With the continuous advancement of today's mineral processing technology, the mixed iron ore processing technology has also made great progress. Because mixed iron ore contains a certain proportion of magnetite and weakly magnetic iron ore, the mineral processing process requires a more diversified and flexible process combination. At present, roasting magnetic separation, weak magnetic separation, strong magnetic separation, flotation-gravity separation, etc. are widely used for the mixed iron ore processing . These mineral processing methods not only improve the efficiency of mineral processing, but also reduce the cost of mineral processing to varying degrees.
Use the table of contents below to navigate through the guide:
01Mixed iron ore processing process
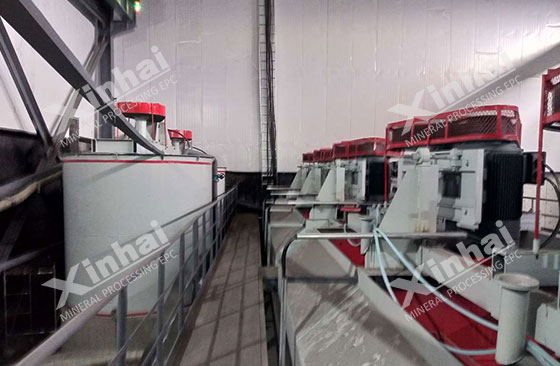
1. Iron ore flotation-magnetic separation (magnetic-flotation) combined process
This process has the characteristics of high unit production capacity of the main equipment, and is mainly suitable for large-scale beneficiation plants, and can obtain good beneficiation indicators. The order of flotation process and magnetic separation process needs to be determined according to the specific situation of mixed iron ore.
- Flotation first and magnetic separation later: This process is short, stable in production and easy to manage, but for mixed iron ore with a high content of magnetite, the reagent consumption is large and the flotation load is large, so it is not ideal for this ore.
- Magnetic separation first and flotation later: Although the operation is complicated and a thickener needs to be added, the amount of ore flotation can be greatly reduced, and it is widely used in actual beneficiation plants.
2. Combined gravity-magnetic separation process for mixed iron ore
The combined gravity-magnetic separation process is relatively mature in the application of ore dressing plants. Its equipment structure is simple, the overall ore dressing cost is low, the concentrate is easy to dehydrate, and it will not cause pollution to the environment. This combined method has a poor recovery effect on -30μm fine-grained weakly magnetic iron ore and requires more gravity separation equipment.
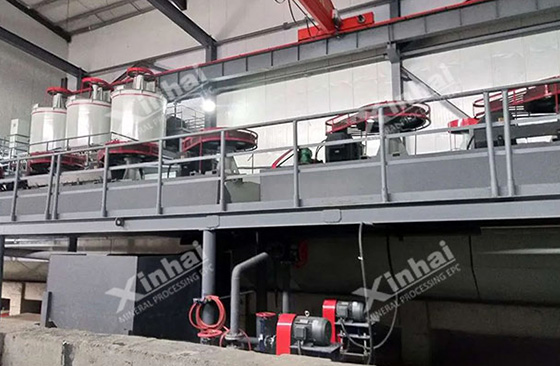
3. Combined gravity-magnetic-flotation process for mixed iron ore
The use of stage grinding, stage separation and combined separation process is the development trend of mineral processing today. When mixed iron ore is treated by stage grinding and combined gravity-magnetic-flotation separation process, after a closed-circuit grinding, the overflow is classified into coarse and fine particles after being classified by a cyclone. After the coarse-grained minerals are separated by spiral chute, part of the concentrate is obtained. The tailings of the re-selection need to be weakly magnetically separated, and then combined with the middlings of the spiral chute for re-grinding and returned to the primary cyclone. For fine-grained minerals, the weak magnetic-strong magnetic-acid flotation process is used for treatment.
02Innovation and development of mixed iron ore processing technology
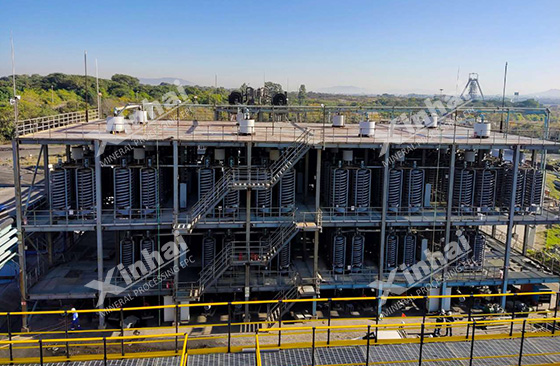
With the development of science and technology, new beneficiation equipment and processes continue to emerge, providing more options for the efficient separation of mixed iron ore. At present, automated and intelligent beneficiation technologies are gradually being applied to beneficiation production, and accurate control and optimized configuration of the beneficiation process are achieved through data analysis and intelligent control. The research and development of new environmentally friendly reagents is also constantly advancing, aiming to reduce reagent consumption, reduce environmental pollution, and improve the green level of beneficiation.
03Future prospects of mixed iron ore processing technology
In the future, the development of mixed iron ore processing technology will pay more attention to the following aspects:
1. Improve resource utilization: Through refined sorting technology, maximize the recovery of useful minerals and improve the comprehensive utilization of resources.
2. Reduce production costs: Reduce the production cost of dressing by introducing new and efficient dressing equipment and optimizing process flow.
3. Environmentally friendly: Adopt green dressing technology to reduce pollution emissions during the dressing process and achieve sustainable development.
4. Intelligent management: Use artificial intelligence and big data technology to monitor and optimize the dressing process in real time to improve dressing efficiency and accuracy.
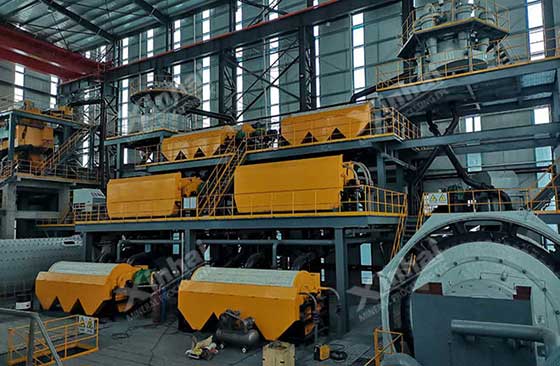
The mixed iron ore processing technology has made significant progress in the past few decades, and various combined beneficiation processes have been widely used in actual production and achieved good results. In the future, with the continuous introduction and application of new technologies, the mineral processing efficiency and resource utilization rate of mixed iron ore will be further improved, achieving green and efficient mineral processing. At the same time, the mineral processing industry will also develop in the direction of intelligence and automation, contributing to the efficient utilization and sustainable development of mineral resources. With the continuous innovation and development of mineral processing technology, the mineral processing technology of mixed iron ore will become more mature and efficient, providing a more solid resource guarantee for the development of the steel industry.