The iron ore resources in the world are increasingly scarce, and the number of high-grade iron ores that can be directly beneficiated is gradually decreasing. The current existing iron ore resources are mainly low-grade, fine-grained, and complex mineral composition hematite. The grade of the hematite concentrate usually processed by the anion reverse flotation process in the concentrator can reach about 65%, but the grade of the tailings is as high as 16%-20%, indicating that hematite resources are wasted. Therefore, improving the concentrate recovery rate of fine hematite is an important way to improve the comprehensive utilization rate of iron ore resources. This article will introduce the difficulties of reverse flotation of fine-grained hematite and its influencing factors.
Use the table of contents below to navigate through the guide:
01Difficulties in reverse flotation of fine-grained hematite
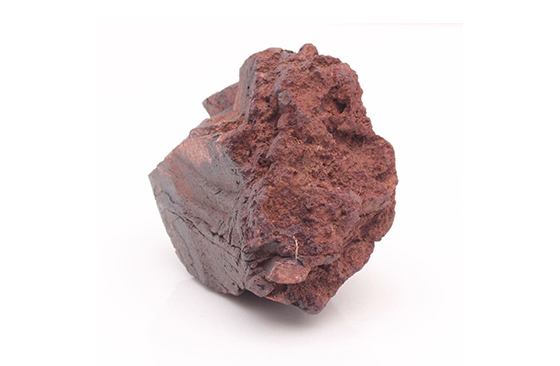
The main reasons why fine-grained hematite is difficult to float are as follows:
1. Small amount of minerals: Due to the small mass of fine-grained minerals, it is difficult for hydrophobic mineral particles to adhere to the bubble surface to form mineralized bubbles. However, once the fine powdered gangue mineral is attached to the surface of the bubble, it is difficult to fall off. In addition, fine-grained gangue minerals easily enter the foam layer with rising water flow to form inclusions.
2. Large specific surface area: The large specific surface area of fine-grained minerals leads to serious non-selective agglomeration between gangue mineral particles and useful mineral particles. As the dosage of flotation reagents increases, the amount of medicaments adsorbed on the surface of mineral particles also increases, reducing selectivity.
3. Fast oxidation rate: Sulfide minerals oxidize quickly and their solubility increases, which increases the number of ions in the slurry. The chemical changes of the slurry solution during the flotation process become complicated, and the interface properties of the mineral particles and various electrical properties are difficult to control.
4. High foam viscosity: Foam has high viscosity, strong stability, and weak "secondary enrichment" effect, making it difficult to handle foam products.
By overcoming the above difficulties, the recovery efficiency of fine-grained hematite can be improved, thereby improving the comprehensive utilization rate of iron ore resources.
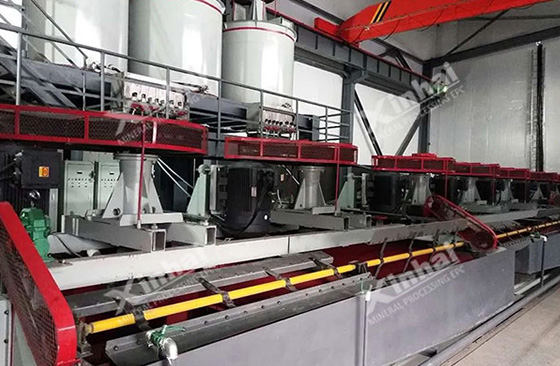
02Factors affecting hematite reverse flotation
During the hematite flotation process, various factors have a significant impact on the flotation effect. The following is a detailed analysis of the impact of collector dosage, inhibitor dosage, activator dosage, stirring intensity, pH value and slurry concentration on hematite flotation:
1. Effect of collector dosage on hematite flotation
Collecting agent is an agent used to increase the hydrophobicity of minerals during the flotation process. Its dosage directly affects the recovery rate of hematite and the grade of concentrate. An appropriate amount of collector can significantly improve the flotation recovery rate of hematite, because the collector can hydrophobicize the surface of hematite, making it easier for bubbles to adhere and float. Excessive collector will cause a large amount of foam in the slurry, which not only consumes the agent, but may also cause co-floating of other minerals, resulting in a reduction in concentrate grade. Insufficient collectors will lead to insufficient hydrophobicity on the hematite surface, poor flotation effect, and low recovery rate.
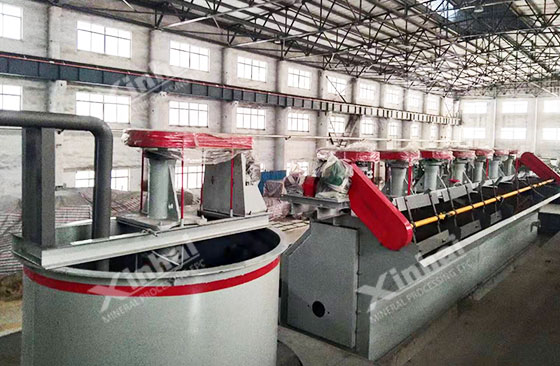
2. Effect of inhibitor dosage on hematite flotation
Inhibitors are agents used to inhibit the flotation of gangue minerals or other impurity minerals. Adding an appropriate amount of inhibitors can help improve the concentrate grade by inhibiting the flotation of gangue minerals (such as quartz), making it easier to separate hematite from them. Excessive inhibitor will inhibit the flotation of hematite itself, resulting in lower recovery rate. If the inhibitor is insufficient, the gangue minerals will not be effectively inhibited, resulting in an increase in impurity content in the concentrate and a decrease in grade.
3. Effect of activator dosage on hematite flotation
Activators are used to enhance the flotation properties of minerals. An appropriate amount of activator can improve the flotation activity of hematite and increase the recovery rate. Excessive activator may cause other impurity minerals to be activated, affecting the concentrate grade. Insufficient activator will lead to insufficient hematite surface activity and reduced flotation recovery rate.
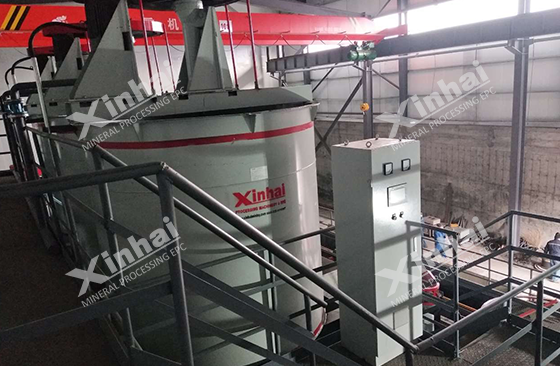
4. Effect of stirring intensity on hematite flotation
Stirring intensity affects the dispersion of slurry, the contact between mineral particles and chemicals, and the formation of bubbles. Appropriate stirring intensity helps to uniformly disperse mineral particles in the slurry, promotes contact between the agent and the mineral surface, and improves flotation efficiency. Too high agitation intensity will cause the slurry to be too disordered and increase bubble collapse, which is not conducive to the floating of hematite. When the stirring intensity is insufficient, the contact between mineral particles and chemicals in the slurry is insufficient, the flotation efficiency is low, and the recovery rate is reduced.
5. Effect of pH value on hematite flotation
The pH value affects the surface charge of minerals, which in turn affects the adsorption of collectors and the flotation behavior of minerals. When the slurry is within a suitable pH range, hematite has a better flotation effect, and usually the flotation effect is better in the neutral to weakly acidic or weakly alkaline range.
If the pH value is too high or too low, it will affect the effect of the collector and the electrical properties of the mineral surface, resulting in poor flotation effect and reduced recovery rate.
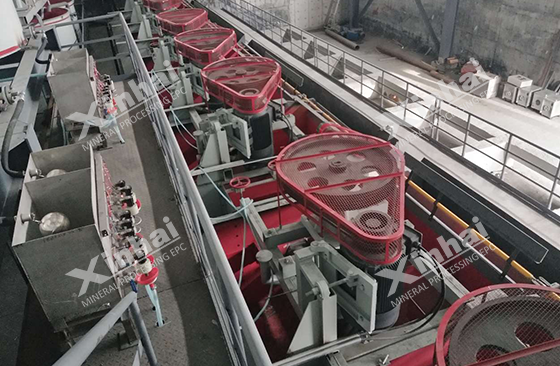
6. Effect of pulp concentration on hematite flotation
Slurry concentration affects the collision opportunities of mineral particles and the distribution of bubbles. Appropriate slurry concentration is conducive to the effective collision and attachment of mineral particles and bubbles, improving flotation efficiency and recovery rate. When the slurry concentration is too high, the viscosity of the slurry increases, the bubble movement is blocked, the mineral particles are difficult to float, and the flotation efficiency is reduced. When the slurry concentration is too low, the chances of collision between mineral particles and bubbles are reduced, which also leads to a reduction in flotation efficiency and recovery rate.
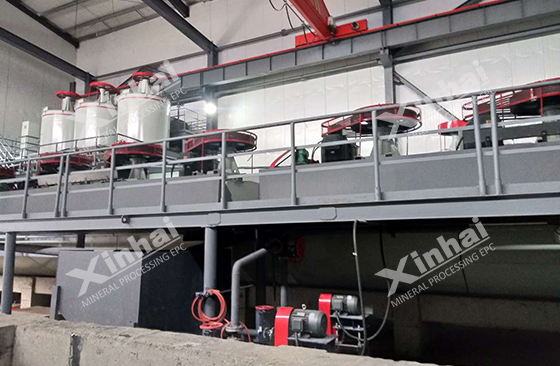
The above content is a brief introduction to the difficulties in fine hematite reserve flotation and the factors that affect the flotation process. In the hematite flotation process, overcoming the difficulties in the mineral processing process and controlling the above factors is the key to achieving high recovery and high precision. The key to ore grade. Therefore, hematite beneficiation testing is an important means to determine the optimal conditions for each factor. Xinhai Mining can provide you with a series of services including mineral processing testing, mineral processing plan design, and complete equipment production, manufacturing, transportation, and installation. Welcome to consult .