The beneficiation process of nickel ore is closely related to the properties of the ore, the mineral composition and the requirements of the final product. According to different types of nickel ores and their flotation properties, there are various choices in the design of beneficiation processes in practice. Especially when processing sulfide copper-nickel ores, a stage beneficiation process is usually adopted, combined with rapid flotation, differential flotation, sediment separation, magnetic flotation combined process, etc., to maximize the recovery rate and improve the concentrate grade. This article will systematically introduce the main beneficiation processes of nickel ore and their related structural designs.
Use the table of contents below to navigate through the guide:
01Main types of nickel ore
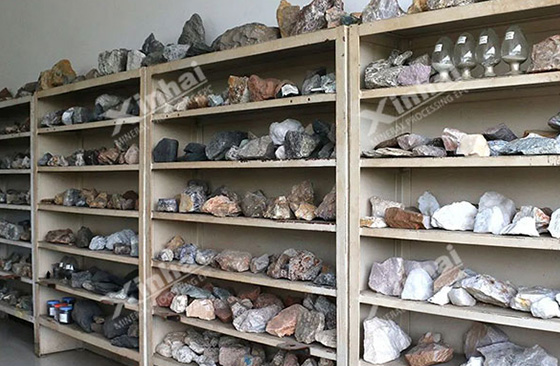
According to the different mineral components and mineral types, nickel ores can be roughly divided into the following two categories:
1. Nickel sulfide ore: This type of ore mainly contains pentlandite, nickel sulfide and copper-nickel sulfide, has good flotation performance, and is the key ore type to be processed during the beneficiation process.
2. Nickel oxide ore: Such as laterite nickel ore, mainly contains nickel oxide. Since nickel oxide ore is not easy to float, it is usually processed by metallurgical extraction method.
02Design of the beneficiation process of sulfide nickel ore
The beneficiation process of copper-nickel sulfide ore is mainly flotation, which aims to maximize the grade and recovery rate of concentrate by reasonably designing the staged operation process. The following is a common beneficiation process structure.
1. Stage beneficiation process
The stage beneficiation process is the main processing process of nickel sulfide ore. Through multiple flotation stages such as roughing, concentrating and scavenging, nickel minerals and gangue are effectively separated. The specific steps of this process include:
- Roughing: Preliminary separation of nickel minerals to obtain rough concentrate;
- Concentrating: Further enrich the rough concentrate, remove impurities, and improve the grade of the concentrate;
- Scavenging: Reprocess the rough tailings to recover the residual nickel minerals.
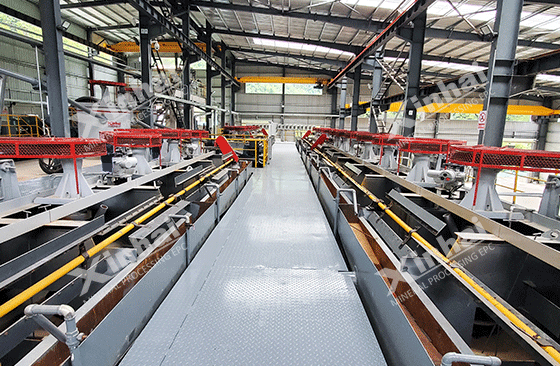
2. Rapid flotation and speed-differential flotation
Rapid flotation is suitable for easy-floating minerals and aims to reduce the flotation time, while speed-differential flotation separates different minerals (such as nickel and copper) by adjusting the flotation speed and the order of reagent addition. This process is suitable for processing ores with uneven mineral particle sizes or large differences in flotation speeds.
3. Sediment separation and separation flotation
Sediment separation is aimed at the situation where the fine mud content in the ore is high. By separating the fine mud and coarse sand in the ore and flotating them separately, the overall flotation effect is improved. The process includes:
- Mud separation: first separate the fine mud to prevent it from affecting the flotation effect;
- Sand selection: specializes in processing coarse-grained minerals to improve the flotation speed and efficiency.
4. Magnetic flotation combined process
When processing nickel ores containing magnetic minerals (such as magnetite), the magnetic flotation combined process is an effective process. This process can significantly improve the nickel recovery rate and concentrate quality by first removing strong magnetic minerals by magnetic separation and then flotating the remaining nickel minerals.
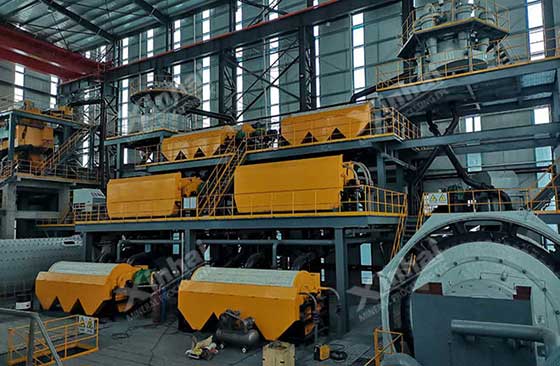
5. Optimization of the number of concentrations
In order to simplify the process and reduce energy consumption, the number of concentrations is often reduced by optimizing the reagent system and flotation parameters in mineral processing practice to achieve a balance between concentrate grade and recovery rate.
03Basis for selection of nickel ore mineral processing
The selection of nickel ore beneficiation process is mainly based on the following factors:
1. Mineral composition: The mineral composition of different ores directly affects the selection of reagents and the design of flotation time. For example, sulfide nickel ore is suitable for flotation treatment, while laterite nickel ore is more suitable for metallurgical extraction.
2. Dissemination particle size: The dissemination particle size of nickel minerals in the ore will directly affect the design of the flotation process. Fine-grained dissemination minerals usually require more complex flotation processes.
3. Product requirements: Product quality requirements determine the final design of the mineral processing process. For example, copper-nickel symbiotic ores usually use separate flotation processes to enrich copper and nickel separately.
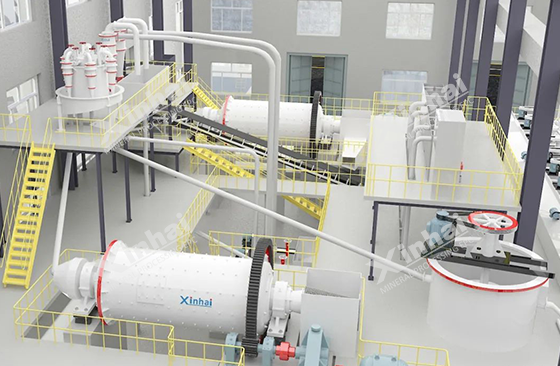
The design of nickel ore beneficiation process is a systematic project. The properties and flotation performance of different ores determine the choice of process structure. In the beneficiation process of sulfide copper-nickel ore, process methods such as stage beneficiation process, rapid flotation, sediment separation, and magnetic levitation combined process have been widely used and continuously optimized in actual operation to improve nickel recovery and concentrate grade. In the future, with the advancement of mineral processing technology, the design of process flow will be more accurate and efficient, ensuring the effective utilization of resources and the improvement of mine economic benefits. In this context, mineral processing companies need to flexibly adjust the process flow according to the specific properties of the ore and market demand, continuously optimize production operations, and ensure maximum benefits.