Fluorite is an important ore resource and the main fluorine raw material. With the gradual depletion of high-grade fluorite ore resources, the use of associated (symbiotic) fluorite ore resources has been put on the agenda, and the flotation process is the most important beneficiation method for fluorite ore. Lithium is widely used in new energy, ceramics, aerospace, medicine, national defense and other fields, and lepidolite is one of the most important resources for extracting lithium, which can improve the utilization rate of lepidolite resources and promote the high-quality development of lithium industry. The main beneficiation method of lepidolite and fluorite is flotation. At present, fluorspar and lepidolite are usually recovered separately in the industry. The method of using flotation fluorite to suppress mica has a long process, many types of chemicals, and a low recovery rate. In view of these problems, this paper will introduce a mineral separation method of fluorite-containing lepidolite concentrate. This method is to mix the mixed concentrate obtained by flotation of fluorite lepidolite, and adopt the technical scheme of flotation fluorite to inhibit lepidolite.
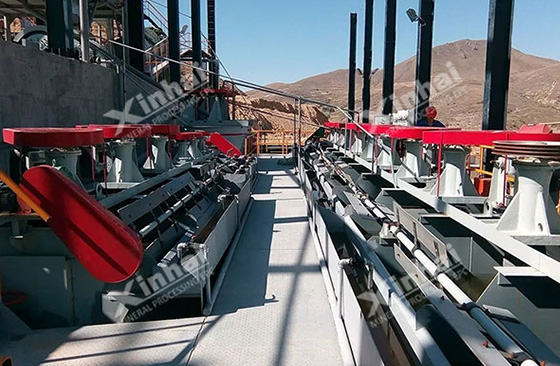
Use the table of contents below to navigate through the guide:
011. Fluorite roughing separation stage
Inhibitor (composed of caustic starch and sodium hydroxide) and collector A (composed of sulfonated oleic acid, diesel oil and dodecylbenzenesulfonic acid Sodium composition) for roughing operation, fluorite rough concentrate and roughing tailings can be obtained. The addition amount of inhibitor is generally 10-100g/t, and the addition amount of collector A is 10-50g/t. In order to improve the utilization rate of ore resources, the roughing operation of fluorite is carried out at least once, and the obtained roughing tailings are subjected to at least one sweeping operation; the middle ore obtained from the sweeping operation is returned to the previous operation in sequence for processing.
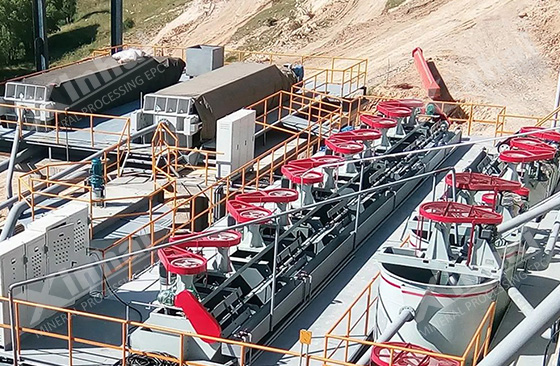
022. Fluorite ore concentration separation stage
The fluorspar coarse concentrate obtained from the above process enters the beneficiation operation for processing. When performing beneficiation, it is necessary to add inhibitors to the pulp. In order to improve the recovery rate of fluorite concentrate, the beneficiation operation must be carried out at least three times. Each beneficiation needs to add inhibitors to the ore pulp, and the addition amount is 10-60g /t. The medium ore in the beneficiation operation needs to return to the previous processing stage.
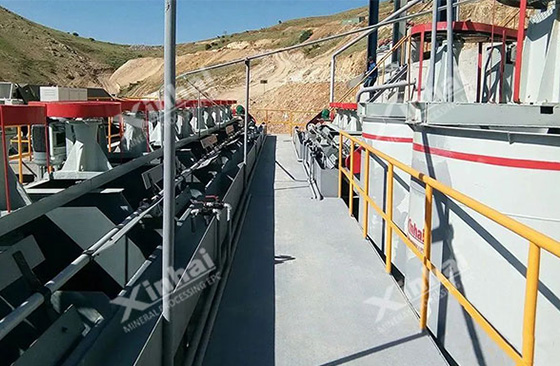
033. Lepidolite rough separation + concentration stage
The tailings obtained from the above-mentioned rough separation of fluorite are adjusted for slurry, the pH value of the slurry is adjusted to 2-5, and collector B (composed of dodecylamine and octadecylamine) is added for ore dressing to obtain lepidolite coarse concentrate and re-election tailings. The lepidolite coarse concentrate can be obtained through at least three times of blank beneficiation. Re-selection of tailings also requires a sweeping process, and the middlings produced in the above process need to be returned to the previous step for processing.
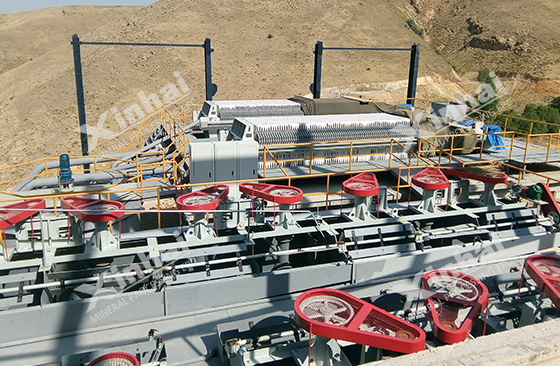
The above process improves the common mineral flotation separation method. The method is to mix flotation fluorite and lepidolite, and separate the mixed concentrate. This process is short and the concentrate recovery rate is high, which can improve the resource utilization rate of fluorite concentrate and lepidolite concentrate. In actual production, the specific fluorite lepidolite beneficiation plan should also be determined according to the characteristics of the ore itself. Xinhai Mining recommends that the beneficiation test be carried out in order to determine the suitable beneficiation process. Xinhai Mining has more than 20 years of experience in beneficiation process design, and can provide you with customized fluorite beneficiation solutions, lithium beneficiation solutions.