Grinding operations and grading operations together constitute the grinding and classifying process. Grinding process mainly includes ball mills, rod mills, autogenous grinding, semi-autogenous grinding, etc. Classifying process are divided into three types: pre-classifying, inspection classifying and control classifying. The closed circuit consisting of grinding operation and classifying operation is called closed circuit grinding process. When the grinding operation does not form a closed circuit with the classifying operation, it is called an open circuit grinding process. There are various grinding and classification processes that can be constructed in actual production, and they need to be combined according to the characteristics of the ore and the requirements of the ore dressing process. When formulating the grinding and classifying process, you need to consider how to determine the number of grinding sections, whether it is closed-circuit or open-circuit grinding, and the application conditions of different classifying operations. The following will introduce you to how to formulate the grinding and classifying process based on these issues.
Use the table of contents below to navigate through the guide:
01How to determine the number of grinding process sections?
The factors that affect the determination of the number of grinding process stages include the grindability of the ore, the mineral particle size and distribution characteristics, and the structure of the ore dressing process. When determining the grinding process, the beneficiation test results and plant scale data should be taken into consideration. General situations can be divided into the following categories:
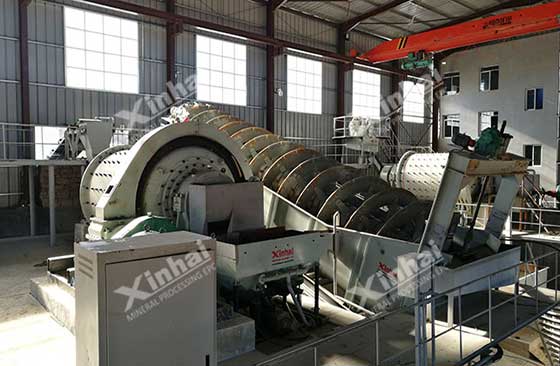
(1) When the ore contains a large amount of mud or a large amount of clay minerals, it is difficult to achieve the expected results using conventional crushing processes, and it will also increase the complexity of the ore washing operation. At this time, the wet semi-autogenous grinding process can be considered. In addition, depending on the grinding fineness requirements, a single-stage semi-autogenous grinding process or a semi-autogenous grinding + ball grinding process can also be applied.
(2) When the particle size of the selected ore is required to be less than 0.2mm and the proportion is 55%~65%, the following three situations can be considered:
① If the ore is broken to 10~15mm, a closed-circuit grinding process can be used;
② If the ore is crushed to 20~25mm and the ore dressing plant is large-scale, you can choose a two-stage grinding process with the first stage open. The first stage of grinding equipment can use rod mill;
③If the ore is crushed to 300~350mm and the ore properties are suitable for autogenous grinding, the process of autogenous grinding + ball milling, semi-autogenous grinding + ball milling or autogenous grinding + ball milling + fine crushing can be used.
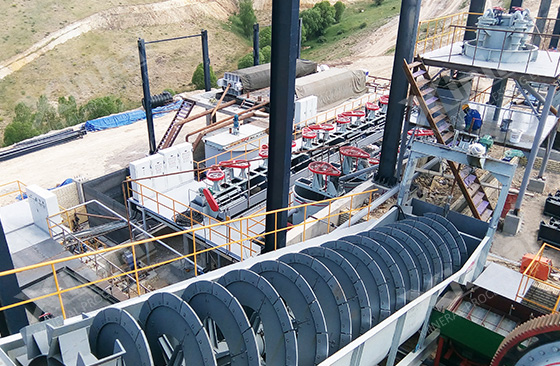
(3) When the ore particle size is required to be less than 0.15mm and the content is greater than 70%~80%, the following three situations can be considered:
① Ore with uniform particle size is generally processed by the conventional crushing process, and the ore concentrator generally adopts a two-stage fully closed-circuit continuous grinding process.
② When the ore with uneven particle size is selected in stages, a two-stage fully closed-circuit stage grinding process is generally selected;
③In order to simplify the process, small mineral processing plants often adopt a closed-circuit grinding process, but need to add overflow control classification.
(4) When the ore particle size is required to be less than 0.074mm and the content is greater than 90%, the following two situations can be considered:
① When processing ores with uniform particle size, choose to use a two-stage fully closed-circuit continuous grinding process. Add overflow control classification in the second stage grinding classification operation;
② When processing ores with uneven particle size, choose to use a multi-stage grinding process. When processing non-ferrous metal ores, useful minerals may become muddy in large quantities. Therefore, multi-stage grinding and multi-stage separation processes can be used to effectively avoid this situation.
In summary, the design of the grinding process needs to be selected based on the properties of the ore and the embedded characteristics of useful minerals. After comparison, a reasonable solution is determined to ensure effective grinding conditions and reduce unit power consumption.
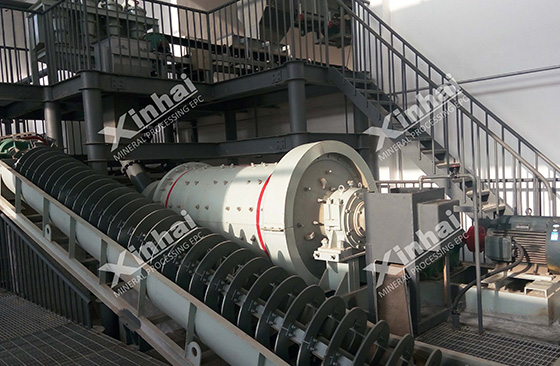
02How are different classifying processes applied?
From the above, it can be seen that classifying operations can be divided into three types: pre-classifying, inspection classifying and control classifying. Different types of classifying processes have different purposes and therefore the conditions for their application are also different.
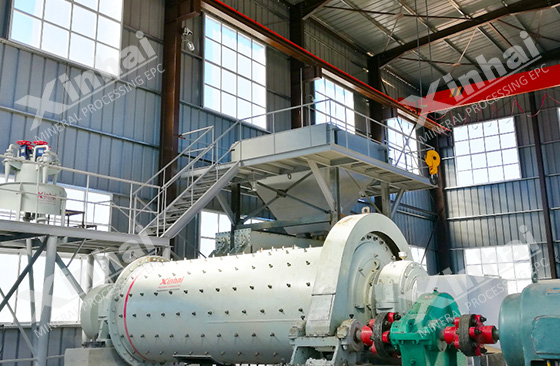
(1) Pre-classifying: Pre-sort the qualified particle sizes in the ore feed, thereby relatively improving the processing capacity of the grinding machine. Pre-grading can also separate slime and harmful soluble salts in advance to facilitate separate processing and improve the sorting index.
(2) Inspection classifying: The purpose is to ensure that the particle size of the grinding product is qualified. Inspection and classification can return coarse-grained minerals to the grinding equipment for re-grinding. The ore throughput per unit time of the grinding equipment increases, the grinding efficiency is improved, and the over-crushing phenomenon is reduced.
(3) Overflow control classification: The purpose is to obtain a finer overflow fineness through one stage of grinding, or to achieve stage separation in one stage of grinding, that is, the coarser overflow after separation The tailings are then controlled and classified to obtain finer overflow products for re-selection, and the coarse-grained products are returned for regrinding. In production, return sand control classification is also used, the purpose of which is to reduce the fine-grain content in the return sand.
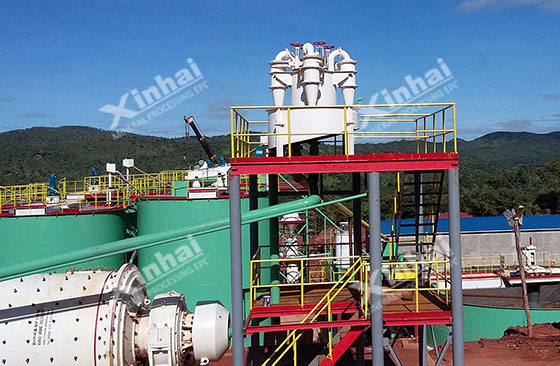
The above is a brief introduction on how to determine the number of grinding process stages and the application conditions of different classification operations. In actual production, the formulation of grinding classification needs to be based not only on the mineral processing test results, but also on the production requirements and production budget of the mineral processing plant. Developing a reasonable and efficient grinding and classification process can not only improve the efficiency of the production line, but also improve the economic benefits of the entire mineral processing plant.