When ilmenite ore is beneficiated and recycled, sometimes the recovery rate is not high. The important reason is that the grinding and grading process of the iron beneficiation production line and titanium production line is unreasonable, resulting in a large amount of mineral loss. For different ilmenite beneficiation, the requirements for particle size are also different. Let’s take a look at what are the grinding and grading processes for ilmenite ore?
Use the table of contents below to navigate through the guide:
01Ilmenite ore grinding+spiral classifier classifying process
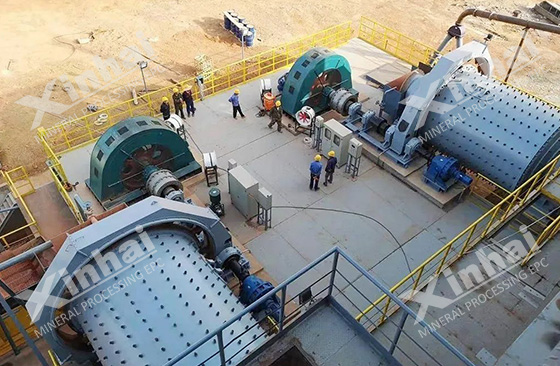
This process uses a ball mill and a spiral classifier to directly form a closed circuit. This process is a simple grinding and classification process. It has the advantages of low investment, low operating cost (no transfer pump, low power consumption for the operation of the spiral classifier), and low maintenance cost. However, the classification efficiency is low, the particle size is uneven, the over-grinding problem is serious, and the overflow and coarsening are also very serious.
02Ilmenite ore grinding+ cyclone classification process
This process has two types: single cyclone classification process and combined cyclone classification process.
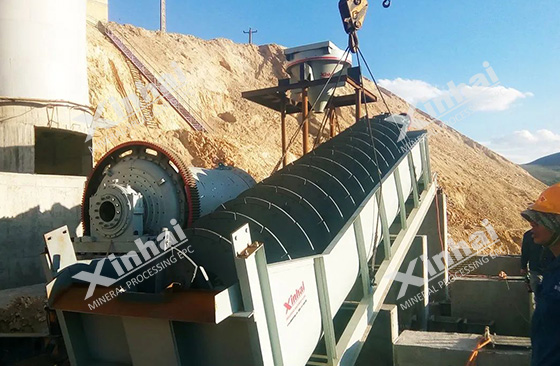
Single cyclone classification process: The cyclone uses a single cone cyclone, and the classification particle size boundary is determined according to the process. Its advantages are simple structure, small footprint, and less investment. However, the classification is relatively rough, and fine particles are included in the sand. , the overflow is more coarse-grained. In order to reduce over-grinding, there are over-coarse minerals in the overflow, and the over-coarse minerals cannot be recovered in the flotation operation.
Combined cyclone classification process: This process uses a ball mill to grind ore. The first stage uses a classification cyclone, using a single cone cyclone. The classification particle size boundary is 0.074mm. The second stage uses a dehydration cyclone and uses a composite cone body cyclone, the classification particle size boundary is 0.20mm. This process has the advantages of simple structure, small floor space, and low investment. However, the overall particle size is relatively fine, the classification is rough, the fine particles in the sand are serious, and the over-grinding phenomenon is serious. In addition, the grinding cost is high.
03Ilmenite ore high-frequency fine screen grinding and classification process
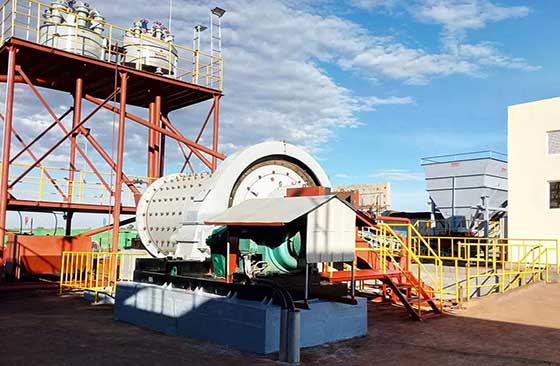
The advantage of the grinding and classification process composed of a high-frequency fine screen and a ball mill is that its overall particle size control is good, which can well meet the particle size requirements of the next process. The process structure is simple, it occupies a small area, and it requires less investment. However, the use of high-frequency fine sieving in this process can easily lead to coarse particle size and poor fluidity of the objects on the sieve. In order to meet the concentration needs of the ball mill, this process is only suitable for situations where the processing volume is small.
04Ilmenite ore cyclone + high-frequency fine screen grinding and classification process
The cyclone + high-frequency fine screen combination and the ball mill form a grinding and classification process, which can effectively reduce over-grinding and have a good effect on subsequent sorting operations. In addition, the high-frequency fine screen only classifies the overflow of the cyclone, reducing investment and floor space. However, the concentration of the material on the high-frequency fine screen is low (50% to 60%), so it can only be used in processes with a small amount of mineral processing. Otherwise, the sand settling of the cyclone + the material on the high-frequency fine screen will cause The mixing concentration is low and cannot meet the concentration requirements of grinding.
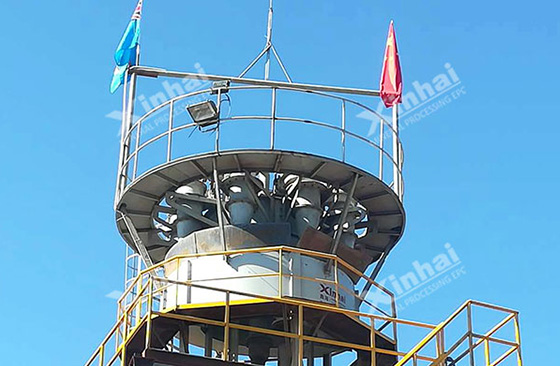
The above is the commonly used grinding and classification process in the ilmenite ore concentrator. In the actual concentrator, how to choose the grinding and classification process depends on the raw material particle size, ore grindability, and the particle size requirements corresponding to this section of the operation. Comprehensive consideration should be given to several aspects of the impact of the selected process, and cannot be generalized.