Magnetite mineral is a naturally occurring iron oxide mineral that is one of the most magnetic minerals found in nature. Magnetite is commonly found in a variety of geological formations, including igneous, metamorphic, and sedimentary rocks. Its magnetic properties make it valuable in a variety of applications, from compasses and navigation tools to industry. In order to rationally utilize magnetite resources, it is particularly important to select appropriate magnetite beneficiation technology and equipment. Magnetite beneficiation consists of multiple processes, and specific process equipment is used in each process to improve the efficiency of ore processing. The following will introduce you to the mineral processing technology and equipment of magnetic separation.
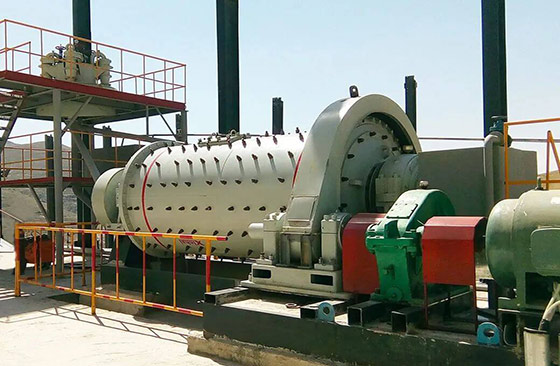
(Grinding system)
Use the table of contents below to navigate through the guide:
01Magnetite mineral crushing&grinding processes and equipment
The initial step in magnetite beneficiation is the crushing and grinding of ore. Crushing mainly uses equipment such as jaw crushers, cone crushers and impact crushers to crush the original magnetite ore into smaller particles. After screening, the minerals under the screen are then ground into finer particles using a ball mill or rod mill, which helps to achieve the monomer dissociation of magnetite and liberate it from the gangue minerals. The screened product is returned to the crushing system for processing. The ground products need to be processed by classification equipment before entering the sorting stage, in order to improve the sorting efficiency.
02Magnetite mineral separation technology and equipment
1. Magnetic separation technology and equipment
The equipment used for primary magnetic separation of magnetite mainly includes magnetic drum, permanent magnet drum magnetic separator and dry magnetic separator. These devices can complete the separation of magnetite and non-magnetic gangue minerals. In the magnetic separation process, high gradient magnetic separators and magnetic filters are used for secondary magnetic separation, which can remove finer particles or impurities and further improve the purity of the concentrate.
2. Gravity separation technology and equipment
Because magnetite is denser than most gangue minerals, it can be separated using gravity separation technology. Gravity separation mainly relies on the density difference between different minerals for separation. Shaking tables, jigs and spiral chutes can be used to further separate gangue minerals and magnetite and improve the taste and quality of magnetite concentrate. In the mineral processing process, after the first stage of gravity separation, it is necessary to set up the second stage and the third stage of gravity separation process to further concentrate the concentrate and improve the quality of the concentrate.
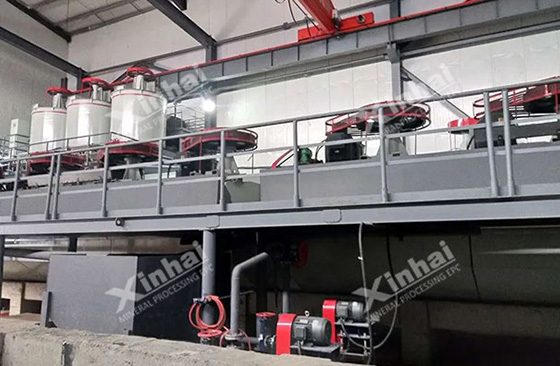
(flotation system)
3. Flotation technology and equipment
When using flotation technology to select magnetite, it is necessary to pay attention to the use of flotation reagents. The types of flotation chemicals commonly used in the flotation process include collectors, frothers and regulators. Different types of chemicals have different effects on minerals. The collector can change the properties of the magnetite mineral surface to make it hydrophobic and easy to adhere to bubbles and float. The frother can stabilize foam generation, while the adjuster adjusts the pH of the slurry and improves flotation efficiency. Flotation equipment can choose flotation cells, flotation machines and flotation columns. Correct equipment paired with a suitable flotation reagent system can improve mineral processing efficiency and concentrate quality.
03Magnetite mineral concentration and dehydration technology and equipment
After the above separation, the concentrate obtained will contain a certain amount of moisture, which will affect the quality of the concentrate. A thickener, filter press or filter can be used to remove excess moisture and improve product quality. The tailings generated during the mineral processing process can also be processed after concentration and dehydration, which can reduce the impact of the tailings on the environment.
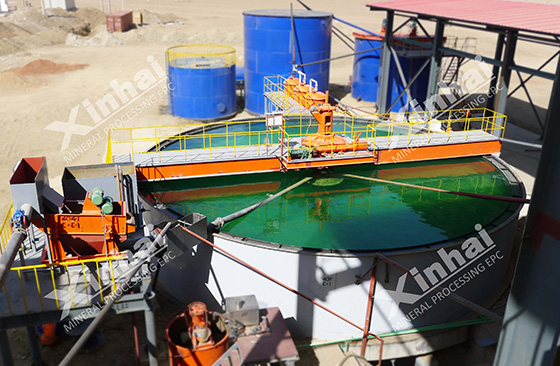
(Concentrated and dehydrated)
The above are the commonly used mineral processing methods and equipment for magnetite. In actual production, the specific methods and equipment used will be appropriately adjusted according to the characteristics of the ore, production requirements and product requirements. When the nature of the ore is relatively complex, it is necessary to combine a variety of mineral processing methods for processing. Xinhai Mining recommends conducting magnetite beneficiation test analysis to determine the composition and characteristics of the ore, and designing the beneficiation process based on the production requirements of the ore dressing plant. This can improve the beneficiation efficiency, reduce resource waste and environmental impact, and achieve green economic development and production.