Quartz products are widely used in high-tech fields, such as electronic materials, silica film materials, optical fiber communication cable materials, quartz crucibles, quartz glass, silicon for semiconductors, etc. These high-performance materials have strict requirements on the quality of raw materials and require higher purity silica. Natural crystal stones are generally used as raw materials for these materials at home and abroad. However, due to the shortage of natural crystal stone raw materials and high prices, the demand for low-cost, high-quality high-purity quartz sand is one of the ways to solve this problem. This article will introduce you to a purification process of high-purity quartz sand, that is, the magnetic-flotation-acid leaching separation process of quartz sand.
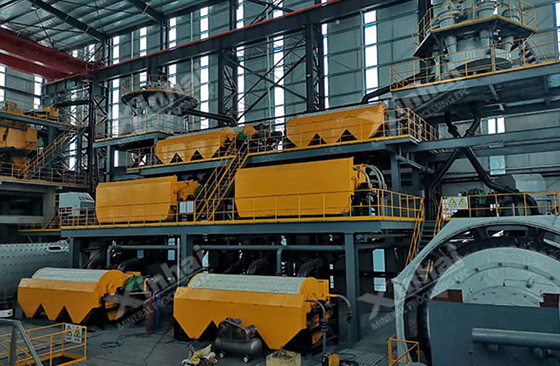
Use the table of contents below to navigate through the guide:
01High-purity quartz sand magnetic separation process
The impurities that affect the purity of quartz mainly include clay ores and iron oxides that contain aluminum elements. Among them, iron oxides mainly include iron ore and limonite. Since the hardness of these minerals is close to that of quartz, it is difficult to dissociate monomers during the crushing process, and most of them are conjoined with quartz particles. Therefore, magnetic separation can effectively remove this type of impurities.
When performing magnetic separation, a wet strong magnetic separator is generally used for primary separation, which can remove hematite, limonite, and hydrobiotite including conjoined particles and inclusions as much as possible. In addition, in order to improve the separation effect, attention should be paid to the ore concentration, magnetic field strength and flushing water volume during magnetic separation.
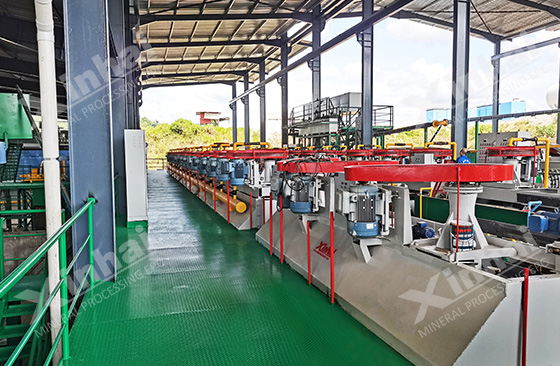
02High-purity quartz sand flotation separation process
As mentioned above, clay minerals are also one of the impurities that affect the purity of quartz. When minerals such as montmorillonite, hydrobiotite and illite are crushed and classified to deslime the ore, part of the clay impurities can be removed with mudification, but there are still some sheet-like structural components that do not have hydration characteristics. When dealing with such impurities, the mica flotation process can be used for separation.
When the mica flotation separation method is used, it can generally be divided into two forms according to the properties of the mineral raw materials:
The first one: In the alkaline pulp, an anion collector is used to directly select quartz through positive flotation, and mica enters the tailings.
The second method: In acidic pulp, cationic collectors are used to select mica through reverse flotation, and the tailings quartz is recovered.
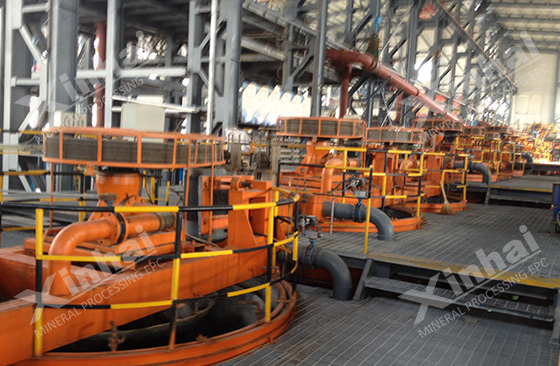
These two forms are based on the differences in the physical and chemical properties of the surface of quartz and mica, and show different affinities for air bubbles under the action of beneficiation agents. The former is more suitable for low-grade quartz raw materials with relatively simple structure, while the latter is more suitable for flotation of high-grade quartz raw materials. At the same time, the amount of flotation reagents used in flotation process should be controlled, and the combination of collector and foaming agent should be used to make them complement each other in the flotation process as much as possible, so that the concentrate yield can be increased and the impurity removal effect is better.
03High-purity quartz sand acid leaching process
After magnetic separation and flotation separation, the aggregate particles with more impurities in the raw ore have been basically removed, but there are still some harmful components or inclusions on the quartz particles. In order to remove such harmful impurities, acid leaching of quartz is required. Because quartz is acid-resistant (except HF), others will be dissolved by acid into soluble compounds, separated from the quartz particles in the liquid, and then removed by solid-liquid separation and water washing. Since most of the harmful components exist in the form of mineral aggregates, mixed acid acid leaching can be used, and the synergistic effect produced has a stronger effect of dissolving impurities.
In addition, the following aspects need to be paid attention to when carrying out acid leaching:
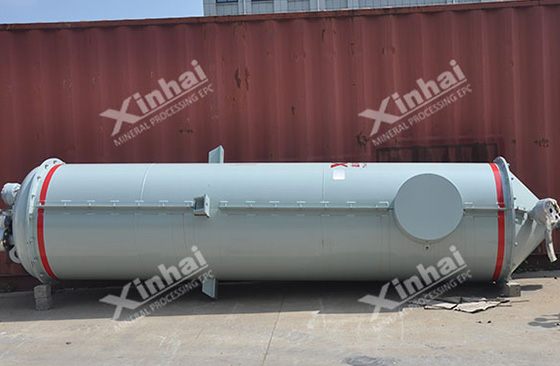
Acid solution concentration: When the acid solution concentration is too low, the impurity removal effect is not obvious and the output is low, and it takes a long time; when the acid solution concentration is too high, not only the corresponding purification cost increases. Moreover, the acid will intensify the corrosion of the equipment, increase the frequency of quartz washing, and at the same time cause problems such as difficulties in the discharge of washing water. Therefore, it is necessary to strictly control the concentration of the acid solution to avoid the loss of raw materials and equipment.
Reaction temperature: Cold acid treatment takes a long time, while hot acid can speed up the dissolution of impurities. When heating the acid liquid, it should be based on the type of acid liquid. Sulfuric acid has good thermal stability and is suitable for processing at high temperature. Hydrochloric acid has the characteristics of easy gasification and easy recovery, so the acid leaching temperature can be appropriately reduced.
Acid leaching time: Proper acid leaching time can ensure sufficient reaction between acid and impurities. In general, as time goes on, the impurity removal effect gradually improves. The initial effect of the reaction is more obvious, but as the concentration of the acid solution decreases, the dissolution rate of impurities decreases. Therefore, the acid leaching time is not easy to be too long, and the effect is better within 3-12 hours. During the acid leaching reaction, stirring can be strengthened. On the one hand, the chance of contact between the acid solution and the surface of the quartz particles is increased. On the other hand, the mutual collision and friction between the particles can prevent the dissolved impurities from depositing on the surface of the quartz particles, which is beneficial to improve the acid leaching reaction process. The effect of acid leaching to remove impurities.
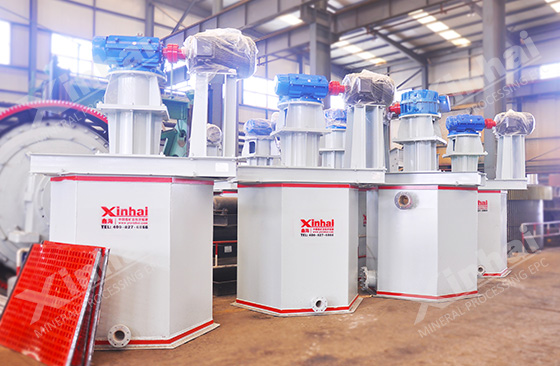
04High-purity quartz sand washing process
The surface of the quartz sand grains treated by acid leaching is covered with residual liquid and leached soluble impurities. Because in a dry environment, the acidic liquid is heated and evaporated to release harmful gases, pollute the environment and corrode equipment. At the same time, soluble impurities on the surface will reduce the purity of silica. Combined with the above, it is necessary to wash the quartz sand after acid leaching.
Washing is a diffusion process. Agitation can be carried out during the washing process to increase the speed of diffusion, which is beneficial to improve the washing effect. Because quartz sand is a dense particle, its pollution only occurs on the surface of the particle, so it can be washed with clean water first, and when it is neutral, it can be rinsed with ionized water to remove the clean water.
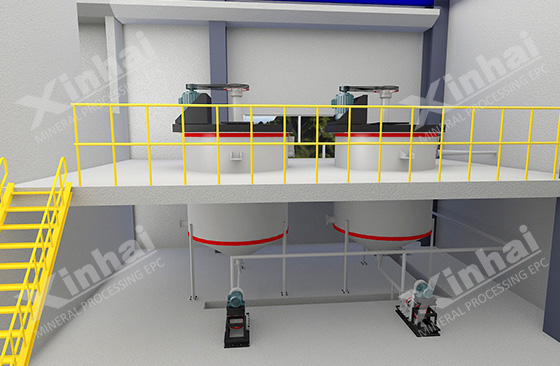
The above is the high-purity quartz sand magnetic-flotation-acid leaching separation process. When using silica to extract high-purity quartz sand, it is necessary to pay attention to the selection of raw materials and ore beneficiation techniques. Therefore, in order to select an efficient sorting process, it is necessary to conduct a beneficiation test and analysis of the raw materials to determine the composition and characteristics of the ore. Xinhai Mining can provide you with quartz sand beneficiation turnkey services, including beneficiation test, beneficiation process design, complete sets of equipment production and procurement, and subsequent transportation and installation. If necessary, welcome to consult.