Gold mines refer to places where gold ore is obtained through mining operations, and gold ore refers to mineral aggregates with a certain gold content that can be used by industry. Gold, from which it is selected, is a rare, precious and stable metal that has always been a symbol of wealth and status. With the depletion of high-grade gold ore reserves, research on medium and low-grade, refractory gold ores and strengthening of traditional gold beneficiation processes have become the mainstream trends in global gold beneficiation. Gold ore has high mining value, and its beneficiation process is relatively complex, and the beneficiation process and equipment are not the same.
The following is an introduction to the gold ore beneficiation process and beneficiation method, and the relevant gold ore beneficiation equipment is attached to the process:
Use the table of contents below to navigate through the guide:
01Gold ore beneficiation process
The gold ore beneficiation process is mainly divided into several stages: crushing and screening - grinding and classification - separating - tailings treatment.
(1) crushing and screening stage
Usually gold ore has low content, fine particle size and complex composition. The commonly used crushing and screening process in the industry is mainly a three-stage closed-circuit process, that is, through coarse crushing, medium crushing, fine crushing and screening to crush minerals to a suitable particle size . The common three-stage-one closed-circuit process is as follows:
Gold ore crushing and screening equipment:
(2) gold ore grinding stage
Rock gold ore grinding operations usually use one-stage or grid-type ball mill + overflow ball mill two-stage grinding. The second stage grinding operation forms a closed loop with a spiral classifier or a hydrocyclone to ensure the grinding fineness. In view of the shortcomings of traditional mills such as fast wear and high energy consumption, Xinhai and other large mining machine manufacturers have carried out a series of transformations on ball mills. Such as adopting new wear-resistant rubber lining plate, changing rolling bearing to sliding bearing, and increasing the size of the mill, etc., while improving the operation rate of the mill, it also prolongs the service life of the equipment, creating economic benefits for the enterprise. Common gold ball mill equipment is shown in the following figure:
Gold ore grinding and classification equipment:
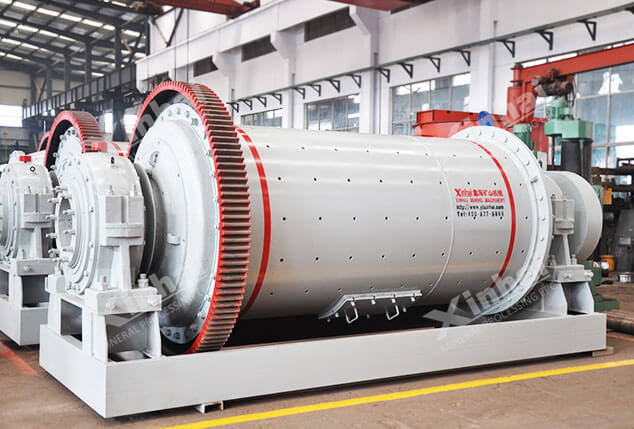
Grid Type Ball Mill
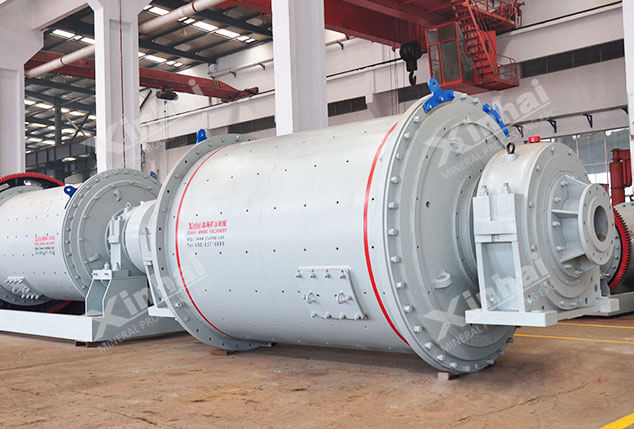
Overflow Type Ball Mill
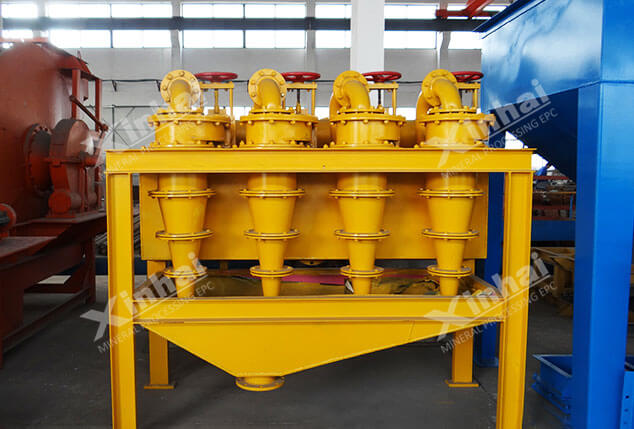
Hydrocyclone
(3) gold ore beneficiation stage
Gold beneficiation stage is divided into two types, one is placer gold beneficiation and the other is rock gold beneficiation. The gold concentrate content of placer gold mine is high, and it mostly exists in the form of sand grains. Therefore, in the separation, the gravity separation process is mostly used. After the pretreatment, desliming and washing, the gravity separation method can directly obtain the coarse gold ore particles. Rock gold ore mainly chooses the appropriate gold selection process according to the composition and composition of the ore. Commonly used gold selection processes are mainly cyanide gold selection process, flotation gold selection process, and gravity gold selection process. For details, see 2. Gold ore beneficiation process.
(4) Gold ore tailing treatment stage
At present, the commonly used tailing treatment methods mainly include tailing re-selection, dewatering ( dry discharge) and filling goaf.
1. Gold tailing re-selection process
The content of useful components in gold tailing is relatively low. However, the use of advanced technology and reasonable process for tailing re-selection can also recover the useful components in the tailing to a large extent, so that the resources can be fully recycled, reduce the output of the final tailing, and relieve the pressure of the tailing on the environment. .
2. Gold tailing dry discharge process
In the gold ore beneficiation stage, the pulp often contains a lot of water. Excessive water content of tailing can easily lead to tailing dam failure accidents. Therefore, in the concentrator, the concentration and dehydration of tailing is also one of the important links, and the tailing dry discharge system is mostly used.
3. Gold tailing fill goaf
Gold tailing fill goaf is to use tailing waste and refill the goaf area after treatment, which can protect the landform and reduce the cost of tailing dam. At present, the main methods of tailing filling goaf are full tailing cement filling technology and high water consolidation full tailing filling technology.
Gold mine tailings treatment process equipment:
02Gold beneficiation method
(1) Cyanide gold selection process
Cyanide gold separation process is one of the main methods for extracting gold from gold ore.
The explanation of the mechanism of cyanide on gold dissolution is currently inconsistent. Most of them think that gold can form a gold complex and dissolve in the presence of oxygen in the cyanide solution. The surface of the gold is gradually dissolved from the surface to the inside in the cyanide solution. The concentration of oxygen in the solution is related to the dissolution rate of gold. The cyanation time varies depending on the nature of the material, the cyanation method and the cyanation conditions. Generally, stirring for cyanidation leaching is usually more than 24 hours, sometimes as long as 40 hours or more, 72 hours for cyanidation gold selection, and more than 5 days for percolation cyanidation leaching.
The method of extracting gold from cyanidation leaching solution: cyanidation gold selection process can be divided into stirring cyanidation and percolation cyanidation. Stirring cyanidation is used for the treatment of re-election, amalgamation of tailings and flotation of gold-bearing concentrates, or for full-slime cyanidation. The percolation cyanidation is used for the treatment of flotation tailing and heap leaching of low-grade gold-bearing ores.
Stirring cyanidation gold extraction process mainly includes two types of gold extraction process flow. One is the so-called cyanide-zinc replacement process (CCD method and CCF method) in which gold is recovered by replacing the precipitation with zinc powder (silk) through continuous countercurrent washing. The other type is the filter-free cyanidation carbon pulp process (CIP and CIL), which uses activated carbon to directly absorb and recover gold from cyanide pulp without filtering and washing.
1. Stirring cyanidation gold selection process
The cyanide-zinc replacement process (CCD and CCF) mainly includes leaching raw material preparation, stirring cyanide leaching, countercurrent washing solid-liquid separation, leaching liquid purification and deoxidation, zinc powder (silk) replacement and pickling, smelting and ingot making and other operations.
Solid-liquid separation (washing): The solid leaching residue is separated from the gold-containing precious liquid. Process: multi-stage countercurrent washing Equipment: thickener, multi-layer thickener, filter press Influencing factors: washing stages 3-5, washing water ratio 4.
Purification: remove the fine suspended solids in the precious liquid (affecting the grade of gold mud). Process: vacuum filtration, pressure filtration. Equipment: plate and frame filter, tube filter. Index: suspended solids<5g/m3.
Deoxidation: Removal of oxygen in the precious liquid (zinc oxide powder, hindering replacement and reducing the grade of gold mud). Process: vacuum deoxidation. Equipment: Deoxygenation tower. Indicator: vacuum degree -0.09~-0.096MPa. The oxygen content of the precious liquid is less than -0.5mg/L.
Add zinc powder: add zinc powder to the precious liquid, and add lead nitrate at the same time. Equipment: Zinc powder disc feeder. Zinc powder parameters: particle size -325 mesh (45um), pure zinc content > 94%. Dosage: Zinc powder: 15-70g/m3. Lead nitrate: 10% of zinc powder.
Displacement: Gold displacement and gold mud filtration. Process: filter press. Equipment: plate and frame filter press. Index: lean liquid grade:<0.02g/m3. The gold content of gold mud is 8-15%, and the moisture content of gold mud is 30-40%.
Scope of application: Ag:Au>5:1 in ore, easy solid-liquid separation, often used for cyanidation of flotation concentrates.
2. Carbon pulp gold selection process
The carbon slurry gold separation process (CIP and CIL) is to put activated carbon into the cyanide pulp, adsorb the dissolved gold on the activated carbon, and then extract the gold from the activated carbon, which mainly includes the preparation of leaching raw materials, stirring leaching and countercurrent carbon adsorption. , Gold-loaded carbon desorption, electrowinning, smelting ingot making, carbon regeneration and other operations.
Carbon pulp separation (CIP): leaching by cyanidation first, and then adding activated carbon to adsorb gold in the pulp.
Carbon leaching of gold (CIL): activated carbon is added to the leaching tank, leaching and adsorption are carried out at the same time, that is, leaching and absorption.
In the CIP process, leaching and adsorption are two separate operations. In the adsorption operation, the leaching process has been basically completed, and the size, number and operating conditions of the adsorption tanks are determined by the adsorption parameters. In the CIL process, leaching and adsorption operations are performed simultaneously. Generally speaking, the leaching operation takes longer than the adsorption operation. The tank size, aeration and dosing are therefore determined by the leaching parameters. Since the adsorption speed is a function of the dissolved gold concentration in the solution, in order to increase the dissolved gold concentration in the front adsorption tank and at the same time increase the leaching time, usually 1-2 stages of pre-dipping are added before soaking and sucking.
3. Percolation cyanide gold selection process
The percolation cyanidation method is also one of the cyanidation leaching processes, which is based on the penetration of the cyanide solution through the ore layer to leaches the gold in the gold-bearing ore, and is suitable for placer and loose porous materials.
The percolation cyanidation leaching method has two processes: pool leaching and heap leaching. The cyanide leachate is percolated and then treated with activated carbon adsorption or zinc powder (silk) replacement treatment.
Pool leaching gold selection process
The percolation leaching is generally carried out in the percolation leaching tank, and the leaching tank usually adopts a wooden tank, an iron tank tank or a cement tank. The bottom of the pool is horizontal or slightly inclined and is round, rectangular or square. The pool is equipped with a false bottom made of acid-resistant board with holes, the false bottom is covered with filter cloth, and the filter cloth is covered with a grid with wooden strips or corrosion-resistant metal strips. During leaching, the ore is placed in the pool, the leaching agent is added above the pool, and the leaching liquid flows out from the lower part of the false bottom. The false bottom is used to filter and support the ore.
The time required for leaching in the percolation tank is not only determined by the dissolution rate of the solvent to the minerals, but also closely related to the penetration rate of the solvent in the material layer. The penetration rate mainly depends on factors such as the height of the material, the porosity of the material, the degree of sludge content, the viscosity of the leaching agent, and the characteristics of the material itself.
Heap leaching gold selection process
Heap leaching is mainly to transfer the mined ore to the prepared yard for stacking, or directly on the stockpiled waste rock or low-grade ore, spray or infiltrate with cyanide leaching solution to make the solution pass through the ore. Percolation leaching. The leachate is circulated for many times, and the ore heap is sprayed repeatedly, then the leachate is collected, and then adsorbed by activated carbon or replaced with zinc, and the lean liquid is returned to the heap leaching operation for recycling.
The heap leaching site generally chooses a gentle slope mountain (natural slope 5-15˚) close to the stope and convenient for transportation. Weeds and floating soil are removed first, then compacted, and a foundation with a slope of about 5° is built, with two sides high and the middle slightly low, so that the leachate can be concentrated into the liquid storage tank. A geomembrane is placed on the yard to prevent leakage. A 0.4-meter soil ridge is built around the yard and a water-proof ditch is built to prevent rainwater from flowing into the yard. A large piece of lean ore 0.3 meters thick is piled up before the ore is piled up.
Advantages: Heap leaching cyanidation method has low production cost and can be put into operation quickly. The scale of heap leaching can be large or small, and each pile of ore can reach tens of thousands of tons. The ore is crushed to a certain particle size and then heap leached or pelletized heap leaching.
4. Resin pulp gold beneficiation process
Using ion exchange resin to adsorb gold from pulp, RIP is mostly used now, and RIL is immature. Use anion exchange resins.
Compared with the carbon slurry method, the resin method has the advantages of large adsorption capacity, good resin wear resistance, no fear of organic pollution, loose desorption conditions, and simple regeneration. The disadvantage is the poor adsorption selectivity.
Scope of application: applicable to both raw ores and concentrates.
Gold mine cyanidation equipment:
(2) Gold flotation process
Flotation method is a kind of beneficiation method widely used to treat rock gold ore in gold concentrator, and it is often used to treat gold-bearing ores of sulfide minerals with high floatability. The flotation process can maximize gold enrichment into sulfide minerals, tailings can be directly discarded, and the beneficiation cost is low. The flotation process mainly includes several stages such as dosing, stirring, aeration, and scraping.
For the flotation of gold ore containing a single gold mineral, with a relatively uniform particle size distribution and relatively coarse particle size, a one-stage grinding and flotation process is usually used.
For gold ore with uneven distribution of coarse and fine particles, usually, mercury plates or gravity separation equipment are placed in the grinding and classification circuit before flotation to recover the gold particles in advance. The above two processes are mostly used in gold beneficiation plants.
For gold mines with complex ore properties, the flotation process is also more complicated. For example, the stage grinding stage sorting process and the mud sand sorting process are all applied in practice.
For the flotation of gold-bearing polymetallic ores, the process is complex and diverse. Gold is usually enriched in a certain mineral concentrate, and gold is sold as an associated mineral.
Scope of application: The flotation gold separation process is suitable for the treatment of gold-bearing sulfide ores with fine gold particles and good floatability. During flotation, sulfide ore is enriched into sulfide concentrate as a carrier for gold. Flotation can also be used to process polymetallic gold-bearing sulfide ores and carbonaceous ores.
In addition, for "insoluble ores" that cannot be directly treated by amalgamation or cyanidation, a combined process including flotation is also required.
Gold ore flotation equipment:
(3) Re-election gold selection process
Gravity separation is one of the commonly used methods for gold ore beneficiation. It mainly uses different specific gravity of materials and different settling speeds in the medium to carry out stratified separation. In placer gold deposits, gold mostly exists in the form of single natural gold, and the density difference between it and gangue is large. The gravity separation method is effective and economical.
There are many kinds of re-selection methods, such as jig re-selection, shaker re-selection, chute re-selection, screw re-selection, centrifugal re-selection and wind re-selection. exist
In gold beneficiation, the common gravity separation gold separation methods mainly include three methods: jig gold separation, shaking table gold separation and chute gold separation.
1. Jigging process for gold selection
Jigging equipment is mainly jig. The jigging process is to mix mineral particles of different specific gravity, and stratify according to specific gravity in a vertically moving variable-speed medium flow. Minerals with small specific gravity are located in the upper layer and minerals with large specific gravity are located in the lower layer. The layered materials are discharged separately.
Scope of application: Jig gold separation is suitable for sorting coarse mineral particles (mineral raw materials of any size except fine materials). For metal mineral beneficiation, the upper limit of particle size is 50mm and the lower limit is 0.2-0.007mm. For placer gold beneficiation, the lower limit of particle size can reach 0.04mm under the premise that the specific gravity difference is greater than or equal to 1.25 and the ore monomer is dissociated.
Advantages: The process operation is simple, the equipment processing capacity is large, and the final product can be obtained in one selection.
2. Shaker gold selection process
Shaker is the main equipment for gold selection. It is a selection equipment in the horizontal medium flow, using the transmission mechanism to drive the bed surface to do longitudinal reciprocating motion, and to perform rushing and differential motion of the bed surface. During the reciprocating motion, the ore particles are subjected to the layering action perpendicular to the bed surface and the separation action parallel to the bed surface, so that materials of different particle sizes are discharged from different sections of the bed surface to realize separation.
Scope of application: Shaker gold selection is suitable for processing and sorting minerals with fine particle size. According to the particle size of the ore, it can be divided into three types: coarse sand bed, fine sand bed and ore mud bed. Among them, the coarse sand bed is suitable for sorting ore particles with a particle size of less than 0.5 mm, the fine sand bed is suitable for processing ore particles with a material particle size range of 0.5 to 0.074 mm, and the slime bed is suitable for processing ore particles with a material particle size of 0.074 to 0.037 mm. .
Advantages: The ore feeding particle size range of the shaker gold selection is generally between 3 and 0.019mm, and the gold selection is stable and reliable. The distribution of the ore belt is clearly visible, the rich ore is higher than other beneficiation methods, it is easy to manage, and the required ore can be sorted at one time.
3. Chute gold selection process
The main equipment for chute gold selection is spiral chute. It is an equipment that uses inclined water flow for sorting. Under the action of the combined force of water flow, mineral gravity, and friction between the ore particles and the bottom of the tank, the ore particles settle in different areas in the tank according to their specific gravity, and the specific gravity is small. The ore particles are taken away by the water flow, leaving behind the ore particles with a large specific gravity, that is, the separation is completed. The chute is an intermittent operation. When the concentrate at the bottom of the chute is deposited to a moving level, it is necessary to stop feeding the ore, remove the concentrate, and then start the operation.
Scope of application: The spiral chute gold selection method is suitable for processing fine-grained materials with low mud content, and the material particle size range is 0.6~0.03mm.
Advantages: simple structure, large processing capacity and low comprehensive cost.
The above three methods of gravity separation and gold separation are only used for the gold ore (placer gold ore) of monomer dissociation. For vein gold minerals, the gravity separation process is rarely used alone, and it is generally combined with other processes to form a combined process, such as the heavy-float combined gold extraction process, and reuse is used to assist gold extraction. In the grinding and classification circuit, the jig, the spiral chute and the shaking table are used together to recover the easily dissociated coarse gold particles first, so as to create better sorting conditions for the subsequent flotation and cyanidation processes, which can be effectively used in the end. Improve gold ore indicators and total gold recovery.
Gold ore gravity separation equipment recommended:
Jig Machine
Shaking Table
BLL Spiral Chute