Useful minerals in lead-zinc ore are usually distributed in fine granular or irregular shapes and are of low grade. Through the mineral processing process, these useful minerals can be enriched from the raw ore, improve the grade of the concentrate, and provide qualified raw materials for the subsequent smelting process. Flotation technology is one of the commonly used separation methods for lead-zinc ores, but the flotation technology will be different for different types of lead-zinc ores. The following will introduce you to a lead-zinc ore flotation and mineral processing process. According to the performance of the mineral processing equipment, the flotation and mineral processing process of lead-zinc ore can be divided into crushing operations, grinding operations, and flotation operations (lead beneficiation operations, zinc beneficiation operations). operations and copper selection operations) and other stages.
Use the table of contents below to navigate through the guide:
01Second-stage crushing operation of lead-zinc mine
After a coarse crushing operation, the raw lead-zinc ore is transported to the secondary crushing operation via a belt conveyor for fine crushing. After the raw ore reaches the appropriate particle size after being crushed in these two stages, it is sent to the ore warehouse for temporary storage as raw material for the grinding section.
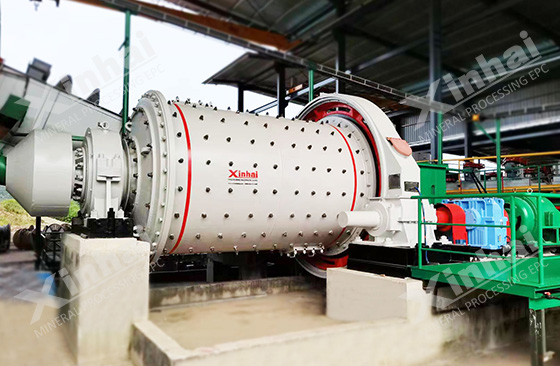
02Lead-zinc ore grinding operation
This stage uses a closed-circuit grinding and classification process. The ore in the ore bin is sent to the ball mill through the feeder under the average swing of the swing feeder for wet ball grinding. The ore and the steel balls in the barrel of the ball mill constantly hit and grind each other, and then are discharged out of the ball mill to form slurry. The slurry passes through the classification equipment and the slurry with qualified grinding particle size is sent to the next step, while the unqualified coarse particles will be returned to the ball mill for re-grinding.
03Lead-zinc ore flotation operation
The ore beneficiation operation of this mine adopts a preferential flotation process, which adopts a process of preferential flotation of lead, then zinc and finally copper, to separate separate lead concentrate powder, zinc concentrate powder and copper concentrate powder.
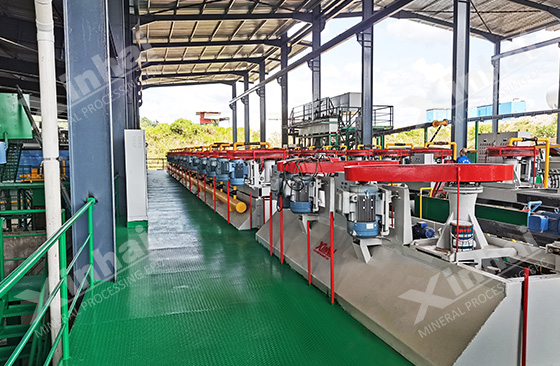
(1) Lead selection operation: After the ground slurry is mixed evenly in the mixing barrel, it enters the first operation section - lead selection operation. After the slurry interacts with the flotation reagent, mineralized foam will be formed in the flotation machine. At this time, the lead ore will be separated from the gangue minerals and the suppressed zinc ore and copper ore. After flotation separation, the lead concentrate can be obtained, and one coarse, two fine and three sweep operations can be used.
(2) Zinc selection operation: After the above-mentioned lead selection operation, the slurry enters the mixer for zinc flotation. The suppressed zinc is activated before flotation, and then collectors and frothers are added. The slurry will form mineralized zinc foam in the flotation machine. Qualified zinc concentrate can then be flotated. The zinc flotation operation can adopt the operation of one coarse, three fine and three sweep.
(3) Copper beneficiation operation: After the zinc beneficiation operation, the slurry enters the mixing barrel for copper flotation operation. Similar to the zinc beneficiation operation, the suppressed copper is activated and then a collector and a foaming agent are added, so that the slurry forms copper mineralized foam in the flotation tank, and qualified copper concentrate is flotated. The copper separation operation can be carried out by using a flotation process of one coarse, three fine and three sweeps.
04Lead-zinc ore tailings treatment operations
After a variety of metal concentrates are selected through three-stage flotation operations of lead, zinc and copper, the discharged tailings will be sent to the tailings dam for storage for further comprehensive utilization. The lead concentrate, zinc concentrate and copper concentrate will be sent to their respective concentrate pools, bagged and sent to the smelting plant for further processing, or exported as products. The wastewater from the mineral processing will be recycled after sedimentation.
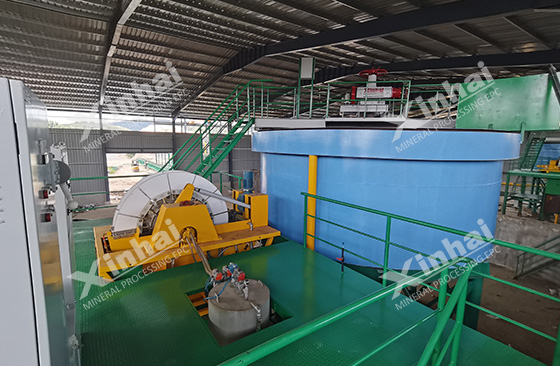
The above is an explanation of the operations at each stage of the lead-zinc ore flotation process. The process needs to be changed and optimized according to the actual needs of the mineral processing plant and the characteristics of the raw ore products. Xinhai Mining recommends conducting mineral processing tests to determine the characteristics of the ore, and customizing the design of the lead-zinc ore process to improve the economic, production and environmental benefits of the overall processing plant. Xinhai Mining can provide you with EPC+M+O services, from mineral processing test design to processing plant operation and management, helping you to build and produce your plant efficiently.