In the process of mining and utilization of phosphate rock resources, the treatment of ore tailings is also an important part of resource utilization. There is also a part of phosphate minerals in the phosphate ore tailings. By recycling the concentrate part of the tailings, the recovery rate of the phosphate ore resource concentrate can be improved and the waste of resources can be reduced. This article will introduce you to two phosphate ore tailings treatment methods, namely physical separation and chemical treatment. Through these two treatment methods, valuable minerals in phosphate ore tailings can be effectively recovered.
Use the table of contents below to navigate through the guide:
01Physical separation of phosphate ore tailings
Physical separation methods aim to separate valuable minerals or components from tailings through different physical properties. Common physical separation methods include gravity separation, magnetic separation and flotation separation.
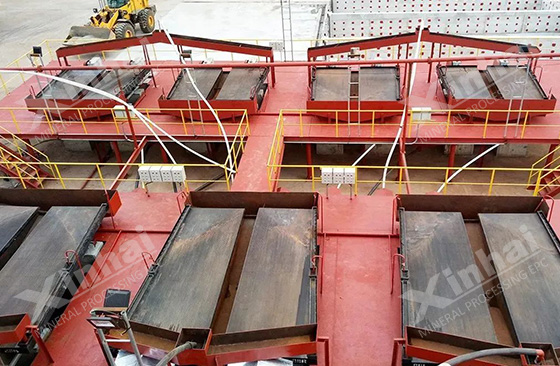
a. Gravity separation:
Gravity separation is a method based on differences in particle density. It is usually accomplished through the use of equipment such as jigs and shakers. In phosphate ore tailings treatment, gravity separation can be used to separate phosphate minerals from other gangue minerals or impurities, such as sand and clay. Before gravity separation, tailings may require pre-treatment, such as screening or crushing, to ensure that the particles are of a suitable size for the separation operation. During re-selection, gravity causes particles to separate according to density differences, thereby achieving separation. Phosphate minerals typically settle to the bottom, while lightweight materials such as sand and clay float on the surface. In practical applications, it may be necessary to combine other separation methods, such as magnetic separation or flotation, to achieve the best recovery effect.
b. Magnetic separation:
-Magnetic separation is a method of separating magnetic and non-magnetic substances through differential magnetism. This is particularly useful for recycling tailings containing iron minerals. By introducing a magnetic separation device into phosphate tailings, iron minerals can be separated from other minerals. First, ensure that the phosphate ore tailings are refined for better magnetic separation. Select appropriate magnetic separation equipment. Commonly used equipment includes magnetic separators, permanent magnet drum magnetic separators or wet high-intensity magnetic separators, which are capable of generating magnetic fields strong enough to separate magnetic and non-magnetic materials. When sorting, it is necessary to set the magnetic field strength, rotation speed and feeding speed of the equipment according to the properties of the tailings and the characteristics of the magnetic materials to avoid affecting the separation efficiency.
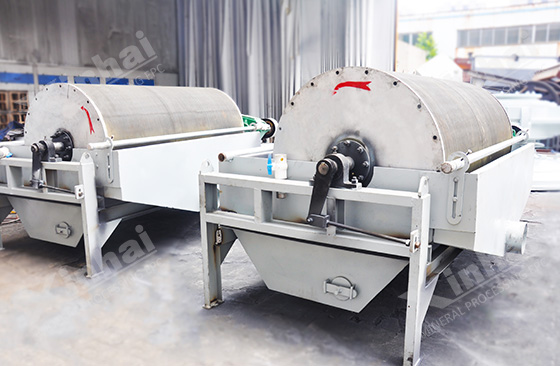
c. Flotation separation:
Flotation is a widely used ore processing method that uses bubbles to float valuable minerals to the surface of a liquid, where they are then collected. In phosphate ore tailings treatment, flotation can be used to separate phosphate minerals. Usually, the flotation process requires the addition of chemicals to enhance the separation effect. Flotation agents used in phosphate ore tailings treatment usually include collectors, frothers and modifiers. Proper selection and dosing of these agents is critical for efficient treatment of phosphate ore tailings.
02Chemical treatment of phosphate ore tailings
The process of chemically treating phosphate ore tailings typically involves using chemical methods to alter the chemical properties in the tailings in order to separate or extract valuable components. Common chemical treatment methods for phosphate ore tailings include acid leaching and alkali leaching.
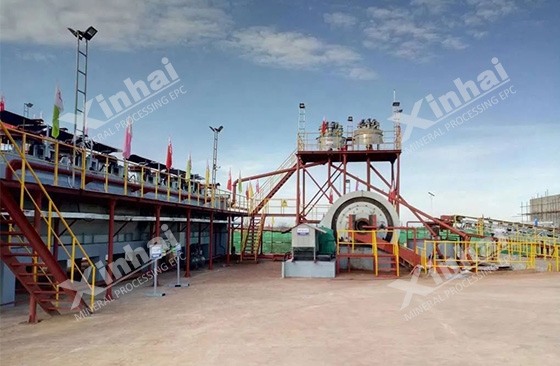
a. Acid leaching:
Acid leaching is a method of soaking tailings in an acidic solution to dissolve phosphate minerals from the tailings. Through acid leaching, phosphate minerals can be extracted from tailings to form a phosphate leachate, which can then be separated by precipitation or other methods. Generally, sulfuric acid is the most commonly used acidic solution, but other acids can also be used, depending on the nature of the tailings.
b. Alkali leaching:
Alkaline leaching is a method using an alkaline solution, often used to separate aluminum-containing materials. Alkaline solutions can convert aluminum minerals into soluble salts. Aluminum minerals can be dissolved from tailings through alkali leaching, and the aluminum salts can then be separated by precipitation or other methods. Sodium hydroxide or potassium hydroxide is the alkaline solution commonly used for alkaline leaching.
Depending on the specific composition of the tailings, other chemical reactions may be used to separate or extract the target components. But before using any chemicals to treat tailings, you should understand the minerals and chemicals present in the tailings.
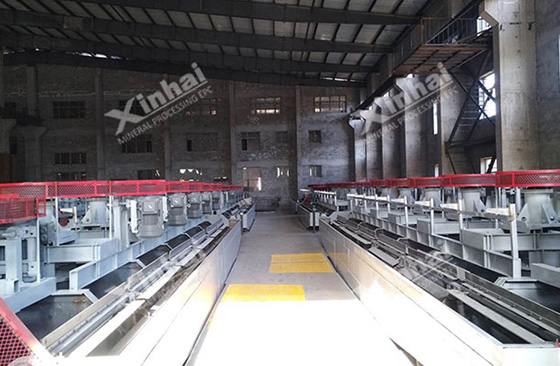
The above are the physical and chemical treatment methods of phosphate ore tailings. When using physical separation or chemical treatment methods, the appropriate method must be carefully selected to increase the recovery rate of valuable components and reduce the generation of waste. This often requires beneficiation test and process studies to determine the appropriate treatment method. In addition, environmental regulations must be adhered to to ensure that the treatment process has no adverse impact on the environment.