansion of the electric vehicle market and the popularity of portable electronic devices in recent years, the importance of spodumene as a lithium resource has increased. This paper mainly introduces the spodumene flotation process and successful case.
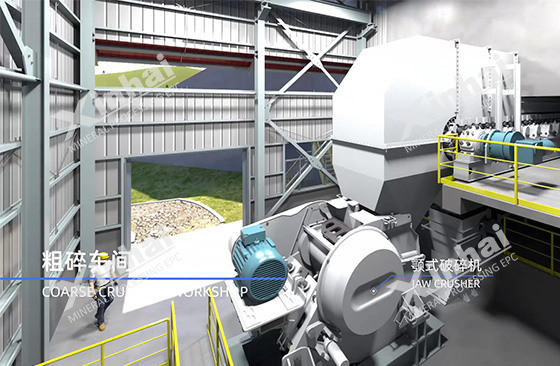
The spodumene flotation process is a method of separating and concentrating spodumene minerals from associated gangue minerals through a flotation process. Flotation is a technique widely used in mineral processing to selectively separate minerals by taking advantage of differences in their physical and chemical properties.
Use the table of contents below to navigate through the guide:
01Spodumene flotation process steps:
1. Crushing and screening: The mined spodumene raw ore is broken into smaller particles for subsequent processing. The crushed spodumene ore needs to be further screened, the oversize material enters the grinding equipment, and the undersize material returns to the crushing system for re-crushing. Such a process can improve the working efficiency of the grinding equipment and avoid over-grinding of the ore.
2. Grinding and classification: The ore after crushing and screening is further ground into fine powder to increase its surface area for effective flotation. In order to improve the flotation efficiency, the grinding products need to be classified before flotation, the overflow returns to the regrinding process, and the bottom flow enters the flotation system for flotation.
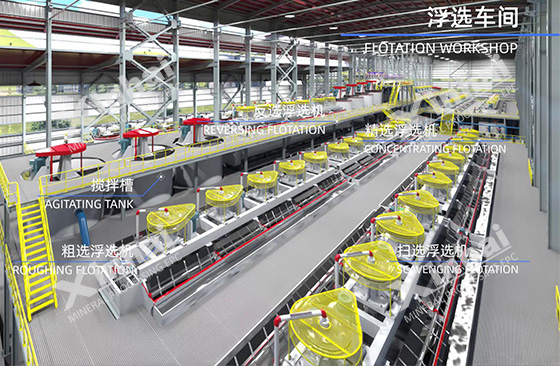
3. Spodumene flotation: the pulp entering flotation needs to be mixed with various reagents to create a good flotation environment. Added reagents include collectors, frothers, etc. Collectors enhance the hydrophilicity (hydrophilicity) of the spodumene particles, while frothers help form a stable froth layer for the flotation process. The slurry after pulping is introduced into the flotation equipment and injected with air bubbles. Spodumene particles with lower hydrophilicity selectively attach to the bubbles and float to the liquid surface to form a foam layer. The froth layer of spodumene particles rising by flotation is taken from the top of the flotation cell.
4. Concentration and dehydration: After flotation, the spodumene concentrate needs to be concentrated and dehydrated to remove most of the water. At this stage, thickeners, filters, filter presses, etc. can be used.
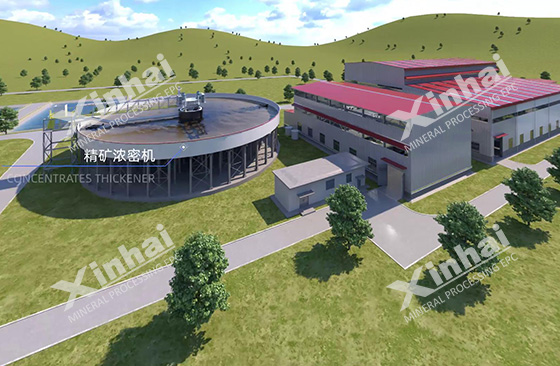
5. Further processing: Spodumene concentrate may undergo additional processing steps, such as heat treatment or chemical conversion, to produce lithium compounds such as lithium carbonate or lithium hydroxide, which are used in various applications, including battery manufacturing.
The above are the common steps of spodumene flotation process. The specific spodumene beneficiation flotation process may vary due to ore composition, product specification requirements, and flotation equipment and reagents used by different mining enterprises.
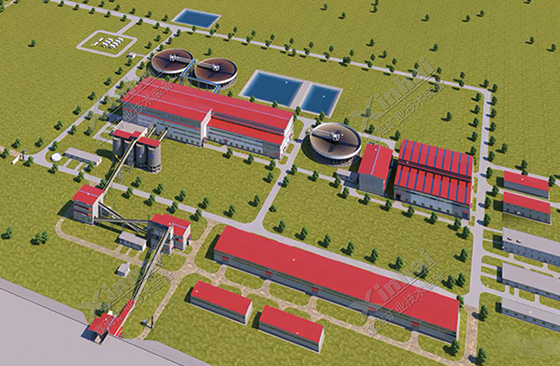
02Successful case: Zimbabwe 2 million TPA spodumene concentrator of Xinhai Mining
Recently, the Zimbabwe BIKITA 2 million TPA spodumene concentrator project undertaken by the mine manager of Xinhai has successfully entered the trial production stage. The process used in this project is spodumene flotation. The following will give you a brief introduction to the spodumene flotation process of this project:
The raw ore enters the crushing process of "one stage of coarse crushing, one stage of medium crushing and one stage of fine crushing" through the feeder for processing. The crushed product enters the two-stage screening process for screening, and the under-screen product enters the wet ball mill for grinding. Due to the closed circuit between the screening system and the crushing system, the product on the screen enters the crushing system for further processing. The grinding and classifying system of this project adopts the technological process of "one-stage grinding and one-stage classification". The classified products need to enter the process of "one-stage magnetic separation and two-stage desliming" for impurity removal. The magnetic separation equipment adopts magnetic drum, and the desliming equipment is desliming cyclone. The underflow part of the cyclone enters the flotation system for separation. The flotation system of this project is designed as a process of "one-stage reverse flotation, one-stage positive flotation roughing, three-stage scavenging and three-stage concentrating". After flotation, the spodumene concentrate enters the dehydration system of "thickener+filter press" for concentration and dehydration. The tailings produced in each stage of the spodumene flotation process will enter the tailings thickener for dehydration, the overflow water will be recycled, and the underflow will be discarded as tailings.
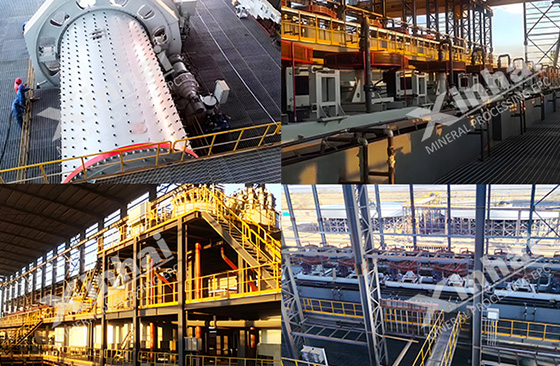
This project was customized and designed by Xinhai Mining according to the properties and needs of the customer's spodumene ore. It took only one year from signing the contract to equipment installation and successful trial operation. During the construction of this project, Xinhai Mining coordinated and cooperated with various departments to overcome difficulties in overseas transportation, installation, and external environment, and deliver the project on time, once again demonstrating the ability and strength of Xinhai Mining in mine mineral processing design, equipment production, installation, commissioning, production and other aspects.