In actual production, the selection process of lead-zinc mine has developed a variety of processes, mainly including full potential controlled flotation, full flotation process, sulfide flotation process, gravity separation-flotation process, modified amine flotation, chelating collector flotation, leaching (ammonia leaching, acid leaching)-flotation, rapid flotation, branch series flotation, asynchronous mixed flotation, partial rapid priority flotation and smelting combined processes. These processes provide diversified solutions for different types of lead-zinc mines to improve resource utilization efficiency and ore dressing effect.
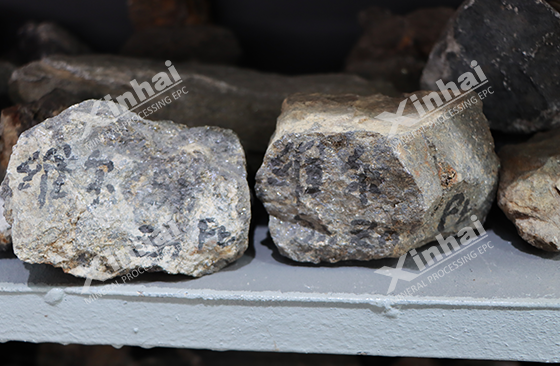
Use the table of contents below to navigate through the guide:
01Specific methods of lead-zinc mine beneficiation process
In the specific ore selection methods, single flotation methods can be divided into three types according to the properties of the ore and the process characteristics: priority flotation (lead first, then zinc), segmented flotation (sulfide ore first, then oxidized ore) and equal floatable process (first float easy ore and then float difficult ore). These methods have their own advantages and disadvantages and need to be selected according to the actual ore conditions.
For medium and low-grade oxidized lead-zinc mine resources, it is more suitable to choose the combined process of beneficiation and smelting: first use the forward and reverse flotation technology to select the oxidized lead-zinc concentrate, and these concentrates must meet the requirements of the combined technology of beneficiation and smelting. Although these concentrates may not meet the high-grade requirements of national standards, metals can be extracted through subsequent metallurgical processes (such as sulfuric acid leaching, purification, etc.) to meet production needs.
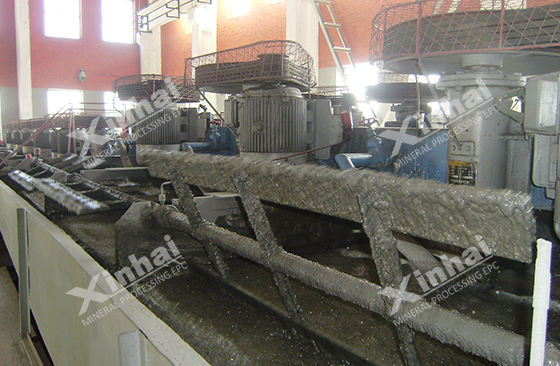
02Flotation problems of oxidized lead-zinc mine
The main problem of flotation of oxidized lead-zinc mine is the ore slime problem. Ore slime includes primary ore slime and secondary ore slime. The former is mainly composed of mud minerals in the ore such as kaolin, sericite, chlorite, etc., while the latter is produced due to over-crushing during crushing, grinding, transportation and mixing. The harm of ore slime to flotation process is mainly reflected in the following aspects:
1. Reduce the effective concentration of sulfiding agent: The presence of ore slime increases the solubility of ore pulp, thereby increasing the amount of sulfiding agent.
2. Pollute the surface of minerals: The ore slime covers the surface of oxidized ore, reducing its floatability.
3. Hinder the action of collector: The ore slime adheres to the surface of mineral particles, hindering the action of collector and target mineral.
4. Reduce the grade of concentrate: The ore slime easily adheres to the surface of bubbles and enters the concentrate, resulting in a decrease in the grade of concentrate.
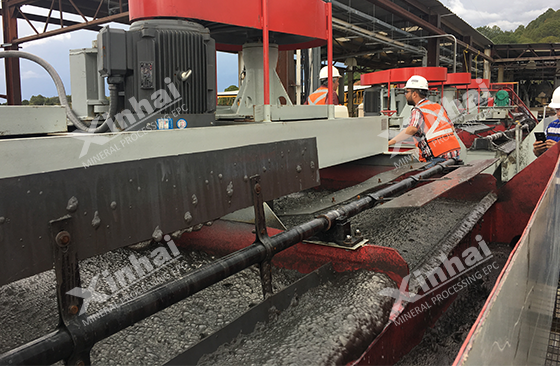
03Desliming methods to solve the problem of ore slime
In view of the obstruction of ore slime to the flotation of oxidized lead-zinc ore, the desliming methods currently used mainly include:
1. Ore pretreatment process: desliming by hydrocyclone.
2. Adding chemical agents: using water glass, sodium carbonate, and sodium hexametaphosphate to disperse the ore slime and eliminate the harmful covering effect of fine slime.
3. Adding agents in stages and batches: avoiding one-time dosing by ore slime.
4. Dilute ore pulp concentration: using a dilute ore pulp concentration to reduce the viscosity of the ore slime and its coverage of coarse particles.
5. Using mixed flotation: the combination of mixed amine and sec-octyl xanthate can achieve the effect of direct flotation of zinc oxide without desliming.
6. Electrochemical pretreatment: electrochemical pretreatment of the ore pulp to reduce the influence of ore slime on amine flotation.
7. Adjustment and dispersion of slurry: During the flotation process, adjusters are added to disperse the slurry and inhibit gangue. Then flocculants are added to flocculate the fine mud. Finally, carboxylic acid esters, tall oil and No. 2 fuel oil are mixed for flotation.
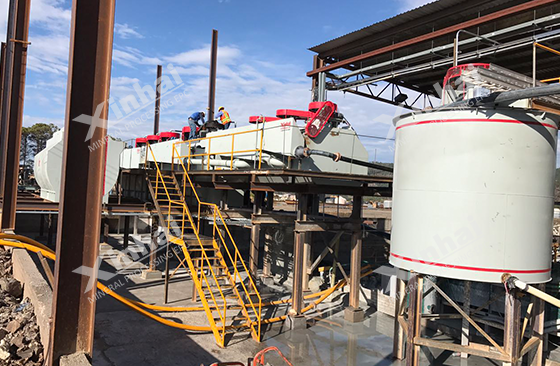
04Comprehensive utilization of lead-zinc mine resources
Lead-zinc mineral resources are often accompanied by valuable elements such as silver, copper, and germanium. Therefore, in the process of lead-zinc beneficiation, it is necessary not only to recover lead and zinc, but also to comprehensively recover other valuable elements to increase the value of resource utilization. This makes the flotation technology of lead-zinc beneficiation plants relatively complex. Therefore, the future development of lead-zinc ore beneficiation technology mainly depends on the optimization of separation reagents and process flow. For sulfide lead-zinc ore, the potential-controlled flotation method is worth promoting, while for oxidized lead-zinc mine, the key is to solve the ore slime problem and prevent over-crushing. Improve the crushing and grinding process, reasonably control the grinding fineness, and reduce the impact of fine slime on the flotation effect by optimizing separation reagents and process flow for the problem of fine slime.
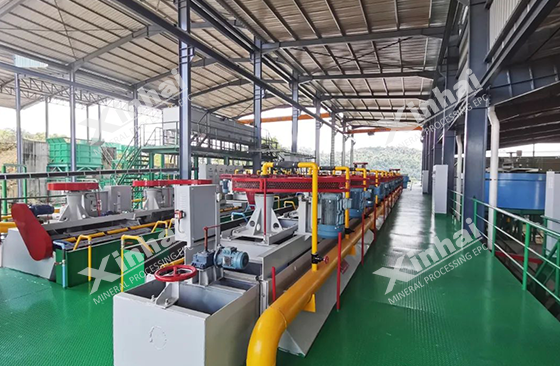
Lead-zinc mine separation technology involves a variety of processes and methods. According to different ore properties and process requirements, the use of appropriate technical means can effectively improve the recovery rate and concentrate quality of lead-zinc ore. The development of lead-zinc ore beneficiation technology will continue to focus on optimizing separation reagents, improving process flow and comprehensively utilizing associated resources, so as to achieve efficient utilization and sustainable development of lead-zinc ore resources.
05Specially listed are the cases of Xinhai Mining lead-zinc mine projects