Amid increasing volatility in global iron ore prices, reducing costs and
improving efficiency in ore dressing plants have become critical to corporate
competitiveness. Drawing on advanced process practices and equipment selection
data, this article explores how systematic design can help reduce the processing
cost per ton of iron ore.
Use the table of contents below to navigate through the guide:
01General Layout Of Iron Ore Concentrator
1. Three-Dimensional Layout
"Crushing–Screening–Dry Selection" Trinity Workshop Design: This innovative layout model closely integrates the three key stages of
crushing, screening, and dry selection.
Simulating Material Flow with BIM Technology: The
application of BIM technology enables accurate simulation of material flow
throughout the entire mineral processing process. It helps the beneficiation
plant optimize the vertical height difference between the crushing system and
the grinding and selection system, thereby reducing energy consumption caused by
secondary material lifting.
2. Terrain Energy Conversion Technology
Utilizing a 5°–8° natural slope to achieve gravity-driven slurry
flow:
This design takes full advantage of the terrain, reducing dependence on
pumping equipment and thereby lowering energy consumption and maintenance
costs.
Innovative Stepwise Thickener Design:
The stepwise thickener leverages natural elevation differences to create a
gravity-driven dewatering system. By arranging the thickeners in a stepped
layout, the slurry undergoes stage-by-stage thickening and dewatering under
gravity. This not only improves dewatering efficiency but also reduces reliance
on additional dewatering equipment, further cutting down energy use and
operational costs.
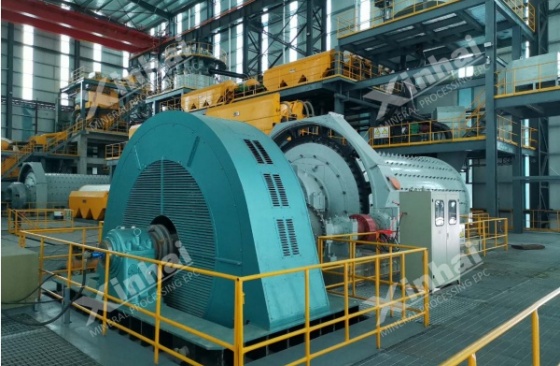
02Process Design of Iron Ore Concentrator
1. Crushing Process Design
Combination of high-pressure roller mill and two-stage closed-circuit
crushing: This combined process enables stable control of the mill feed particle
size to below 8 mm.
Compared with the traditional three-stage crushing process, it reduces the
ball mill’s power consumption by 1.8 kWh/t.
2. Pre-selection and Waste Disposal
Dry magnetic separation after coarse crushing: After coarse
crushing, 18%–25% of waste rock can be discarded through dry magnetic
separation. This effectively reduces the amount of ore entering subsequent
processing stages, thereby lowering overall mineral processing costs.
Wet pre-selection (magnetic separator + spiral chute combination): This combined process increases the ore grade by 5%–8%.
By improving the feed grade, the quality of the final concentrate is enhanced,
thus increasing the overall economic benefits for the enterprise.
3. Precise Control of the Grinding and Separation System
Two-stage grinding + three-stage separation: The first stage
uses a grid type ball mill for coarse grinding and tailings removal, while the
second stage employs a vertical mill for fine grinding. This process enables
precise control of the grinding particle size based on the ore’s characteristics
and processing requirements, thereby improving overall grinding efficiency.
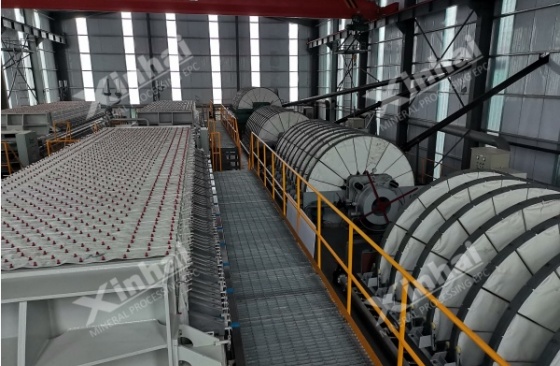
03Iron Ore Concentrator Equipment Selection
1. Crushing Equipment
Cone Crusher: Equipped with PLC-controlled automatic
discharge port adjustment, increasing the product qualification rate to 92%.
Impact Crusher: Capable of achieving 80% of product below 15
mm. This crusher performs well when processing ores within a specific particle
size range and meets the particle size requirements of downstream processes.
2. Grinding System
Large Ball Mill: Compared with the small ball mill, the unit
processing cost is reduced by 28%. Large-scale equipment effectively lowers unit
costs when processing large ore volumes.
Cyclone Unit: Classification efficiency exceeds 85%.
Efficient classification ensures that the grinding product meets the particle
size requirements for subsequent separation, improving the overall mineral
processing efficiency.
3. Technological Advancements in Separation Equipment
Full Magnetic System Magnetic Separator: With a background
field strength of 0.8 T, it reduces tailings grade by 0.7 percentage points.
High-intensity magnetic separators significantly enhance magnetic separation
efficiency, lower tailings grade, and increase resource recovery.
Flotation Column + Mechanical Agitation Flotation Cell Combination:
This integrated process reduces reagent consumption by 15%. Optimizing
flotation equipment and processes helps cut reagent costs while improving
flotation performance.
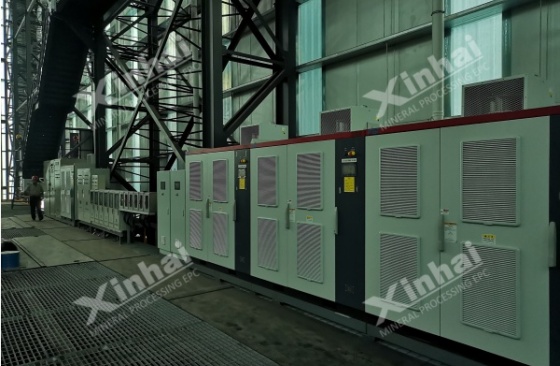
04Resource Cycle of Iron Ore Concentrator
1. Deep Utilization of Tailings Value
Tailings Dry Stacking System(deep cone thickener + plate-and-frame filter
press):
Capable of achieving tailings moisture content below 18%, meeting the
requirements for construction aggregate production. This dry discharge system
not only addresses tailings disposal challenges but also enables the conversion
of tailings into valuable construction materials, thereby realizing resource
recycling.
2. Closed-Loop Water Circulation Design
Plant-front Return Water System (inclined tube sedimentation + high-gradient
magnetic separation):
Reduces fresh water consumption to as low as 0.15 m³/t. This efficient return
water system maximizes water recovery and utilization, reduces dependence on new
water, and lowers production costs.
Rainwater Collection Pool with a Capacity Equivalent to Three Days of Water
Use:
Effectively responds to extreme weather conditions to ensure continuous
production. The implementation of a rainwater collection system increases water
reserves and enhances the ore dressing plant’s production reliability during
adverse weather events.
05Intelligent Control System: Digital Twin Factory Construction
1. DCS Central Control Platform
Real-time monitoring of 2000+ process parameters: By monitoring a large
number of process parameters in real time, the production status of the ore
dressing plant can be accurately understood, enabling timely detection and
resolution of issues.
Grinding mill load fluctuation controlled within ±3%: Accurate control
ensures stable mill operation, improves grinding efficiency, and reduces energy
consumption.
Intelligent dosing system (X-ray fluorescence analyzer + fuzzy control): The
precision of reagent dosage reaches ±2%. The intelligent dosing system adjusts
reagent amounts based on ore properties and process requirements, improving
flotation efficiency and reducing reagent costs.
2. Predictive Maintenance System
Vibration analyzer + infrared thermal imaging for 48-hour advance warning of
equipment failure: Advanced monitoring equipment detects potential failures in
advance, enabling timely maintenance, reducing downtime, and improving
production efficiency.
Digital twin model simulates the effects of process adjustments: Trial and
error costs are reduced by 70%. The digital twin model simulates process
adjustments in a virtual environment, helping avoid the high costs and risks
associated with large-scale trials in actual production.
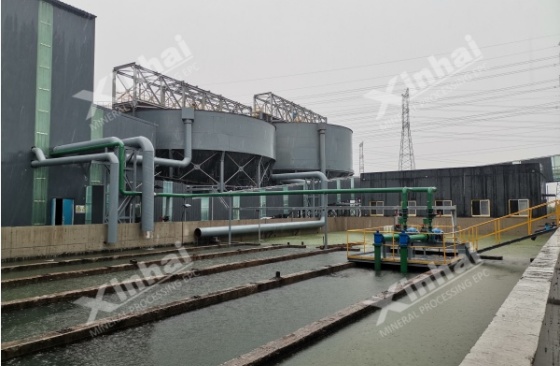
06Energy-saving Technology Matrix: Innovation from Equipment to System
1. In-depth Application of Frequency Conversion
Technology
The power-saving rate of slurry pump frequency conversion transformation
reaches 25% - 40%: The application of frequency conversion technology can
accurately control the equipment’s operating speed, reducing energy consumption
based on actual production needs.
Application case of permanent magnet motor in magnetic separator drive
system: An annual electricity saving of 180,000 kWh. Permanent magnet motors,
known for their high efficiency and energy-saving characteristics, can
significantly reduce equipment energy consumption.
2. Construction of Waste Heat Recovery Network
The waste heat of the ball mill cylinder (80 - 120℃) is used for ore
pre-drying, resulting in a 30% reduction in dryer energy consumption. By
recovering waste heat from the ball mill for ore pre-drying, energy consumption
in the dryer is reduced, and drying efficiency is improved.
Air compressor waste heat recovery for the bathing system: Annual coal cost
savings of 60,000 US dollars. Waste heat recovery from air compressors helps
save significant energy costs and improves overall energy utilization
efficiency.
Conclusion
Through the system integration of the above six strategies, modern
iron ore concentrators have achieved a remarkable transformation from "extensive
production" to "precise control." According to recent data from the
concentrators, the cost of concentrate can be controlled at US$24-35/ton for
newly built concentrators with optimized designs, providing a practical
technical path for economically viable iron ore concentrators.