Pyrite ore is widely used in sulfuric acid production, chemical industry and other fields. With the continuous development of pyrite resources, how to efficiently and economically process different types of pyrite ores has become the focus of mining companies. The selection of mineral processing methods is mainly based on the selectivity characteristics of the ore, so this article will discuss the research progress of pyrite mineral processing and the application of different mineral processing methods.
Use the table of contents below to navigate through the guide:
01Separability analysis of pyrite ore beneficiation
The separability judgment of pyrite ore mainly depends on the volume and mass difference between useful minerals and gangue minerals in the ore. When the separability judgment coefficient is greater than 1.75, the ore is considered to be easy to be separated. This type of ore generally has nodule-like and dendritic structures, which are easier to be effectively separated by gravity separation. For these ores, gravity separation is not only simple in process, but also has low infrastructure investment, low cost, easy operation, and less pollution to the environment. Therefore, it is widely used in most coal-based pyrite beneficiation plants in my country.
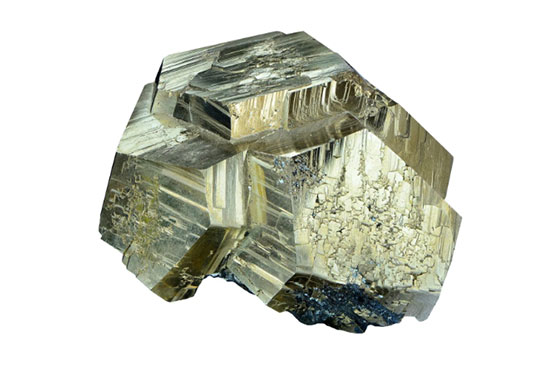
02Common pyrite ore beneficiation methods
The selection of pyrite ore beneficiation methods depends on the properties of the ore and its distribution characteristics. According to the specific conditions of the ore, common beneficiation methods include gravity separation, flotation and gravity-flotation combined process. The following will discuss in detail the applicable conditions and process design of each beneficiation method.
1. Single gravity separation method
For coarse-grained pyrite ores with large volume-mass differences, gravity separation is usually the most effective choice. Gravity separation mainly separates minerals by the density difference of mineral particles. This method is suitable for processing easy-to-separate ores, and has the advantages of simple process and low cost. Common process flows include two-stage closed-circuit crushing-classification or non-classification jigging.
In actual operation, the ore is sorted by a jig after the second stage of crushing. For unevenly coarse and fine embedded ores, fine separation can be carried out after jigging using equipment such as shaking tables, heavy medium cyclones, spiral chutes, centrifugal concentrators and belt chutes. Through this process, qualified concentrates can usually be obtained.

2. Single flotation method
When the pyrite ore is in a fine-grained state, the separation efficiency of the gravity separation method is often low, and flotation can be considered at this time. The flotation method uses the difference in the surface properties of the mineral to separate the target mineral from the gangue through the action of the reagent. This method is usually suitable for processing hydrothermal, late contact metasomatic and metamorphic pyrite with finer embedded particles.
The advantage of the flotation method is that it can efficiently separate fine-grained ores, but due to the use of reagents, the cost of the flotation method is relatively high, so a comprehensive comparison of technical and economic benefits is required when applying it.
3. Gravity-flotation combined process
For pyrite ores with unevenly distributed particle sizes, it is difficult to achieve efficient separation by a single gravity separation method or flotation method. In this case, the gravity-flotation combined process is a common choice. Preliminary separation of coarse-grained ores by gravity separation and then treatment of fine-grained ores by flotation can achieve higher recovery rates and concentrate quality.
This method is widely used in actual production, especially for deposits containing more fine-grained impregnated ores. Through the gravity-flotation combined process, it is possible to save costs while improving mineral processing efficiency and obtaining qualified concentrate products.
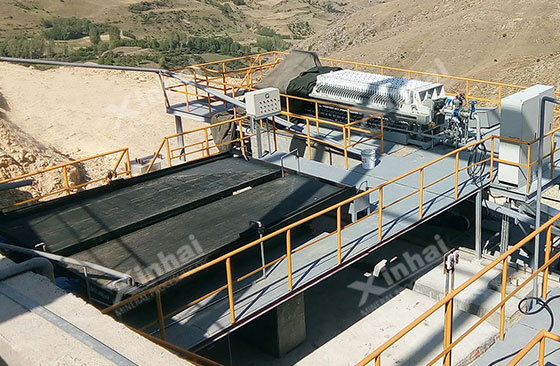
03Typical pyrite ore beneficiation process flow
In pyrite ore beneficiation, common process flow designs include the following:
- Gravity separation process for coarse-grained ore: generally two-stage closed-circuit crushing is used, followed by separation by a jig. For ores with uneven distribution of coarse and fine particles, shaking tables, heavy medium cyclones and other equipment can be added for further separation.
- Flotation process for fine-grained impregnated ore: when the ore is finely interpenetrated, flotation is the most effective option. Flotation can maximize the recovery rate of pyrite by adjusting the type and dosage of reagents.
- Gravity-flotation combined process: This process is suitable for ores with uneven particle size. By first gravity separation and then flotation, the separation and enrichment of minerals can be achieved more efficiently.
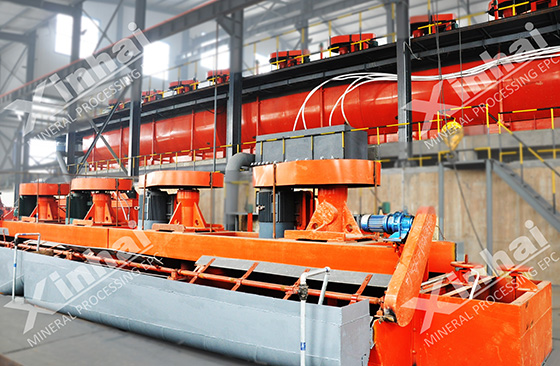
The selection of pyrite ore beneficiation methods must be comprehensively analyzed based on the ore's dissemination characteristics and technical and economic benefits. In the treatment of coarse-grained ores, gravity separation is still the main choice due to its simple process, low cost, and environmental friendliness. For fine-grained impregnated ores, flotation can provide higher recovery rates, especially when reagent conditions are optimized. For ores with uneven dissemination particle sizes, gravity-flotation combined processes can strike a balance between cost and recovery.
With the continuous development of technology and the improvement of mineral processing technology, pyrite ore beneficiation technology still has a lot of room for improvement in the future. When selecting a process flow, the beneficiation plant should fully consider the specific characteristics of the ore and the economic benefits to ensure the feasibility and efficiency of the process.