With the rapid development of modern science and technology, quartz glass, as a basic material for high-tech industries, has been applied in many fields, including construction, chemical industry, lighting, atomic energy, radio electronics, semiconductor technology, instrument manufacturing, aerospace, high-frequency technology, non-ferrous metallurgy, and national defense. The demand for quartz and its products continues to grow, but the depletion of global crystal resources has made the search for crystal substitute raw materials an important issue in the production of quartz glass. Although artificial crystal, artificial synthetic quartz glass and natural silica processing and purification methods can be used as alternatives, due to high energy consumption, high cost and difficulty in production, the production process of high-purity quartz sand has become the key way to manufacture quartz glass.
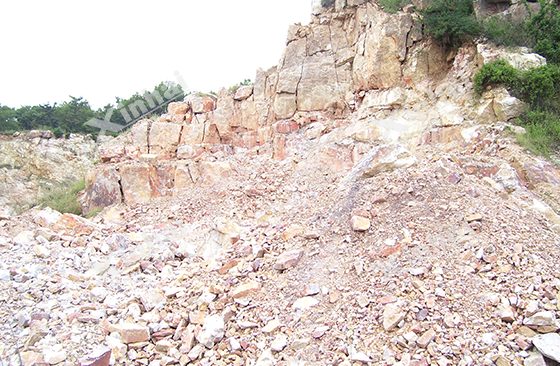
The production process of high-purity quartz sand involves multiple steps, each of which requires strict technical control to ensure the purity and quality of the final product. The following is a detailed production process from raw material processing to the final product:
Use the table of contents below to navigate through the guide:
01Vine Quartz Sand Processing Process
As a primary vein ore, vein quartz has the characteristics of pure quality, so its processing technology occupies an important position in the entire production process. The main steps of vein quartz processing include:
- Ore screening: First, manual hand selection is carried out to divide the vein quartz ore into high-quality and milky ordinary quartz, and processed into ultra-high purity quartz sand and acid-washed high-purity quartz sand of different specifications. Manual hand selection workers rely on their rich experience and ability to identify quartz quality to divide the ore into two categories.
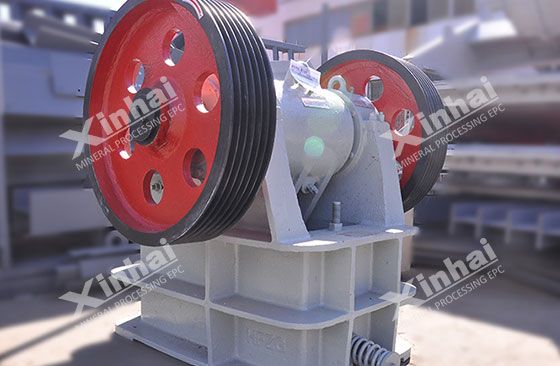
- Crushing processing: After manual hand selection, the vein quartz is initially crushed using jaw crusher and roller crushers. If further purification is required, the crushed raw materials will be manually selected again. The raw materials that do not need further purification are directly put into the gravel mill for grinding, and then screened and graded to obtain quartz sand products of different particle sizes.
02Quartz sandstone processing technology
The processing technology of quartz sandstone is relatively simple, because its ore quality is high and no manual selection is required. The main processing steps include:
- Processing: High-quality quartz sandstone ore is directly processed to produce 11 different quartz sand products.
- Iron removal: All processed quartz sand products are treated by iron removal devices. Before packaging, the mixed natural iron and strong magnetic minerals are removed by a strong magnetic field to ensure that the iron content of the product is less than 0.05%.
03Quartz sand purification process
The purification process of quartz sand is a key step to ensure the quality of high-purity quartz sand products. According to different needs, the purification of quartz sand is divided into two processes: ultra-high purity quartz sand processing and ordinary high-purity quartz sand processing.
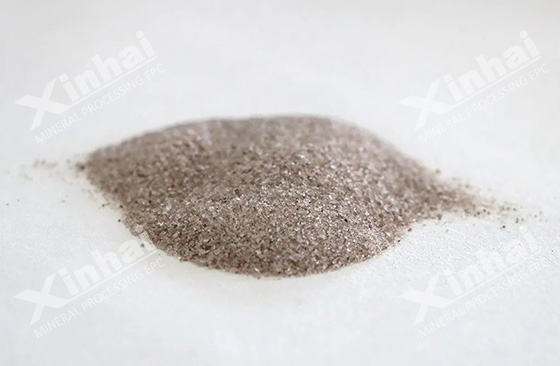
1. Ultra-high purity quartz sand processing
Ultra-high purity quartz sand requires extremely high purity and the lowest iron content. Its production process includes:
- Crushing and grading: After the raw materials are crushed and graded, they are manually selected to remove quartz blocks with small bubbles, milky white crystal bands, foreign impurities, color spots and slag. The remaining quartz is then ground and graded to separate 40~70 mesh and 70~140 mesh as raw materials for processing ultra-high purity quartz sand.
- Magnetic separation: Use a strong magnetic field magnetic separator (magnetic field strength of 12000 Oersted) to remove iron-containing materials to ensure that the Fe2O3 content in the product is less than 2ppm.
- Flotation: Add hydrofluoric acid, amine collectors, fuel oil and pine oil to the acidic medium for flotation to float out heavy minerals such as feldspar and obtain quartz sand concentrate.
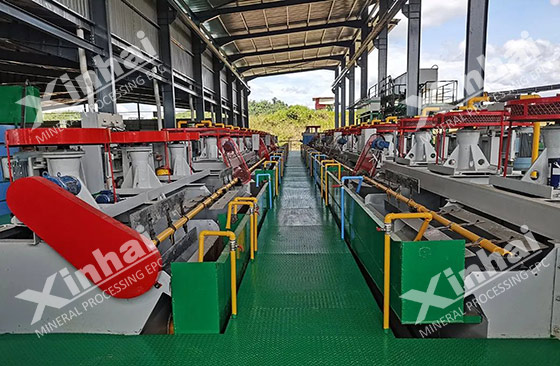
- Chemical treatment: Use acid leaching to treat impurities in quartz sand. Hydrochloric acid converts iron substances into ferric chloride for dissolution, and hydrofluoric acid acid leaching of quartz sand can more effectively remove iron and other impurities. During acid leaching, add nitric acid in an appropriate amount to accelerate the reaction process. In the air-stirred leaching tank, the slurry reacts at a temperature above 85°C for 1-2 hours, and after sand settling, it is washed with purified water until the aqueous solution is neutral. After filtration and drying, ultra-high purity quartz sand containing more than 99.99% SiO2 and less than 2ppm Fe2O3 can be obtained.
2. Ordinary high-purity quartz sand processing
The processing of ordinary high-purity quartz sand is relatively simple, and the main processes include:
- Pickling treatment: Use the quartz sand in the waste acid solution to pickle and treat it to ensure that the product contains more than 99.96% SiO2 and less than 5ppm Fe2O3. The waste acid solution after pickling is treated in a neutralization tower and can only be discharged after meeting the emission standards.
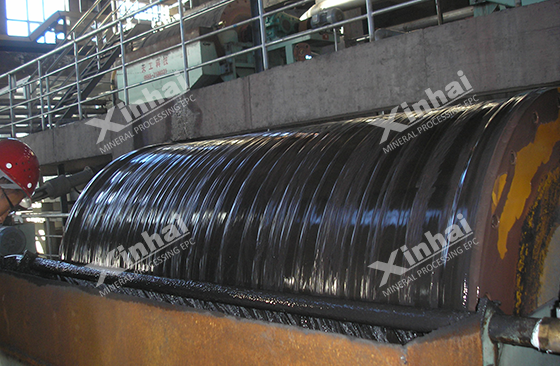
The production process of high-purity quartz sand is the key to ensuring the high quality and high purity of quartz glass. Through precise raw material processing, advanced purification technology and strict quality control, we can effectively cope with the challenges brought by the depletion of crystal resources and promote the sustainable development of the quartz glass industry. In the future development, continuous optimization of production processes and exploration of new materials will be important directions for improving the level of quartz glass manufacturing.