Gold mines can be divided into gold-forming ores, gold-bearing ores, gold-containing ores, etc. based on the gold content of the minerals and the composition and structure of the minerals. These gold ore resources are rare precious metal resources. When gold ore beneficiation is carried out, in order to avoid waste of resources, mineral processing technology is very important. There are basically two methods used in gold ore concentrators, the flotation process and the chlorination process. When choosing the appropriate process based on the properties of the gold ore, it is necessary to analyze the properties and specifications of the gold ore. When flotating gold mines, we should not only pay attention to reducing gold mine losses, but also pay attention to protecting the environment. The flash flotation process is a type of flotation technology. Because the flotation time of this process is very short, it is called flash flotation. This method can recover gold resources more economically. The rapid flotation method has been adopted on a large scale, and it can effectively improve the efficiency of mineral processing. This article introduces the principle, function, influencing factors and application of flash flotation process in gold ore beneficiation to help you better understand the flash flotation process.
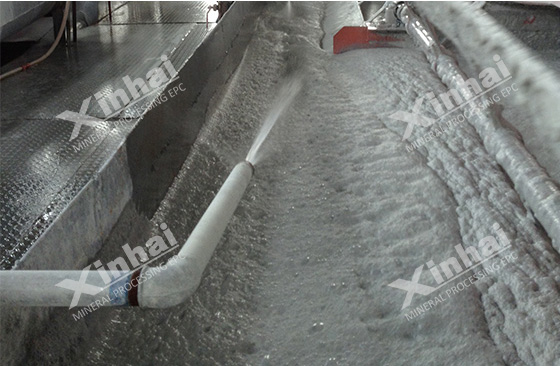
Use the table of contents below to navigate through the guide:
01What is the principle of flash flotation process?
Since the mineral surface is hydrophobic and can aggregate in liquids and gases, the target mineral gold ore will be tightly combined with the bubbles and float to the surface of the liquid to be recycled as a foam product. During the flash flotation process, chemicals need to be added to improve efficiency. There are many types of chemicals to choose from, such as collectors, regulators, and foaming agents. The specific types of chemicals should be combined with the properties of the gold mine, and specific problems should be analyzed in detail, and the order, location and dosage of the chemicals should be adjusted according to the process.
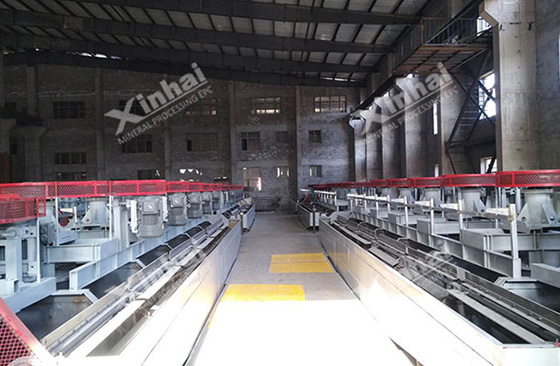
The flotation operation cannot be carried out without flotation equipment. The structure of the flotation machine is multiple grooves connected in series. During flotation, the slurry needs to be fully stirred and aerated, and flotation reagents are added to combine the target mineral particles with bubbles. The bubbles are forced to float. A foam layer is created on the surface of the slurry, and the foam layer is scraped out to collect the gold ore particles.
During flash flotation, because the flotation time is very short, the gangue minerals have no time to float, so the ore and gangue minerals can be effectively separated. In addition, the slurry concentration used in the flash flotation process is very high, and the quality of the selected ore is also very high.
02What are the functions of flash flotation process?
The flash flotation process has two main functions: reducing the waste of gold mine resources and grading gold mines.
1. Reduce the waste of gold ore resources: The flash flotation process will classify the returned sand in a graded manner, recover gold minerals as early as possible, avoid the problem of over-crushing, and thereby reduce the loss of gold ore particles in the sediment. The flash flotation process can also make the gold ore particles more concentrated and speed up the floating speed.
2. Grading gold mines: Flash flotation machines can screen poor quality and low-grade gold mines, thereby ensuring stable quality of the final gold mines and improving the quality of the concentrates.
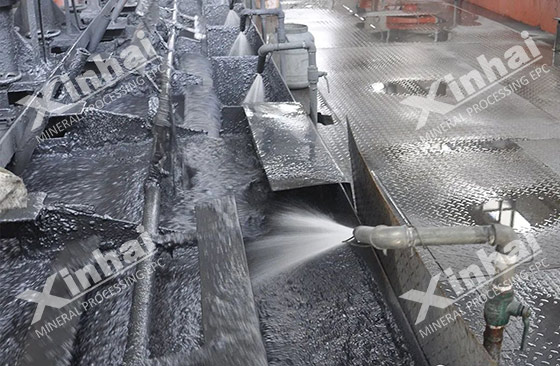
03What factors can affect the flash flotation process?
In the practical application of flash flotation process, there are many influencing factors, such as the properties of raw ore, flotation slurry concentration, ore particle size, bubble size, type and amount of reagents, slurry temperature, etc.
1. Ore properties: Flotation process has a great relationship with ore properties. When the useful elements in gold mines become smaller, the flotation process will become relatively simple and the flotation process will be smooth. If the raw ore elements are too large, the flotation process will not be easy to control.
2. Slurry concentration: The slurry concentration is closely related to the best, and the change in slurry concentration determines the number of bubbles. When the gold ore particles are fine, the slurry concentration requirement is low; when the gold ore particles are coarse, the slurry concentration requirement is high. The concentration of slurry also determines the dosage of chemicals. The higher the concentration of slurry, the greater the dosage of chemicals.
3. Ore particle size: The size of the ore particle is also called the fineness of the ore. The purpose of using flotation technology is to separate gold ore from the mineral, so the fineness of the mineral has a great impact on the flotation process.
4. Mineral processing reagents: Mineral processing reagents can generally be divided into collectors and foaming agents. The more reagents used, the better the flotation effect will be, but this is not absolute. Too much reagents will also cause some harm.
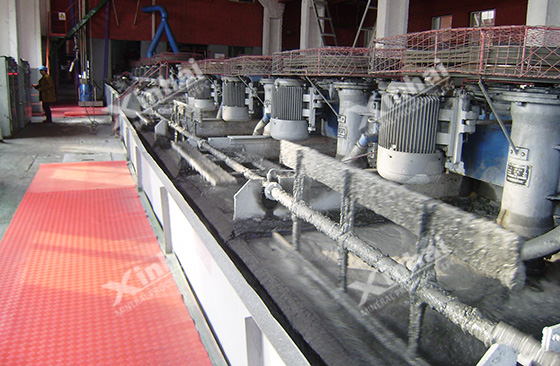
04Why is gold mine suitable for flash flotation process?
Flash flotation is a flotation machine that works together with grinding equipment and classification equipment. The flash flotation machine can screen the minerals in the graded return sand, recover useful minerals, reduce unnecessary grinding processes, and avoid gold ore damage. Wear and surface pollution, improve the utilization of gold mines. The concentration of the flash flotation process is very high. It is a high-concentration flotation process, so it is more suitable for gold mines. Gold mines are high-density ores and are easier to float.
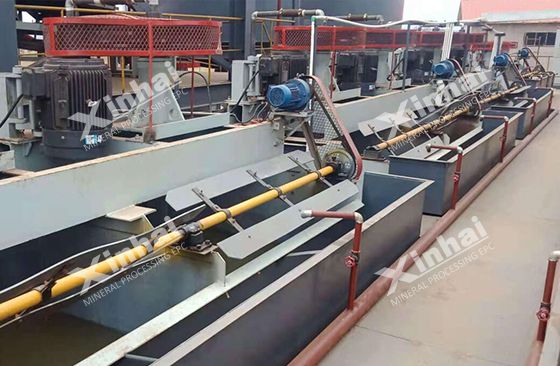
The above is a brief introduction to the application of flash flotation process in the gold ore beneficiation process. Mineral resources are very valuable, gold mines even more so. Therefore, when dealing with the gold ore selection process, it is necessary to conduct a comprehensive study of the ore, analyze the ore properties, select a reasonable mineral processing process, improve the efficiency of the mineral processing work, and reduce resource waste and environmental pollution.