Copper is a vital metal with applications in everything from electrical wiring to building materials. Meeting growing copper demand requires efficient extraction of copper from deposits. In this article, we’ll introduce the methods and equipment used in the beneficiation process to effectively extract valuable copper content from the ore.
Use the table of contents below to navigate through the guide:
01Copper ore beneficiation: crushing and grinding
The crushing and grinding processes in copper ore beneficiation play a key role in improving the availability and quality of copper ore. This process is explained in detail below:
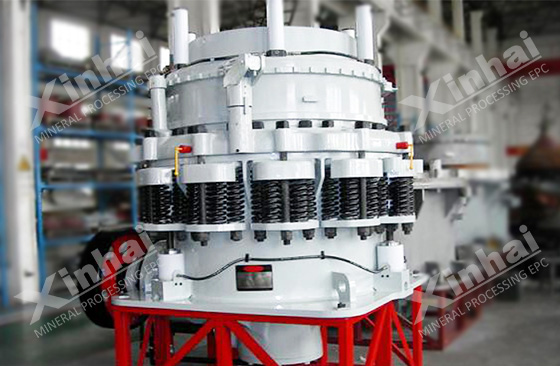
(cone crusher)
In order to extract copper concentrate, raw ore needs to be crushed and ground into fine particles. Crushing and grinding are important steps in the copper ore beneficiation process, further improving the availability and quality of raw ore.
Crushing: It is the first step in copper ore beneficiation. Raw ore usually appears in lumps or large blocks and needs to be crushed to complete the initial dissociation of the concentrate to facilitate subsequent processing. Commonly used crushing equipment mainly includes jaw crusher and cone crusher. The jaw crusher mainly uses a movable jaw plate to crush the ore into smaller block particles and is suitable for coarse crushing. The cone crusher mainly squeezes and crushes the ore through a conical crushing head, and is mainly used for fine crushing.
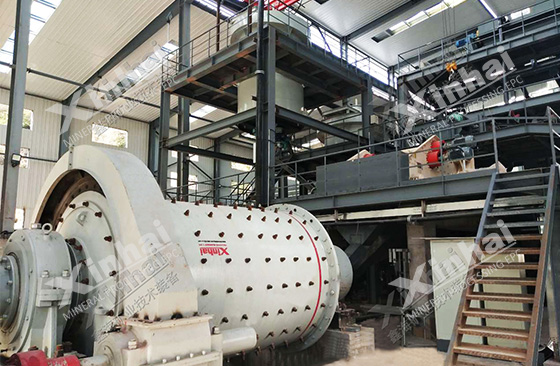
(Grinding equipment)
Grinding: Grinding is a copper ore treatment process after crushing and screening. This process can further refine the ore and facilitate the subsequent mineral processing process. Commonly used grinding equipment mainly includes ball mills and rod mills. The ball mill uses a rotating cylinder and steel balls to grind ore into smaller particles. The structure of a rod mill is similar to a ball mill, but the grinding medium it uses is mainly a longer cylindrical rod.
02Flotation technology for copper ore beneficiation
As one of the commonly used beneficiation methods for copper ores, flotation technology mainly performs separation based on the difference in surface properties between copper minerals and gangue minerals. During the flotation process, the ground copper ore particles are mixed with specific flotation reagents, and air is introduced into the flotation machine to generate foam. Useful mineral particles adhere to the surface of the foam, then float to the liquid surface, and are then scraped away and collected by a scraper. Flotation reagents are important elements in the flotation process and can be divided into collectors, frothers and regulators according to their functions. Collecting agents are mainly reagents adsorbed on the surface of copper mineral particles. The frother mainly plays a role in generating foam during the flotation process. The adjuster is mainly used to adjust the pH value of the slurry.
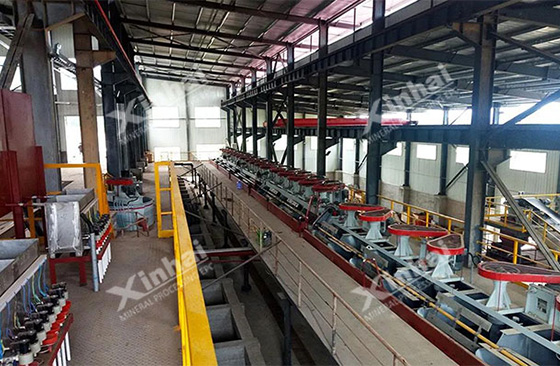
(flotation equipment)
Foam flotation is highly selective and can effectively separate valuable copper minerals from ores. It is especially effective in treating copper ores containing sulfide minerals. It can also be used to treat non-ferrous metal minerals such as lead, zinc, Nickel etc. The equipment used in flotation includes flotation machines, stirring tanks and flotation reagents. It is necessary to select the appropriate type of flotation equipment based on the actual processing capacity to improve mineral processing efficiency and reduce production costs.
03Gravity separation technology for copper ore beneficiation
Gravity separation is another important method for copper ores, mainly used to process denser ores, because gravity separation mainly uses the density difference between different minerals for separation. Equipment that can be used in the re-selection process are: shakers, jigs and spiral chutes.
Shaking table gravity separation: The ore mixture is placed on the table of the shaking table, and shaken to generate fluctuations, so that minerals with different densities are stratified. Valuable copper minerals will be concentrated along one side of the table, while other minerals are scattered along the other side. Finally, copper minerals and non-copper minerals are separated separately and can be collected through different discharge ports.
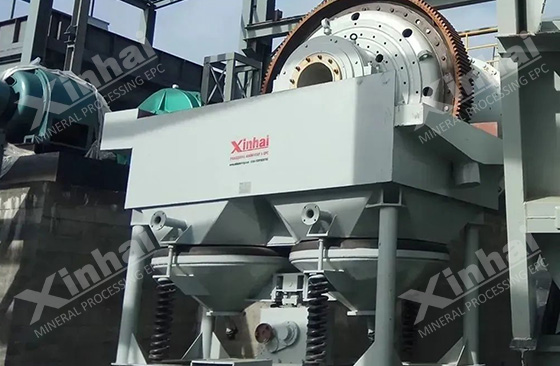
(Jig)
Jig gravity separation: The copper ore is fed into the jig, and the jagged plates inside the equipment will rise and fall periodically, forming a wave motion, causing the particles in the ore to float and sink respectively. According to the density difference, the value The copper minerals will settle at the bottom, while the lighter minerals will float up. Finally, by adjusting the equipment parameters, the separation effect of minerals with different densities in the ore can be controlled.
Spiral chute gravity separation: The ore mixture is injected through the feed port on the spiral chute and rotates and slides along the spiral structure. Due to density differences between the ore minerals, the ore naturally stratifies, with valuable copper minerals sliding down the outside of the spiral grooves while light minerals concentrate in the center. Eventually, copper minerals and non-copper minerals are separated separately.
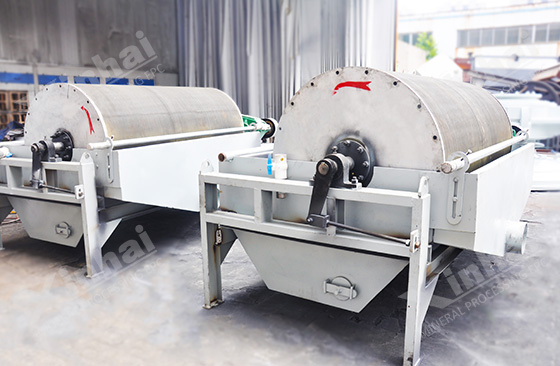
(Magnetic separation equipment)
04Magnetic separation technology for copper ore beneficiation
Since there may be magnetic minerals or impurities in copper ore, which affects its quality, magnetic separation technology is used to remove impurities. Magnetic separation technology is mainly used to improve the quality of ore. Commonly used equipment in the magnetic separation process mainly include magnetic rollers and metal detectors. The magnetic drum is equipped with a rotating magnetic drum. When copper minerals enter the magnetic field, the impurities will be adsorbed on the drum and then separated. Metal detectors are often used on conveyor belts to separate magnetic impurities from flowing ore during the conveyance process.
The magnetic separation method is highly selective and can effectively remove magnetic impurities without affecting copper minerals. The magnetic separation process usually does not require the use of chemical reagents and therefore has a low impact on the environment.
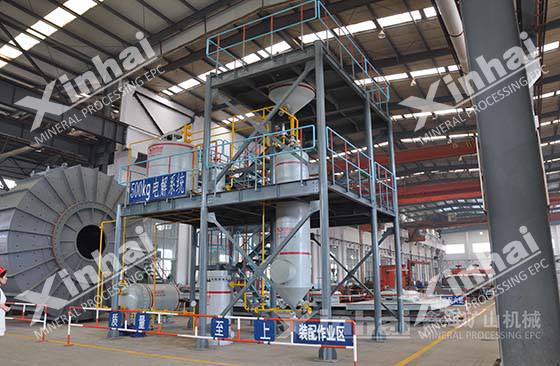
(Electrolysis system)
05Electrowinning and electrolytic refining of copper ore beneficiation
After copper ore is concentrated, some impurities still exist. Electrowinning and electrolytic refining can be used to purify copper and improve the purity of copper metal. In electroplating, an electric current is passed through a solution containing copper ions, causing copper to be deposited on the cathode. Electrorefining further purifies the copper to meet industrial standards. Equipment used in these processes include electrolytic cells and electrolysis cells.
The above are commonly used technologies in the copper ore beneficiation process. In actual production, in order to process copper ores with relatively complex compositions, two or three technologies are often used in combination to improve the grade of copper concentrate and the efficiency of beneficiation. Therefore, choosing the appropriate method and method is an important way to realize the beneficiation of copper ore, but it needs to be based on the specific ore characteristics and production requirements, so it is necessary to conduct a beneficiation test. Select the copper ore beneficiation plan and equipment based on the test results. , which can improve the mineral processing efficiency.