Fluorspar ore is an important non-metallic mineral resource, widely used in metallurgy, chemical industry, pharmaceuticals, building materials and other fields. With the increasing demand for industrial development, the supply of high-quality fluorite is particularly important. However, the efficient utilization of fluorite resources depends on scientific and reasonable mineral processing technology. To this end, it is necessary to conduct in-depth research on the fluorspar beneficiation process, especially how to effectively separate fluorite from gangue minerals, in order to maximize the utilization of resources.
Use the table of contents below to navigate through the guide:
01Basic principles of fluorspar ore beneficiation
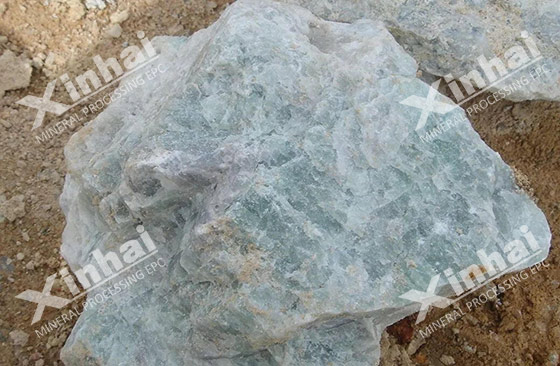
The main component of fluorspar ore is calcium fluoride, while gangue minerals are mainly composed of siliceous minerals such as quartz and feldspar. The differences in physical and chemical characteristics such as density, particle size, and surface properties between fluorite and gangue become the basis of flotation beneficiation. In the beneficiation process, these differences are used to achieve efficient separation of fluorite through a series of process steps such as grinding and flotation.
02Limitations of traditional fluorspar ore beneficiation
The traditional fluorspar ore flotation process usually uses a grinding and flotation process. After the raw ore is ground to a certain fineness by ball mill equipment, it is floated using conventional flotation agents such as oleic acid, sodium carbonate and water glass, which can theoretically achieve satisfactory separation effects. However, in actual operation, the effects of these traditional processes are often unsatisfactory, mainly reflected in the following aspects:
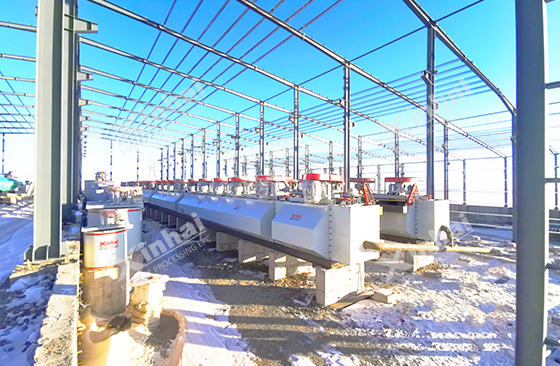
1. Limitations of reagent selection: Traditional reagents may not be able to achieve the expected separation effect under the characteristics of some fluorite ores, resulting in low fluorite recovery rate.
2. The influence of grinding particle size: The selection of particle size during grinding is crucial to the flotation effect. Different particle sizes will affect the characteristics of the mineral surface, and thus affect the flotation results.
3. Inadaptability of flotation process: Traditional flotation process is often lack of pertinence when facing different ore types, which easily leads to low beneficiation efficiency.
Therefore, exploring suitable grinding process, flotation reagents and flotation process is the key to achieving efficient fluorite beneficiation.
03Innovation in fluorspar ore grinding process
In fluorspar beneficiation, grinding is a key link that affects the subsequent flotation effect. By studying different grinding equipment, grinding time and particle size distribution, the beneficiation efficiency of fluorspar can be significantly improved.
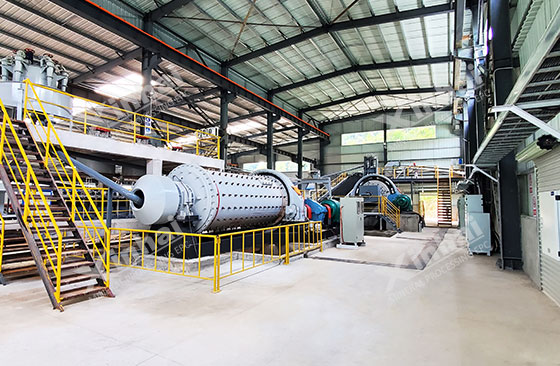
1. Selection of grinding equipment: Although the traditional ball mill can achieve a certain fineness during the grinding process, it has certain shortcomings in terms of energy consumption and wear. In recent years, high-efficiency grinding equipment, such as ultra-fine grinding and impact mills, has been gradually introduced. These equipment not only improve grinding efficiency, but also optimize particle size distribution and improve flotation performance.
2. Control of grinding time: Grinding time directly affects the fineness of the ore and the flotation effect. Through experimental research, reasonable control of grinding time can achieve a balance between fineness and particle shape and avoid mineral surface damage caused by over-grinding.
3. Optimization of particle size distribution: During the grinding process, optimizing the particle size distribution can not only improve the recovery rate of fluorspar, but also reduce the mixing of gangue minerals. The method of graded grinding and graded flotation can effectively improve the mineral processing effect.
04Selection and application of fluorspar ore flotation reagents
Flotation reagent is another key factor in the mineral processing process. Its selection and use directly affect the recovery rate and product quality of fluorspar.
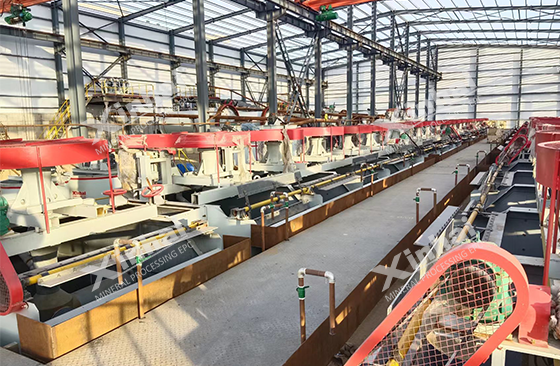
1. Development of new flotation reagents: In recent years, with the continuous advancement of chemical technology, the research on new flotation reagents has made significant progress. For example, the use of emerging materials such as biochemical agents and green agents can improve flotation efficiency without increasing environmental burden.
2. Optimization of chemical formula: Through experiments, exploring the effects of different chemical combinations, a more reasonable flotation chemical formula can be formulated, thereby improving the separation efficiency of fluorite and gangue.
3. Precise control of reagent dosage: In the flotation process, control of reagent dosage is the key to affecting the flotation effect. By real-time monitoring of the physical and chemical properties of the slurry during the flotation process and dynamically adjusting the dosage of reagents, the mineral processing efficiency can be effectively improved.
05Optimization of fluorspar ore flotation process
The reasonable design of flotation process is an important guarantee for achieving efficient fluorite beneficiation. The following are some optimization and innovation directions:

1. Optimization of flotation process: According to the characteristics of different ores, the flotation process is flexibly adjusted, and one, two or even multiple flotation stages are adopted to achieve the best separation effect. For example, for some difficult-to-select fluorite ores, the use of multiple flotation stages can effectively improve the recovery rate.
2. Regulation of bubble characteristics: The characteristics of bubbles have a huge impact on the flotation process. By adjusting the generation mode and characteristics of bubbles, the flotation process can be optimized and the flotation effect of fluorite can be improved.
3. Process integration and automation: Introduce modern automated control systems to realize intelligent management of the flotation process and improve the stability and consistency of the beneficiation process.
In summary, the efficient realization of fluorspar ore beneficiation requires systematic research and optimization from multiple aspects such as grinding, flotation reagents, and flotation technology. In the context of increasingly tight resources, exploring suitable fluorite beneficiation technology is not only an important way to promote efficient utilization of resources, but also an important measure to promote the sustainable development of the mining industry.