Fluorite is an important industrial raw material, widely used in metallurgy, chemical industry and other fields. The global fluorite resources are abundant, meeting the growing market demand. With the advancement of science and technology, fluorite mineral beneficiation technology has also been continuously developed, and new beneficiation technologies and equipment have been continuously introduced to improve beneficiation efficiency and concentrate quality. This article will discuss the fluorite production process and how to improve production efficiency and product quality by optimizing fluorite mineral beneficiation equipment.
Use the table of contents below to navigate through the guide:
01Fluorite mineral production process
1. Crushing process
The crushing operation of fluorite ore can be divided into two stages: primary crushing and fine crushing.
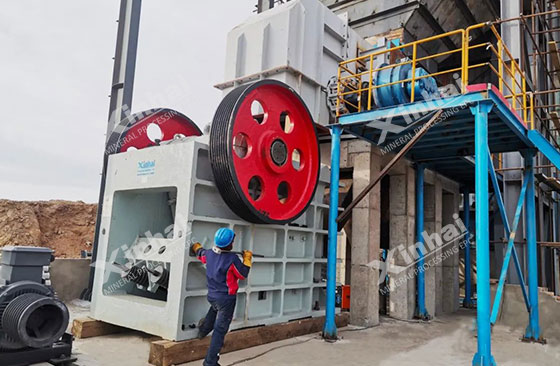
Primary crushing: The primary crushing operation of fluorite ore adopts jaw crusher. Because of its advantages of high efficiency and stability, it is especially suitable for processing harder fluorite mineral, which can effectively reduce the ore particle size and ensure the suitability of the ore in the subsequent processing stage. sex and efficiency.
Fine crushing: When the coarsely crushed fluorspar ore is further crushed, the cone crusher plays a key role. The cone crusher can further refine the ore after primary crushing so that its particle size reaches the selection standard. Choosing efficient and energy-saving fine crushing equipment can significantly improve crushing efficiency and particle size control accuracy.
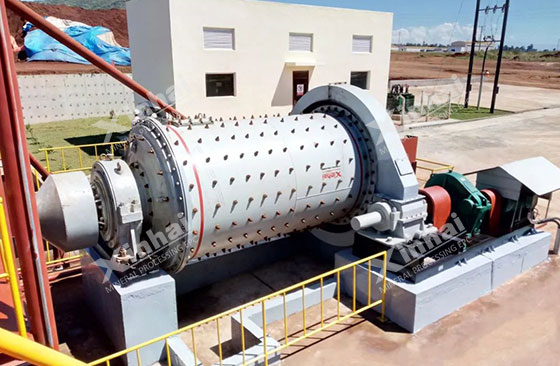
2. Grinding process
In the fluorite mineral beneficiation process, large and efficient ball mills are usually used to grind the fluorite ore. The ball mill refines the ore to a suitable particle size through continuous grinding for subsequent flotation or other beneficiation processes. When selecting a ball mill, its processing capacity and energy efficiency need to be considered to ensure the efficiency and economy of the grinding process. A suitable ball mill can not only improve the grinding efficiency, but also effectively reduce energy consumption, thereby improving the cost-effectiveness of the entire fluorite beneficiation project. Optimizing the operating parameters of the ball mill, such as speed, filling rate and grinding medium size, is also the key to ensuring high-quality fluorite concentrate.
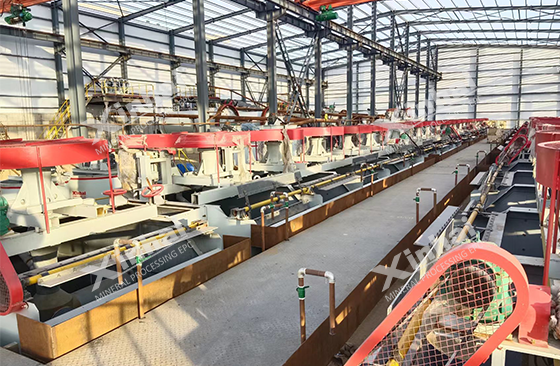
3. Flotation process
In the fluorite mineral beneficiation process, high-quality fluorspar concentrate can be efficiently separated by mixing fluorspar ore with flotation reagents and processing them in a flotation machine. The optimization of the chemical system is crucial. Selecting appropriate collectors, inhibitors and foaming agents, and adjusting their proportions according to the characteristics of the ore can significantly improve the recovery rate of fluorspar and the grade of the concentrate. In addition, the operating parameters of the flotation machine, such as bubble size, stirring speed and flotation time, also need to be precisely controlled. The use of advanced flotation equipment, combined with appropriate parameter adjustment, is the key to improving flotation efficiency and mineral processing indicators, and can ensure the acquisition of high-quality fluorspar concentrate.
02Fluorite mineral processing equipment optimization principles
1. Crushing equipment optimization
- Jaw crusher: Select an efficient and energy-saving jaw crusher to improve crushing efficiency and reduce energy consumption. The equipment should have good wear resistance and reliability to ensure long-term stable operation.
- Fine crusher: According to the characteristics of different ores, select the appropriate type of fine crusher, such as impact crusher or cone crusher, to meet the particle size control requirements.
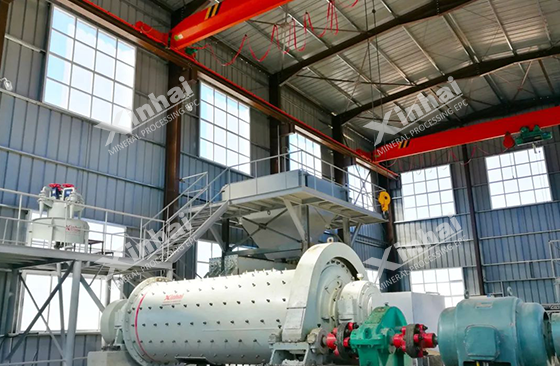
2. Grinding equipment optimization
- Ball mill: Select large and efficient ball mill to improve grinding efficiency and processing capacity. Optimizing the design and operating parameters of the grinding equipment, such as speed, filling rate and grinding medium size, can further improve the grinding effect.
3. Ore dressing equipment optimization
- Flotation machine: Select a flotation machine with advanced technology, such as air flotation flotation machine or mechanical agitation flotation machine, to ensure the efficiency of the flotation process. The selection of flotation machine should be optimized according to the ore characteristics and production scale.
- Reagent system: According to the ore properties and flotation requirements of fluorite mineral, optimize the reagent ratio and addition amount to ensure the best effect of the flotation process.

4. Auxiliary equipment optimization
- Feeder and conveyor: Select efficient and stable feeder and conveyor to ensure the smooth transportation of raw materials and ore. The equipment should have wear-resistant and corrosion-resistant characteristics to adapt to the production environment.
- Pump equipment: Select efficient and reliable pump equipment to ensure the stable transportation of flotation reagents and slurry. The selection of pump equipment should be optimized according to flow and pressure requirements.
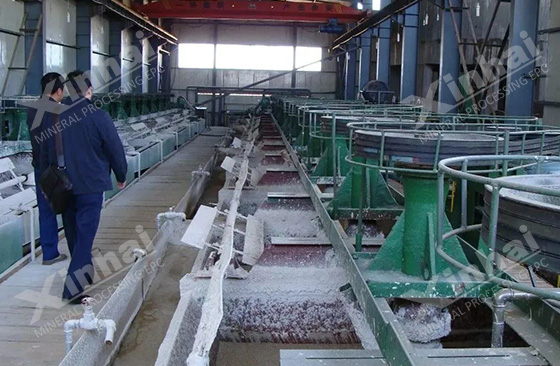
Optimizing fluorite mineral processing equipment is the key to improving production efficiency and product quality. By selecting efficient and energy-saving crushing, grinding and beneficiation equipment, as well as optimizing the configuration of auxiliary equipment, the overall performance of fluorite beneficiation can be significantly improved. With the advancement of science and technology, new equipment and technologies are constantly emerging. Fluorite mineral beneficiation projects should constantly pay attention to the latest developments and implement equipment optimization to meet the market demand for high-quality fluorspar.