The gold ore all sliming cyanidation process is a mature and efficient hydrometallurgical process. The process mainly includes ore crushing, grinding, slurry concentration, cyanide leaching and adsorption, desorption electrolysis and tailings treatment. It has the advantages of high recovery rate and strong applicability to achieve efficient leaching and recovery of gold.
Use the table of contents below to navigate through the guide:
01Gold ore cyanidation process: crushing and screening
In the stage of raw ore crushing and screening, in order to improve production efficiency, a two-stage one-closed circuit or three-stage one-closed circuit crushing and screening process is usually adopted. The coarse, medium and fine crushing processes are completed in sequence, and the screening is checked by the vibrating screen. The qualified ore particles after screening enter the powder bin for storage, and the unqualified ore particles return to the fine crushing cone crusher for re-crushing. This closed-circuit crushing and screening operation can not only reduce the over-crushing of the ore and improve the efficiency of the crusher, but also separate the useful minerals and gangue minerals as much as possible.
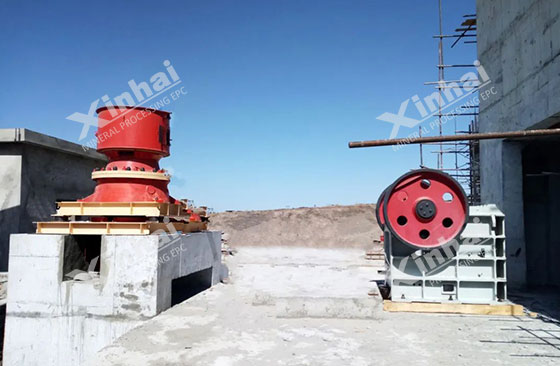
02Gold ore cyanidation process: grinding and classification
In the grinding and classification stage, in order to ensure that the ore is ground to a qualified particle size and the gold particles are fully dissociated, a two-stage two-closed-circuit grinding process is usually adopted to make the -200 mesh material content reach 80% to 95%. The material is sent to the grate ball mill for grinding via a belt conveyor, and some gold minerals are separated from gangue minerals in this process. In order to avoid the loss of coarse gold particles caused by over-grinding and improve the efficiency of mineral processing, a combined gravity separation process can be used to recover some of the gold particles in advance. In addition, in order to prevent impurities such as sawdust and gravel from affecting leaching, a chip removal screen is set at the overflow of the second stage grinding and classification to improve the leaching efficiency.
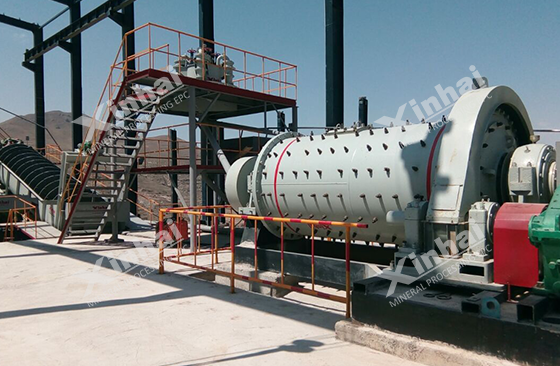
03Gold ore cyanidation process: thickening and slurry adjustment
After grinding and classification, the pulp concentration is usually 18% to 22%, which is not suitable for direct leaching. Therefore, the pulp must be thickened and slurry adjusted before leaching. The thickening operation uses sedimentation or centrifugal technology to increase the pulp concentration to 40% to 45% by adjusting the bottom flow of the thickener and adding an appropriate amount of flocculant to meet the cyanide-carbon adsorption reaction conditions; at the same time, by adjusting the amount of lime before grinding, the pulp pH value is adjusted to 10 to 11.
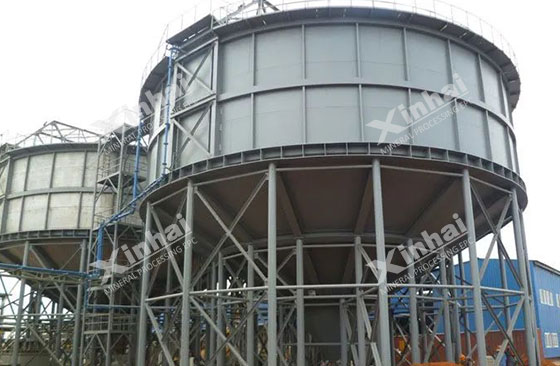
04Gold ore cyanidation process: cyanidation leaching and adsorption
The concentrated full mud pulp enters the stirring tank, sodium cyanide (NaCN) solution is added and fully stirred to convert the gold in the ore into gold cyanide complex [Au(CN)2]⁻ and dissolve it. To ensure the ideal leaching effect, the leaching process needs to control the leaching time, temperature and pulp concentration as well as the cyanide ion concentration (0.05%~0.08%) and oxygen content in the pulp. Usually, by adjusting the sodium cyanide dosage and the air pump valve, small bubbles with a diameter of 5~15mm are evenly dispersed on the surface of the pulp.
Subsequently, gold is recovered by CIP (carbon-in-pulp method) or CIL (carbon-in-pulp method):
CIP (carbon-in-pulp method): After leaching, an adsorption tank is added to allow the gold dissolved in the solution to be adsorbed by activated carbon.
CIL (carbon-in-pulp method): Leaching and adsorption are carried out simultaneously in the same tank to improve the recovery efficiency of gold.
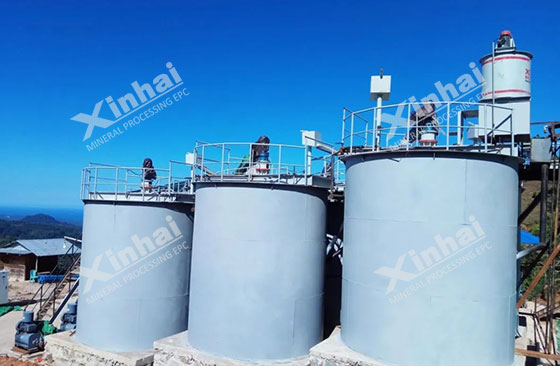
05Gold ore cyanidation process: desorption electrolysis
In the desorption electrolysis stage, the gold-loaded carbon is first sent to the linear vibrating screen for cleaning and separation through a carbon pump or air lift, and then transferred to the desorption column. The gold-loaded carbon in the desorption column is immersed in a solution made of a mixture of NaCN and NaOH. Under the conditions of heating to 90℃~95℃ and pressurization, the gold-cyanide complex [Au(CN)2]- is replaced by adding easily adsorbed anions using a high temperature and high pressure desorption process to form a gold-rich precious liquid. Subsequently, the desorbed precious liquid enters the electrolytic cell, where electrolysis is carried out, and the cations move toward the cathode plate, causing the gold to precipitate at the bottom of the electrolytic cell to form gold mud. After pickling and impurity removal, the gold mud can be directly smelted into gold ingots with a purity of more than 99.99%.
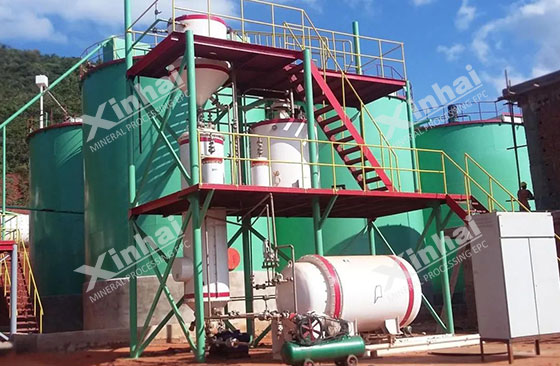
06Gold ore cyanidation process tailings treatment
Since cyanide-containing tailings and wastewater will be produced during the cyanidation leaching process, in order to meet environmental emission standards, chemical oxidation (such as sulfur dioxide-air method), natural decomposition or biodegradation are usually used to decyanate the tailings to ensure that the residual cyanide concentration is lower than the national standard to prevent environmental pollution.
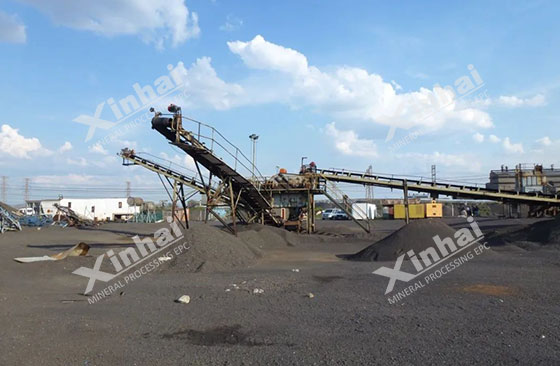
The above is the gold mine all sliming cyanidation process. When designing the full mud cyanidation process, it is recommended to first carry out mineral processing tests so as to optimize the cyanidation leaching conditions through the test results, determine the appropriate process flow, parameter settings and equipment layout according to the characteristics of the ore, so as to achieve ideal results in terms of technical and economic indicators.