The basic process of mineral flotation is to separate different minerals based on differences in their flotability. In nature, the natural floatability of most minerals is very poor and effective flotation separation cannot be achieved. In order to obtain good flotation results, it is necessary to add flotation agents to the slurry during flotation to expand the flotability difference between different minerals. Flotation agents are also commonly used in phosphate mineral flotation. According to different functions, we divide them into three major categories: collectors, frothers and regulators. The following will introduce you to the types of reagents used in the phosphate mineral flotation process around these three flotation reagents.
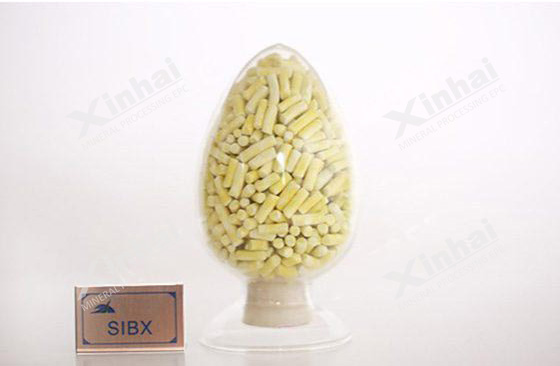
(Collector)
Use the table of contents below to navigate through the guide:
01Phosphate mineral flotation reagent collector
Collecting agents can interact with the mineral surface, reducing the wettability of the mineral surface, thereby improving the mineral's floatability. The ionic or molecular structure of the collector contains two structures: polar groups and non-polar groups. When the collector interacts with the mineral surface, the polar groups will be adsorbed on the mineral surface. Since the non-polar group faces water, the mineral surface cannot come into contact with water, thereby increasing the hydrophobicity of the mineral surface. Fatty acids and their soaps are often used as collectors in phosphate rock flotation. Their high freezing points ensure that they are difficult to disperse and dissolve in the slurry. In order to ensure the full interaction between the collector and the mineral particles, the slurry heating method can be used to make them well dispersed in the slurry.
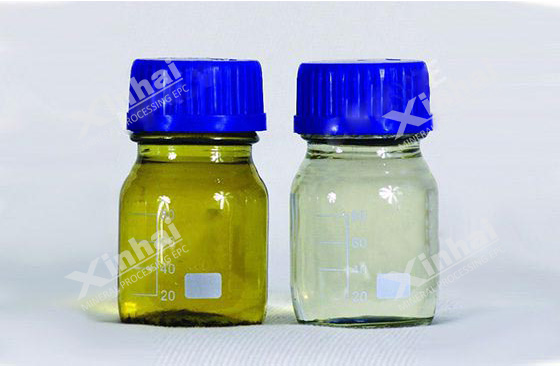
(Frother agent)
02Phosphate mineral flotation reagent frother
During flotation, foam is the medium through which mineral particles float. During flotation, the size of the bubbles should not be too large or too small. If it is too large, the amount of mineral particles attached will be reduced and the flotation effect will be poor. If the bubbles are too small, it will be difficult for the bubbles to float up after the mineral particles are attached. Foam stability should be appropriate. The purpose of adding a foaming agent is to ensure the production of large and stable foam. However, because fatty acids and soap collectors are added during phosphate rock flotation, they have foaming properties, so there is generally no need to add frother during phosphate rock flotation.
03phosphate mineral flotation reagent regulator
The main function of the regulator is to improve the selectivity of the flotation process, strengthen the collector effect, and improve the conditions of the flotation slurry. There are three types of regulators commonly used in the mineral processing process: inhibitors, activators and medium regulators.
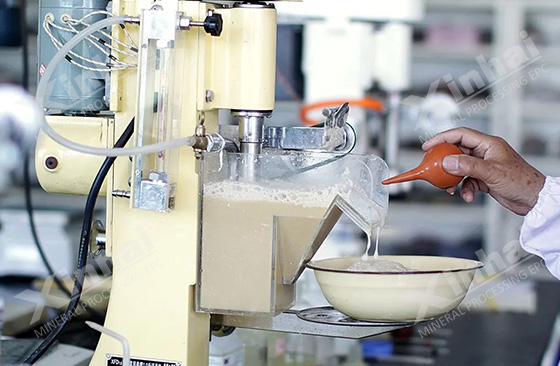
(Beneficiation test for flotation process)
Inhibitors: The types of inhibitors can be divided into two major categories. One is to form a hydrophilic film on the mineral surface to prevent the interaction between the collector and the mineral surface. The second is to dissolve the collector film or the active film that contributes to the action of the collector from the mineral surface, reducing the concentration of active ions in the solution and making it difficult for the collector film to regenerate. The selection of phosphate rock flotation inhibitor should be based on the composition of the gangue mineral. If the gangue mineral is a silicate mineral, water glass should be selected. If the gangue mineral is a carbonate, cellulose should be selected.
Activator: The main purpose is to change the mineral surface into a state that is easy to absorb the collector. In production practice, some minerals cannot directly adsorb collectors, and activators need to be added to change the properties of the mineral surface to facilitate the adsorption of collectors. The commonly used types of activators are mainly heavy metal salts.
Medium adjuster: its main function is to adjust the pH of the slurry, adjust the effects of other drugs, eliminate the impact of harmful ions on flotation, and adjust the dispersion and aggregation of the sludge. Among them, adjusting the pH value of the slurry is an important measure affecting flotation. Apatite flotation often occurs in alkaline media, so sodium carbonate is often used as a media adjuster, which can not only adjust the pH value of the slurry, but also play a buffering role. Sodium carbonate is often used in conjunction with sodium silicate to enhance its inhibitory effect. Sodium carbonate also serves as a good dispersant to prevent the agglomeration of fine mud in the slurry and improve the selectivity during the flotation process.
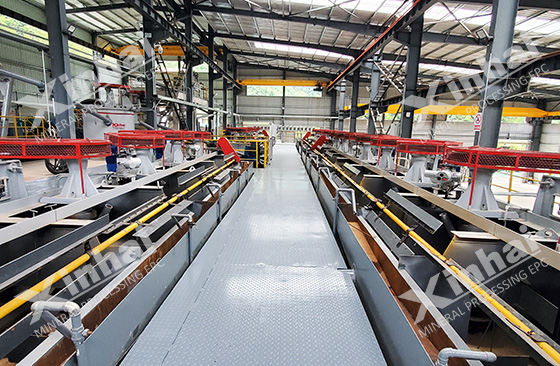
(flotation equipment)
The above content is the three reagents used in the phosphate rock flotation process. The selection of reagent types, the dosage and method of reagent addition will affect the phosphate rock flotation effect. Therefore, mineral processing test analysis should be carried out, and the appropriate flotation reagent type should be selected based on the results. Formulating an appropriate chemical system can not only reduce chemical consumption, but also improve the phosphate flotation effect, concentrate recovery rate and resource utilization rate, thereby improving the economic benefits of the overall mineral processing.