As one of the most important mineral resources in the world, the development and utilization of iron ore resources is crucial to the steel industry. In recent years, with the advancement of science and technology and the continuous development of mining technology, more and more composite iron ores have been discovered, which contain a variety of non-ferrous useful minerals that can be comprehensively utilized. These associated minerals can not only increase the economic value of the ore, but also effectively utilize resources and reduce environmental burdens. This article will discuss in detail the beneficiation technology of composite iron ores with multi-metal symbiosis, especially how to effectively separate and comprehensively utilize these minerals.
Use the table of contents below to navigate through the guide:
01Resource characteristics of polymetallic iron ore
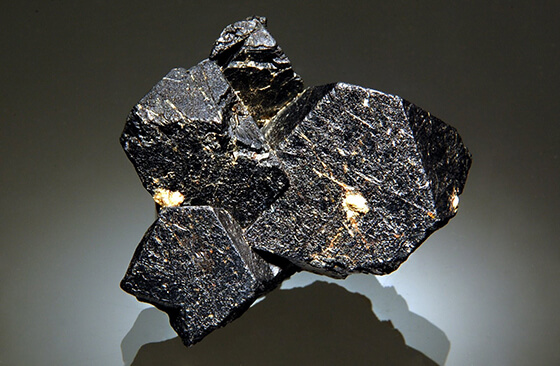
Among the iron ore resources that have been developed and utilized in the world, there are a large number of composite iron ores. These ores not only contain the main iron minerals, but also are associated with a variety of useful non-ferrous minerals, such as non-ferrous metal minerals such as copper, lead, zinc, as well as ilmenite, rare earth minerals, apatite, pyrite, etc. The presence of these associated minerals increases the complexity of the ore, but also provides rich economic value and development potential.
02Iron ore with associated polymetallic sulfides
Polymetallic sulfide ores contain copper sulfide, lead sulfide, zinc sulfide and other minerals, which can be effectively separated by flotation process. Sulfide flotation process is mainly divided into two combined processes:
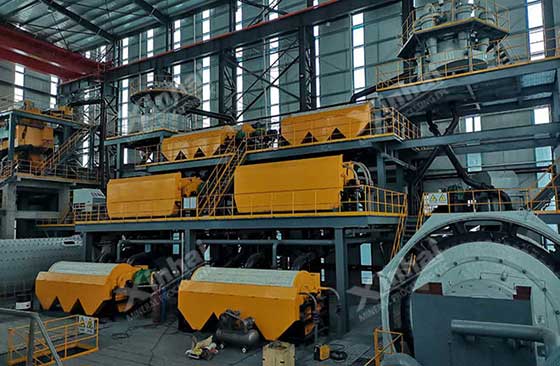
1. Magnetic separation-sulfide flotation combined process: This process is suitable for composite iron ores with low sulfide mineral content. Its advantages are simple process, small amount of ore to be processed by flotation, and wide application range. The magnetic separation process can first separate the magnetite from the iron ore, and then float the remaining sulfide to obtain a concentrate containing useful minerals such as copper, lead, and zinc.
2. Sulfide flotation-magnetic separation (or single flotation) process: This process can effectively reduce the sulfur content in iron concentrate, so it can be used to treat composite iron ores containing higher sulfide minerals or iron minerals containing more hematite and limonite, especially in ores containing more pyrrhotite. By first performing sulfide flotation separation and then magnetic separation, a relatively pure iron concentrate can be obtained and the sulfide minerals can be recovered as a separate concentrate.
03Iron ore associated with ilmenite
Titanium magnetite is the main mineral associated with ilmenite, and its ore usually contains magnetite, ilmenite crystal, magnesia spinel and a small amount of ilmenite platelets. The main occurrence of ilmenite is granular, platelet and irregular, among which granular is the main one. Ilmenite contains a high magnesium content and is isomorphous with ilmenite. In addition, ilmenite may also be associated with minerals such as cobalt and nickel.
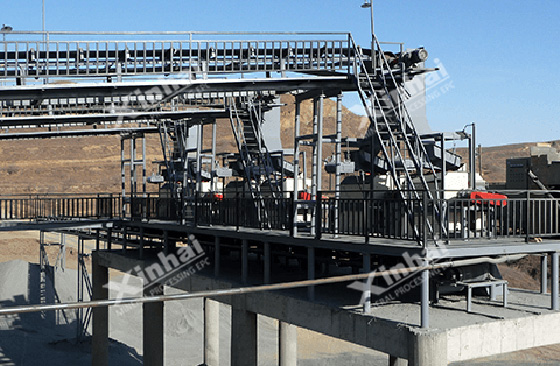
The beneficiation of ilmenite mainly relies on magnetic separation. After long-term production practice, magnetic separation has matured and can effectively extract vanadium iron concentrate from vanadium titanium magnetite ore. The production of vanadium iron concentrate is stable and the smelting technology is becoming more and more mature. However, production practice shows that the iron and titanium content in iron concentrate varies greatly depending on the mining area and ore grade, which mainly depends on the content of titanomagnetite in the original ore and its structural characteristics.
04Iron ore with rare earth minerals
Rare earth elements are an important strategic resource and are widely used in high-tech industries. Iron ore with rare earth minerals usually needs to be processed through complex mineral processing. Rare earth minerals include fluorite, apatite, etc. The mineral processing of these minerals usually involves multi-step flotation, magnetic separation and gravity separation. The recovery of rare earth minerals can not only increase the economic benefits of the ore, but also have a positive effect on environmental protection, because the mining and utilization of rare earth minerals can reduce the mining pressure of other mineral resources.
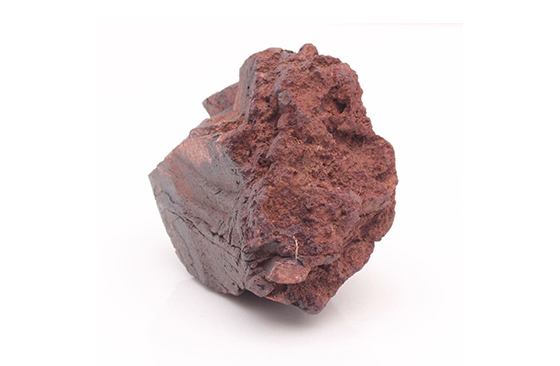
05Iron ore with associated phosphate ore and barite
The presence of phosphate ore and barite as associated minerals in iron ore increases the complexity of the beneficiation process. Phosphate ore is mainly used to produce phosphate fertilizers, while barite is used to make radiation protection materials. The beneficiation of these minerals generally adopts flotation, gravity separation and other methods. Especially for the beneficiation of phosphate ore, special attention should be paid to avoid mixing phosphate ore with iron minerals during the sorting process to ensure the purity and quality of the product.
06Iron ore containing dispersed nonferrous and rare metal elements
Iron ore may contain dispersed nonferrous and rare metal elements, such as cobalt, nickel, platinum, etc. The dispersed state of these metal elements makes their recovery complicated and requires special mineral processing technology. Commonly used technologies include gravity separation, flotation and electromagnetic separation. These technologies can effectively separate nonferrous metals and rare metals from ores and improve the comprehensive utilization value of ores.
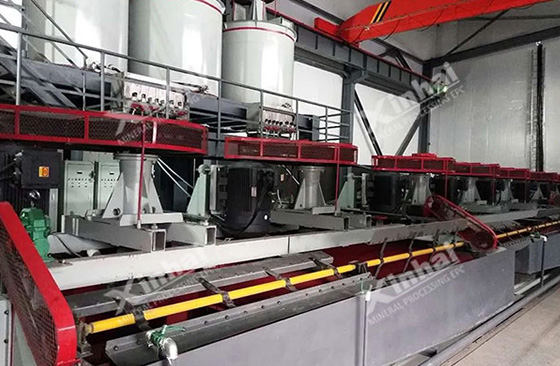
Composite iron ore with polymetallic symbiosis is of great significance in mining development. The economic benefits and resource utilization of ore can be improved by studying and applying the beneficiation technology of different types of associated minerals. Selecting the appropriate iron ore beneficiation process can not only effectively separate and recover useful minerals, but also reduce environmental pollution and resource waste.