The original rutile ore has the characteristics of complex components, close intercalation relationship, and fine particle size distribution, which makes its mineral processing technology complicated. It often requires a combined beneficiation process consisting of gravity separation, magnetic separation, flotation and other processes to obtain high-grade rutile concentrate products. The following will introduce the mineral processing technology of these rutile mines.
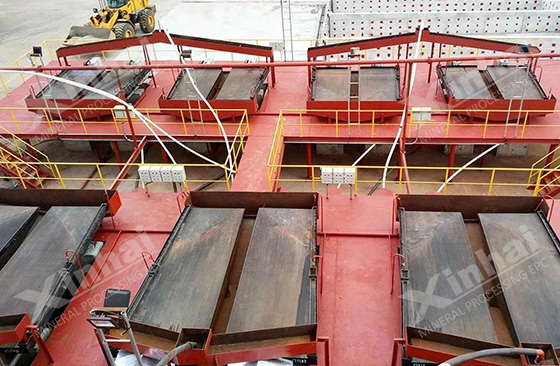
Use the table of contents below to navigate through the guide:
01Rutile ore gravity separation technology
Gravity separation technology is generally based on the density difference between various minerals, which is low in cost and less in environmental pollution. The treatment of placer-type rutile ore generally adopts gravity separation technology, which is a common technical means for sorting and enriching primary rutile ore. During gravity separation, equipment such as spiral chute is often used in roughing operation to discard most of the ore slime. Gravity separation equipment shaking table can separate quartz, tourmaline, garnet and other gangue minerals as tailings, and rutile in the ore and concentrate of the shaking table.
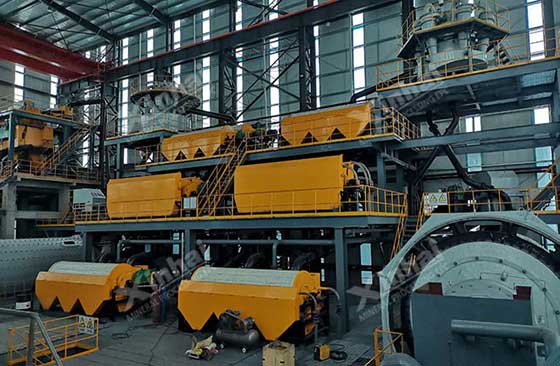
02Rutile magnetic separation technology
Magnetic separation mainly uses the magnetism of minerals to separate magnetic minerals from non-magnetic minerals and strong magnetic minerals from weak magnetic minerals through magnetic separation equipment. During magnetic separation, magnetically conductive minerals, such as ilmenite, limonite, hematite, magnetite, etc., will be separated from nonmagnetically conductive rutile minerals. In production practice, rutile magnetic separation technology is often combined with other mineral processing methods. Magnetic separation can be effectively used for pre-selection and concentration of rutile ore.
03Rutile ore electric separation technology
Based on the conductivity of minerals, the separation method based on the different conductivity of mineral surfaces is electro-separation technology. Ore silicate, zircon, and white titanium are non-conductive, and electro-separation technology can easily and effectively separate the conductive mineral rutile and non-conductive minerals, improve the grade of the concentrate and reduce the impurity content.
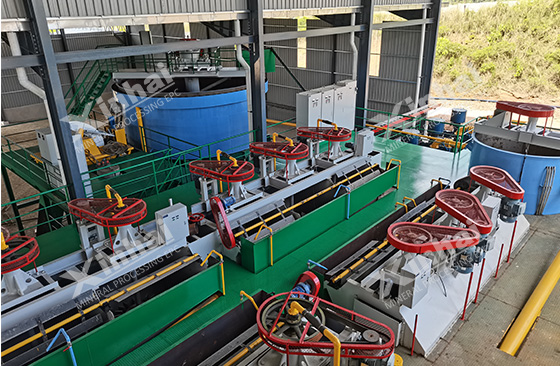
04Rutile ore flotation technology
It is an effective method for sorting fine-grained rutile and reducing metal loss during flotation. For primary rutile mines with fine ore particle size distribution and tight gangue minerals, the combined process of gravity separation, electric separation and magnetic separation cannot be used. Carboxylic acid, benzyl arsenic acid, styrene phosphonic acid, alkyl amine, dimethyl phosphonic acid, alkyl-hydroxy diphosphonic acid, alkyl hydroxamic acid, salicylic hydroxamic acid, etc. are collectors for rutile. Benzylarsinic acid is an effective collector for rutile flotation, and its selectivity is better than that of fatty acid collectors. It has a strong collection effect on rutile, no collection on calcium-containing minerals, and poor collection on garnet. Regulator sodium fluorosilicate, rutile and garnet can be separated, but the disadvantage is that it is expensive and highly toxic. Alkylamine bismethyl phosphonic acid has low toxicity and strong collection ability to rutile, so it can be used as a substitute for benzyl arsenic acid. Sodium hexametaphosphate is used as a regulator instead of sodium fluorosilicate to achieve efficient and pollution-free flotation.
05Rutile ore pickling technology
Because rutile concentrate products require S≦0.05%, P≦05%, and require TiO2 content to exceed 87.5%. Due to the joint separation of redstone ore through gravity separation, magnetic separation, electric separation and flotation, there are still impurity minerals such as silicate, carbonate and iron minerals adhered to the edges and cracks of redstone. As a result, its crude concentrate rutile single mineral content is only above 60%. In order to remove these impurities and improve the quality of the concentrate, a pickling process is required.
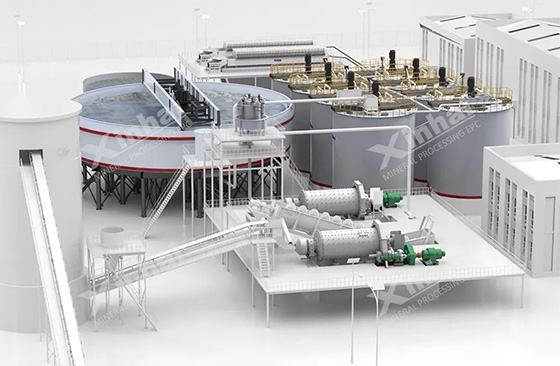
The above content is the beneficiation technology of rutile ore. Due to the different properties of the ore, the beneficiation technology of rutile ore is also different. Xinhai Mining recommends mineral processing tests to determine the appropriate rutile mineral processing plan. Xinhai Mining can provide you with mining services including mineral beneficiation tests, mineral processing plan design, equipment manufacturing, installation and commissioning, and mine management and operation. Welcome to leave a message for consultation.