The flotation process is one of the commonly used separation methods in the mineral processing process. In the flotation process, there are many influencing factors, such as ore particle size, slurry concentration and temperature, chemical system, equipment selection and other factors. In order to obtain higher flotation indicators, the mineral processing plant should conduct mineral processing test analysis based on the properties and characteristics of the ore to determine a reasonable mineral processing plan. However, understanding how these factors affect the flotation process is also an important part of optimizing the flotation process. The following will introduce to you the effects of slurry concentration and temperature during flotation.
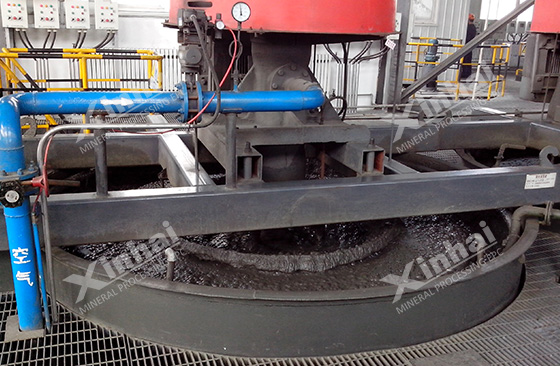
(flotation process)
Use the table of contents below to navigate through the guide:
01Effect of pulp concentration on flotation process
Slurry concentration is an important process parameter in the flotation process and can directly affect the following technical and economic indicators.
1. Recovery rate: There is an obvious regularity between the pulp concentration and recovery rate of mineral flotation. When the slurry concentration is low, the concentrate recovery rate is low, and as the slurry concentration increases, the recovery rate will also increase. When the appropriate slurry concentration is reached, the recovery rate will decrease. The main reason is that too thick or too thin slurry will worsen the aeration conditions of the flotation machine.
2. Concentrate quality: In general, the concentrate obtained by flotation of thinner slurry has higher quality, while the concentrate obtained by flotation of thicker slurry has lower quality.
3. Dosage of chemicals: In order to obtain better flotation indicators, the slurry needs to maintain a certain concentration of chemicals during the flotation process. When the slurry concentration is high, the concentration of chemicals in the liquid phase increases, and the amount of chemicals used per ton of ore can be reduced. If the slurry concentration is small, the amount of chemical used per ton of ore needs to be increased.
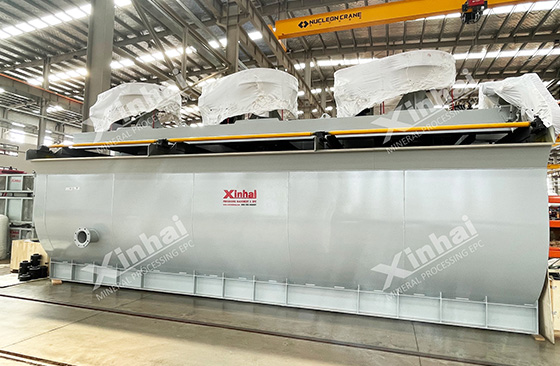
(flotation equipment)
4. Production capacity of flotation equipment: As the slurry concentration increases, the production capacity of the flotation machine will also increase.
5. Flotation time: The flotation time will be extended as the slurry concentration increases. This is beneficial to improve concentrate recovery rate.
6. Water and electricity consumption: The greater the slurry concentration, the less water and electricity consumption per ton of ore will be processed.
In order to obtain a suitable slurry concentration, in addition to the above factors, the ore properties and specific flotation conditions should also be considered. The general principle is: when flotating minerals with high density and coarse particle size, use slurry; when flotating minerals and slimes with small density and fine particle size, use dilute slurry. Concentrated slurry is used during roughing operation, so as to obtain high recovery rate and reduce chemical consumption. For the beneficiation operation, dilute slurry is used to improve the quality of the concentrate.
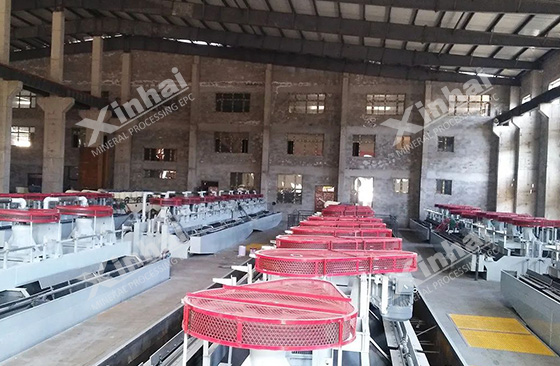
(flotation process)
02Effect of slurry temperature on flotation process
The flotation process is generally carried out at room temperature, but there are also situations where the temperature of the slurry needs to be adjusted, such as chemical property requirements or special process requirements.
1. Heated flotation of non-sulfide ores: When flotating non-sulfide ores such as fluorite and apatite, certain collectors that are insoluble and whose solubility changes with temperature changes are used, such as fatty acids or fatty amines, etc. drug. In order to improve the solubility and capture capacity of these drugs in water, it is necessary to increase the slurry temperature to improve the selectivity during the flotation process, which can save a lot of chemicals and obtain high recovery rates.
2. Heated flotation of sulfide ore: In actual production, the heated flotation process of sulfide ore has been widely used. This process mainly takes advantage of the different oxidation rates on the surfaces of various sulfide ores to expand the differences in floatability of the minerals to be sorted. Although the heating process has many advantages, it consumes a lot of heat energy during the treatment process. Therefore, when choosing this process, you should study it in advance and consider whether it is suitable from economic and technical aspects, thereby reducing unnecessary production costs.
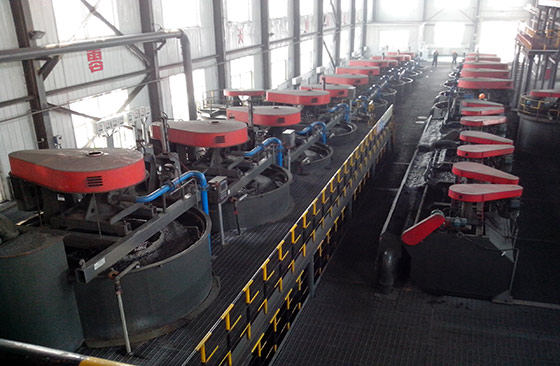
(flotation equipment)
The above content is the influence of slurry concentration and temperature on the flotation process. Due to the different characteristics and properties of different ores, the slurry concentration and temperature required in the mineral processing process are different, and need to be analyzed and adjusted according to specific production conditions. Xinhai Mining recommends that the ore dressing plant conduct a beneficiation test and select a reasonable flotation process based on the test results, which can better utilize raw ore resources and improve concentrate recovery rate and economic indicators.