There are many types of iron ore, including magnetite, hematite, siderite and limonite. Magnetite is magnetic and is the main object of magnetic separation. The other three are non-magnetic or weakly magnetic. For the beneficiation of iron ore, physical or chemical methods are generally selected to separate it from gangue minerals, including flotation, gravity separation and magnetic separation. Flotation and magnetic separation are the most widely used methods. Through flotation and magnetic separation processes, useful minerals and gangue minerals in low-grade iron ore can be effectively separated, the grade of iron ore can be improved, and the demand for high-grade raw materials in the steel industry can be met. The following article will introduce the flotation process, magnetic separation process and combined beneficiation process in detail to help you better understand iron ore flotation and magnetic separation technology.
Use the table of contents below to navigate through the guide:
01Iron ore flotation separation process
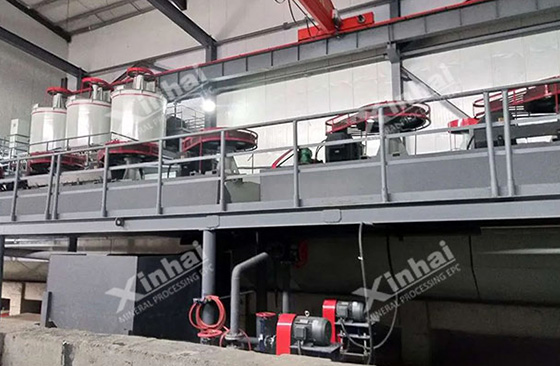
Iron ore flotation utilizes the differences in physical and chemical properties of the mineral surface. By adding flotation agents and bubbles, useful minerals are attached to the bubbles and then float to the foam layer, thereby achieving the separation of iron ore and gangue minerals. The iron ore flotation system mainly includes flotation machines, stirring tanks, bubble generators, etc. There are many influencing factors in the flotation of iron ore, such as pulp concentration, stirring intensity, aeration volume and dosage. Appropriate adjustment and optimization of these factors can improve the flotation effect of iron ore.
02Iron ore magnetic separation process

Iron ore magnetic separation is mainly based on the magnetic difference between magnetic minerals and non-magnetic minerals in iron ore. These different magnetic minerals are separated by magnetic separators, thereby improving the grade and recovery rate of iron ore. Iron ore magnetic separation can be divided into two methods: dry magnetic separation and wet magnetic separation. The specific selection needs to be based on the characteristics of the ore and production requirements. Common equipment for iron ore magnetic separation includes magnetic separators, magnetic pulleys, dry magnetic separators, etc. Among them, magnetic separators are the most commonly used equipment, which can be divided into permanent magnetic separators and electromagnetic magnetic separators. Permanent magnetic separators are usually used to process simpler ores, while electromagnetic magnetic separators are suitable for processing ores with strong magnetism or requiring strong magnetic fields. The intervention of magnetic separation equipment can help further improve the iron ore separation effect.
03What should be paid attention to in the magnetic separation of iron ore?
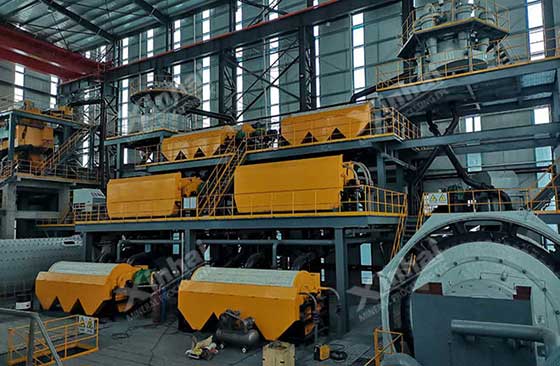
1. Selection and use of magnetic separation media
The commonly used magnetic separation media for iron ore magnetic separation are permanent magnets, electromagnets and superconducting magnets. Permanent magnets can be used in small equipment because of their long-term stable magnetic field. Electromagnets are more flexible, while superconducting magnets can generate strong magnetic fields. The selection of specific magnetic separation media needs to be based on the properties of the ore, the processing volume and the type of equipment. The magnetic field strength should be checked regularly during use to ensure the magnetic separation effect of iron ore.
2. Control of magnetic separation operating parameters
During the magnetic separation process, it is necessary to control parameters such as magnetic field strength, ore feeding speed, slurry concentration, ore particle size, etc. These parameters will affect the magnetic separation effect of iron ore. Therefore, the optimal operating parameters are determined during the ore dressing test, and automatic control technology is used to achieve real-time monitoring and adjustment of these parameters.
04Combined application technology of iron ore flotation and magnetic separation
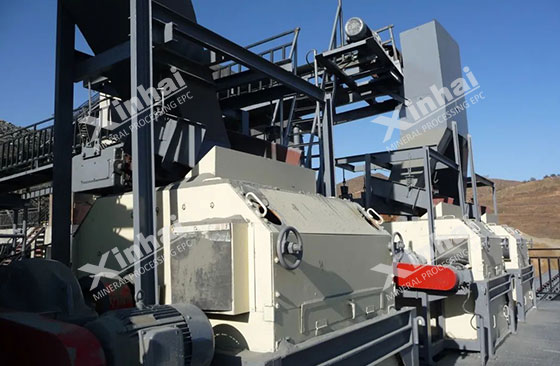
When dealing with complex and difficult iron ore, it is necessary to combine flotation and magnetic separation technology to give full play to their respective advantages to improve the separation efficiency of iron ore and the quality of concentrate. Combined beneficiation technology can also effectively remove impurities, improve the purity and quality of iron ore products, while reducing the energy consumption of the entire production line and improving the economic benefits of the beneficiation plant.
When using combined beneficiation technology, it is necessary to control the dosage of reagents, operating conditions, magnetic field strength and regular equipment maintenance. Since the dosage of reagents in the flotation process has a great influence on the effect, it needs to be adjusted according to the actual situation. The adjustment of process operating conditions includes pulp concentration, pH value, temperature, etc. These factors will have an important impact on product quality. Appropriate adjustment of the magnetic field strength during magnetic separation can ensure the recovery rate and grade of magnetic minerals. In addition, regular maintenance and maintenance of flotation equipment and magnetic separation equipment should be carried out to ensure the normal operation of the equipment.
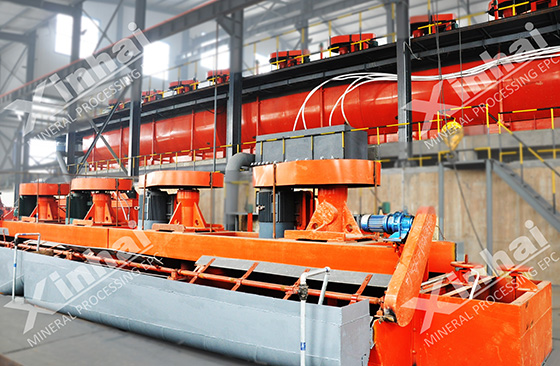
The above content is a brief introduction to iron ore flotation, magnetic separation and combined processes. No matter which beneficiation process is used, it is necessary to select according to the properties of the minerals and production requirements, control the influencing factors, and improve the separation efficiency and product quality. With the continuous development of technology, the flotation and magnetic separation processes of iron ore will be more intelligent in the future. Through real-time monitoring, data analysis and other means, the precise control and optimization of iron ore beneficiation process parameters can be achieved, and the utilization efficiency of iron ore resources and the overall economic benefits of the beneficiation plant can be improved.