Manganese has been widely used in modern industrial fields such as iron and steel, metallurgy, and machinery due to its various valence states and excellent physical and chemical properties. With the gradual shortage of manganese resources, it is imperative to improve the recovery of manganese in raw materials. Manganese carbonate is one of the main raw materials for recovering manganese. At present, the beneficiation process of manganese carbonate ore mainly includes ore washing, gravity separation, magnetic separation, flotation, leaching and combined processes. The following will introduce the process for mineral extraction of manganese carbonate ores.
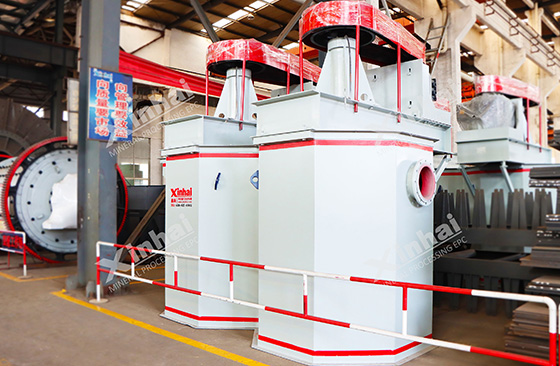
Use the table of contents below to navigate through the guide:
01Manganese carbonate ore washing process
Ore washing is a process of removing slime on the surface of ore by means of hydraulic or mechanical cleaning, and it is a preparation work before ore crushing or sorting. Its purpose is to improve the grade of selected minerals and reduce the impact of ore slime on subsequent operations. Because manganese carbonate ore is brittle, easy to muddy and coexist with clay minerals, it generally needs to be washed before sorting. The ore washing is generally set after the coarse crushing of the ore, which can avoid the problems of material agglomeration in the crushing bin and material blockage in the fine crusher. Mineral washing equipment generally includes hydraulic washing screens, vibrating screens, cylinder washing machines and slot washing machines.
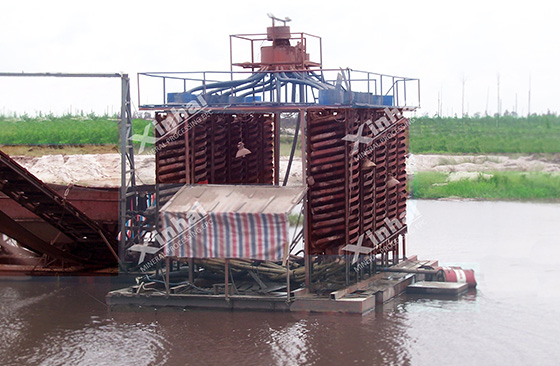
02Manganese Carbonate Gravity Separation Process
The principle of gravity separation is that different mineral particles have different densities, and their falling speeds in the medium are different, which can realize separation according to density. Gravity separation has the characteristics of low cost, wide particle size and low pollution of processed minerals. Generally, the density of manganese carbonate minerals is relatively high, and the density of its associated gangue minerals is relatively low, which can be separated by gravity separation. For carbonate minerals such as calcium rhodochrosite and manganese calcite, dense medium hydrocyclones can be used for classification. After the graded products are washed, they enter the jig machine for gravity separation. But sometimes a single gravity separation process cannot obtain satisfactory beneficiation indicators, and it needs to be combined with other processes, such as magnetic separation and flotation. The equipment that can be used for gravity selection is heavy medium separator, shaker, jig, spiral chute, cyclone and centrifuge, etc.
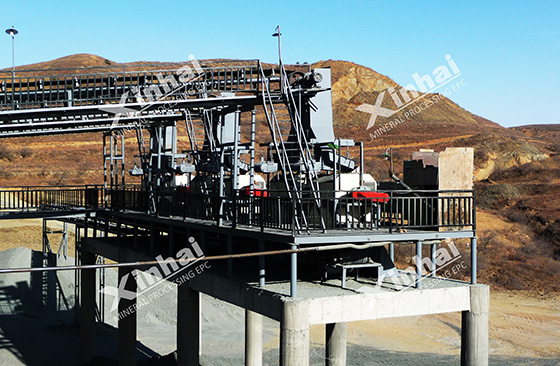
03Manganese Carbonate Magnetic Separation Process
Manganese carbonate has weak magnetic properties, and most of the associated gangue minerals are non-magnetic silicate minerals. Therefore, strong magnetic separation can be used for the enrichment of manganese carbonate. Magnetic separation has the advantages of small footprint, low energy consumption, low cost, economy and environmental protection. Different magnetic separation methods can be used for different types of manganese carbonate ores. For example, wet weak magnetic separation can be used for roughing to process high-iron manganese carbonate, and then high-gradient strong magnetic separation can be used to sweep the rough concentrate, so that the target mineral iron and manganese can be recovered separately. When dealing with high-sulfur carbonate ores, the main gangue minerals are dolomite, pyrite, etc., and the strong magnetic separation process will get better beneficiation indicators. When dealing with low-grade manganese carbonate ore, a high-gradient magnetic separator can be used to perform a rough and sweep process. Magnetic separation equipment generally includes dry magnetic separator, wet magnetic separator and high gradient magnetic
separator.
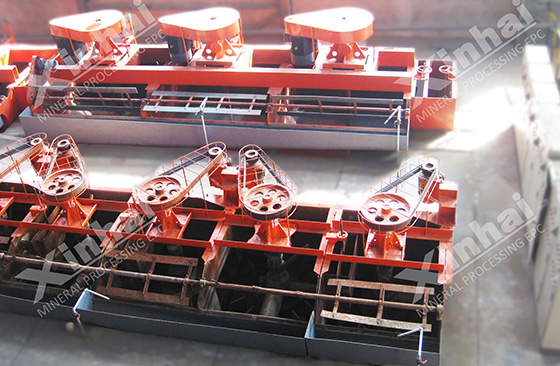
04Manganese Carbonate Flotation Process
Manganese carbonate ore has many associated gangues and complex components, and its embedded particle size is finer, so the flotation process can be selected. The flotation process can effectively enrich the fine-grained manganese carbonate. Generally, positive flotation is used to treat manganese carbonate ore. In the flotation of manganese carbonate ore, a combination of reagents is generally used in combination, so that on the basis of clear target minerals and gangue minerals, different characteristics of drugs can be used in a targeted manner to improve the flotation index.
05Manganese Carbonate Leaching Process
Leaching is mainly to use chemical methods to change the properties of minerals, so as to carry out comprehensive recycling of minerals. The leaching process of manganese carbonate mainly includes pre-roasting leaching, direct acid leaching and microbial leaching.
Pre-roasting and leaching: It is mainly used for the recovery of high-priced manganese resources. The principle is to reduce high-priced manganese to low-priced manganese, and then recover the manganese element in the state of ions during leaching.
Direct acid leaching: A process in which acid acts directly on manganese carbonate ore and then leaches manganese. When pickling directly, it is necessary to pay attention to the temperature, solid-to-liquid ratio, pickling time and stirring intensity during pickling.
Microbial leaching: microorganisms directly or indirectly act on the target minerals to improve the recovery effect of the target minerals.
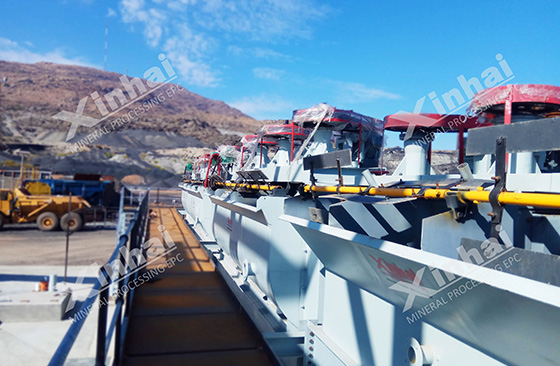
06Manganese carbonate combined beneficiation process
For the development and utilization of lean manganese carbonate ore, the requirements for beneficiation technology are higher, and sometimes a single beneficiation process cannot obtain a good concentrate index, and then a variety of beneficiation processes are required. When the crystal grain size of manganese minerals is fine and closely associated with gangue minerals, magnetic separation-flotation separation process can be selected. Sulfuric acid leaching of the concentrate after flotation can increase the overall recovery of manganese. If the raw ore is high carbonate manganese ore, according to the magnetic and buoyancy differences between the target mineral and gangue mineral, a combined magnetic separation-flotation process can be used. The combined beneficiation process can realize the complementary advantages of multiple single beneficiation processes and improve the comprehensive beneficiation index. In addition, the combined process can also improve the recycling of associated useful minerals and improve the utilization rate of resources.
The above is a brief introduction of the process for mineral extraction of manganese carbonate ore. Depending on the nature of the ore, different beneficiation processes can be used. Xinhai Mining suggests that before determining the beneficiation process, the beneficiation test and analysis of the ore can be carried out, and the suitable beneficiation process of manganese carbonate ore can be determined according to the test results. Xinhai Mining can customize manganese ore beneficiation process, complete set of beneficiation equipment and follow-up equipment installation and use training for you. If necessary, welcome to consult.