In the mineral flotation process, there are many influencing factors. In addition to the process itself, there are also many other external factors. Among them, grinding fineness is one of the important factors affecting mineral flotation. Grinding fineness refers to the mineral particle size. Flotation requires the separation of mineral monomers, and the minerals need to be ground to a suitable particle size. If the mineral particles are too coarse, even if the minerals have been dissociated individually, the floating capacity of the bubbles cannot float the mineral particles for sorting. If the ore particles are too fine, it will also affect the flotation effect. The following will introduce you to the effects of coarse particle flotation and fine particle flotation and their solutions.
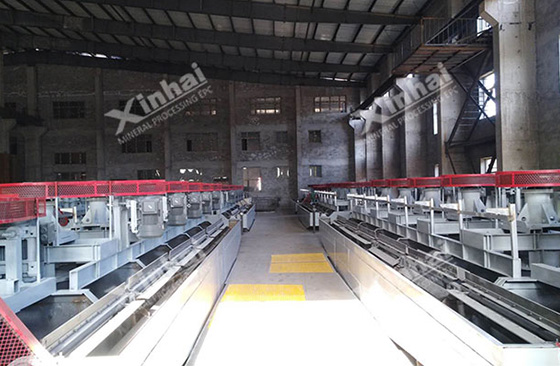
(flotation process)
Use the table of contents below to navigate through the guide:
01Flotation of grinding coarse particles
After the mineral monomers are dissociated, the flotation of coarse-grained minerals can save grinding costs and reduce mineral processing costs. When beneficiating unevenly distributed ores and large-scale porphyry copper ores, flotation is carried out after coarse grinding. Because coarse-grained minerals are relatively heavy and difficult to suspend, the probability of collision with bubbles is reduced. Even if it is attached to air bubbles, it will fall off easily. Therefore, coarse-grained minerals are more difficult to float under general mineral processing conditions. When the particle size exceeds the upper limit of floatable particle size, gravity separation can be used to recover coarse-grained useful minerals.
If you want to use flotation to recover coarse minerals, you can use the following methods:
(1) Improvement of the pharmaceutical system: Add a collector with strong collection ability to the slurry and appropriately increase the concentration of the pharmaceutical. The fixation strength of the minerals and bubbles will be enhanced, and the floating speed will be accelerated.
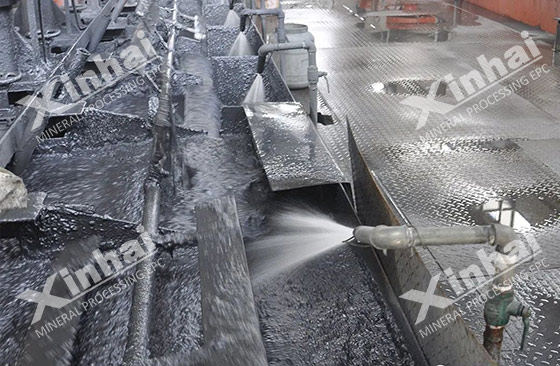
(Slurry during flotation)
(2) Increase the slurry concentration: A relatively thick slurry will be used for flotation of coarse particles. Since the concentration of the overflow slurry from the classifier after coarse grinding is relatively large, the slurry can be directly entered into the flotation machine for processing without adding water to dilute it. When the concentration of the slurry is high, the concentration of the added agent also needs to be increased, and the buoyancy force on the ore particles will also increase. However, the concentration of the slurry should be strictly controlled. If the concentration is too high, the aeration performance of the slurry will be deteriorated and the selectivity in the flotation process will be reduced.
(3) Selection and adjustment of flotation machine: The main reason why the mineral particles in the flotation machine are removed from the bubbles is the movement of the slurry in the mechanical agitation flotation machine. Therefore, reducing the intensity of slurry movement in the tank is an effective way to improve the effect of coarse particle flotation. The main measures to reduce its movement intensity are: ① Select equipment suitable for coarse particle flotation, ② Appropriately reduce the tank depth, shorten the flotation distance of mineralized bubbles, etc. Improve and adjust the structure and operation of conventional flotation machines, ③ Flotation A grid screen is added above the impeller area of the machine to weaken the movement intensity of the slurry and ensure the stability of the foam area. ④ Increase the aeration volume to obtain large bubbles, which is conducive to the floating of coarse particles and the formation of a floating mass composed of bubbles and mineral particles.
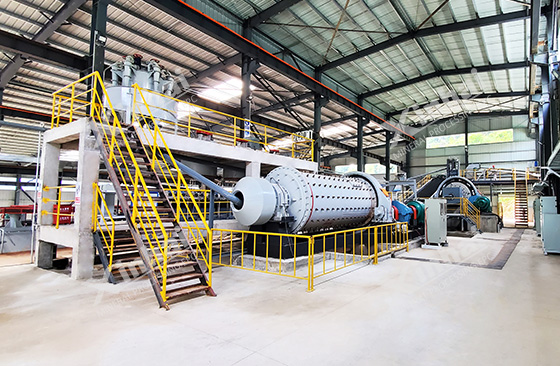
(Grinding process)
02Flotation of grinding fine particles
The fine-grained mineral particles in the flotation process refer to slimes smaller than 18 microns or 10 microns. The sources of these slimes are mainly primary slimes and secondary slimes. The floatability of primary sludge is relatively poor. The characteristics of the slime, such as its small mass, large specific surface area, and unsaturated surface bond forces, will affect the flotation effect. The surface energy of particulate minerals is strong, and mutual cohesion between different minerals is easy to occur under certain conditions, thus forming selective aggregation. The accumulated fine particles will form a mud cover on the surface of the coarse mud, hindering the flotation of coarse particles and reducing the recovery rate of the concentrate. Due to the large specific surface area and surface ratio of particulate minerals, the drug adsorption capacity is enhanced, resulting in poor drug adsorption selectivity and increased drug consumption.
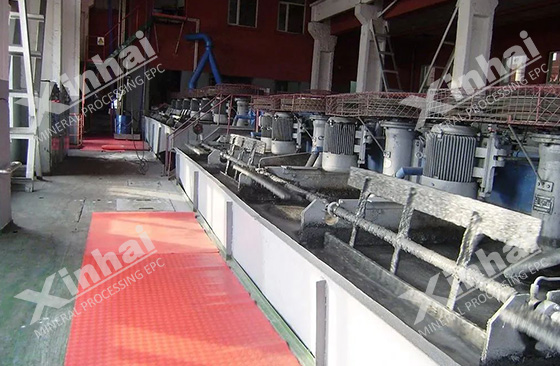
(flotation process)
The presence of a large amount of slime will not only reduce the fine particle flotation speed, but also reduce the concentrate recovery rate and grade. In order to improve this problem, the following measures can be taken:
(1) Eliminate and prevent the impact of slime on the flotation process: adding slime dispersant, dosing in batches, reducing flotation slurry concentration and desliming can all be used to eliminate the impact of slime on flotation. .
(2) Use physical or chemical methods, such as selective flocculation flotation, carrier flotation, and agglomeration flotation, to increase the apparent diameter of particulate minerals and thereby improve the flotation rate and selectivity of minerals.
(3) Add collectors that chemically adsorb or chelate fine minerals into the slurry to improve selectivity during the flotation process.
(4) Under certain conditions, reducing the particle size of bubbles can increase the gas-liquid surface area, and can also increase the probability of collision and adhesion between particles, which is beneficial to the flotation of particulate minerals. There are two optional processes: vacuum flotation and electrolytic flotation.
The above content is the impact of grinding fineness on the flotation process. In order to ensure good flotation results, Xinhai Mining recommends conducting mineral processing test analysis to determine the appropriate grinding fineness and avoid unnecessary grinding cost losses or low concentrate recovery rates.