Lead-zinc sulfide ore is an important metal mineral resource and is widely used in batteries, cables, alloys and other fields. The efficient separation and extraction of lead-zinc ores is the focus of research in the mineral processing industry. The separation method commonly used in mineral processing plants is flotation. The flotation effect depends on the performance and ratio optimization of mineral processing reagents. The following will introduce you to the flotation reagents and their use of lead-zinc sulfide ore, to help you better understand the flotation of lead-zinc sulfide ore, improve flotation efficiency, reduce production costs, and reduce the impact of reagents on the environment.
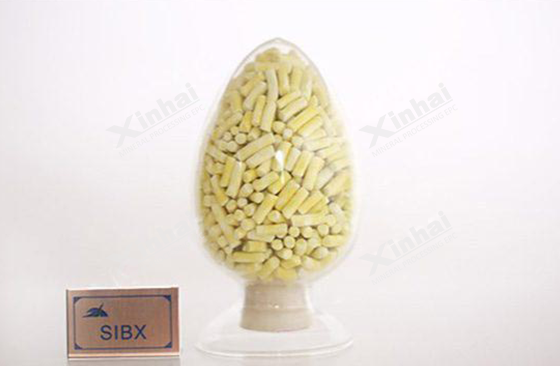
Use the table of contents below to navigate through the guide:
01Lead-zinc ore flotation reagents-collectors
During the flotation process of lead-zinc sulfide ore, the surface hydrophobicity of the target mineral will be improved through the selective absorption of the collector, making it easier for the mineral to attach to the bubbles and float up. Organic collectors have been widely used in the mineral foam flotation process. The main purpose is to improve the surface hydrophobicity of transition metal minerals. Sometimes mixed collectors are also used during the mineral processing process to improve the flotation effect, because the adsorption properties of mixed collectors on the mineral surface are better than those of a single collector.
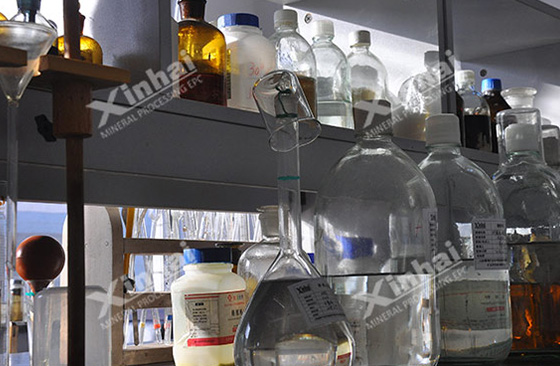
The amount of collector added will have a certain impact on the final product indicators. For example, without affecting the grade of the coarse concentrate, increasing the amount of collector can appropriately reduce the loss of sphalerite. The separation effect of sphalerite and other sulfide minerals is closely related to the slurry solution conditions (pH and concentration of copper ions), but at the same time, the flotation effect is also related to temperature. The recovery rate of zinc in winter will be lower than that in summer. The reason for this result may be that the formation of copper hydroxide and copper activation kinetics are slower at lower temperatures, or it may be due to hydrodynamics in flotation. and changes in particle-bubble interactions.
02Lead-zinc ore flotation reagents-inhibitors
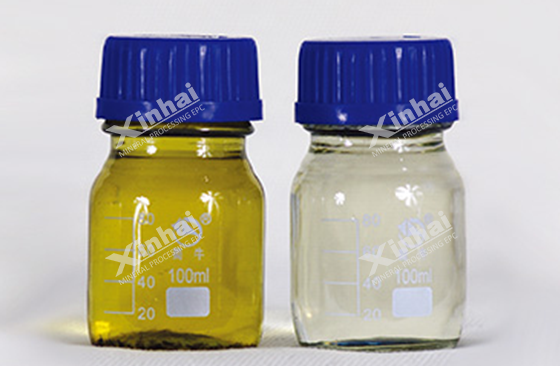
In the flotation separation process of lead-zinc ore, whether new minerals are effectively suppressed will directly affect the quality of lead concentrate. During the separation of lead-zinc ore, the slurry contains more lead ions, and these lead ions will activate the zinc-blende ore, thereby increasing the difficulty of lead-zinc separation. Therefore, in order to selectively enhance the hydrophilicity of the sphalerite surface and promote the inhibition of the sphalerite, the inhibitor needs to meet the following three conditions: (1) The inhibitor has a polar functional group that can strongly adsorb to the sphalerite surface. , making it fixed on the surface of the mineral. (2) the inhibitor must be selectively adsorbed on the surface of sphalerite. (3) the inhibitor contains groups that can make the surface of sphalerite hydrophilic.
The sphalerite inhibitors used in actual production of mineral processing plants are mainly divided into two types: inorganic inhibitors and organic inhibitors. Inorganic inhibitor types include sodium cyanide, zinc sulfate and sulfite, while organic inhibitor types include chitosan and sodium dimethyldithiocarbamate. According to the different properties of the specific ore, different chemical combinations are selected to effectively separate lead and zinc, and a rough lead concentrate with good grade and recovery rate is obtained.
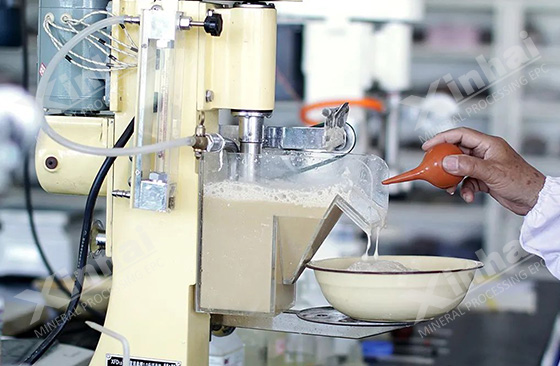
03Lead-zinc ore flotation reagents-activators
The sphalerite activation agents used in the lead-zinc ore flotation separation process mainly include cerium sulfate, lead nitrate, silver nitrate, mercuric chloride and copper sulfate. However, in production practice, considering the cost and zinc concentrate product Quality, etc., generally use copper salt as the activator of sphalerite. The effect of copper sulfate is better, so copper sulfate is commonly used as the activator of sphalerite.
In general, the optimization of lead-zinc sulfide ore flotation reagents can not only significantly improve the separation efficiency of the ore, but also effectively reduce resource waste and environmental pollution. Through in-depth research on the types, dosage and usage conditions of flotation reagents, the optimal flotation process parameters can be found to achieve efficient utilization of lead-zinc ore resources. In the future, with the development of green chemistry and nanotechnology, the research and development of new environmentally friendly and efficient flotation reagents will become a trend. It is hoped that the discussion in this article can provide reference for related research and actual production, and promote the sustainable development of lead and zinc mining.