In the face of precious silver ore resources, the goal of concentrator is to improve the recovery of silver concentrate in ore, the following will introduce five ways to improve the recovery of flotation silver concentrate, respectively is: choose the appropriate grinding fineness, develop appropriate process, control pulp pH, choose the appropriate flotation agent and processing equipment.
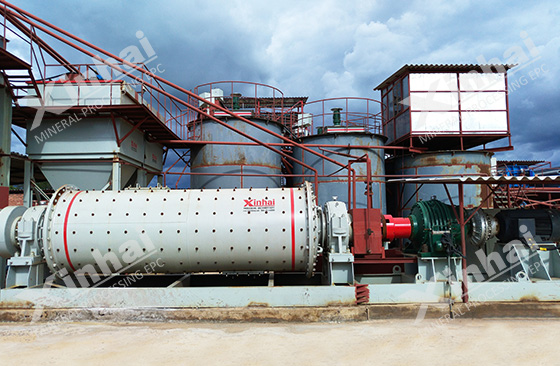
Use the table of contents below to navigate through the guide:
01Select appropriate silver ore grinding fineness
Grinding is a very important link in the process of silver ore. In order to achieve the purpose of various mineral classifying, the raw ore needs to be ground to disassociate various mineral monomer in the ore. Grinding will directly affect the separation effect later, thus affecting the concentrate quality and recovery rate. Most of the silver mineral embedding grain size is fine and small, the occurrence state is complex, the grinding ore fine is too coarse or too fine will affect its sorting results. Therefore, the grinding process requires high requirements, which not only requires the dissociation of silver concentrate and other carrier mineral monomer, but also needs to consider its embedded particle size and occurrence state when grinding. In order to determine these two factors, the concentrator can carry out the mineral processing test composition in advance to clarify the ore composition and physical and chemical properties, so as to determine its suitable grinding grain size.
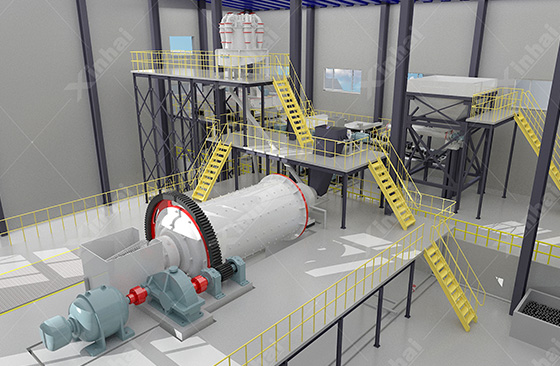
02Design a suitable silver mining process
The main beneficiation process of silver ore includes: flotation, flotation-gravity separation, flotation-cyanide, cyanide, etc.
Among them, the flotation process is one of the main methods to recover silver and other associated metals. In actual production, priority flotation, mixed flotation, partial preferential flotation and partial mixed flotation processes can be selected according to requirements.
For ores with high grade, uneven particle size and easy dissociation, the combined gravity separation-flotation beneficiation process can improve the recovery rate of silver concentrate and reduce production and operation costs.
If the silver ore is unevenly distributed in thickness, the flotation-cyanidation combined beneficiation process can be used to improve the recovery rate of the concentrate, that is, the medium and fine-grained silver ore and its sulfide carrier are first floated out, and the flotation tailings The purpose of regrinding and cyaniding is to recover the dissociated silver minerals inlaid in quartz and other gangues.
If the sulfide content in the raw ore is low, the silver minerals are micro-grained, and the gangue minerals are mainly quartz, the full-slime cyanidation process can be selected.
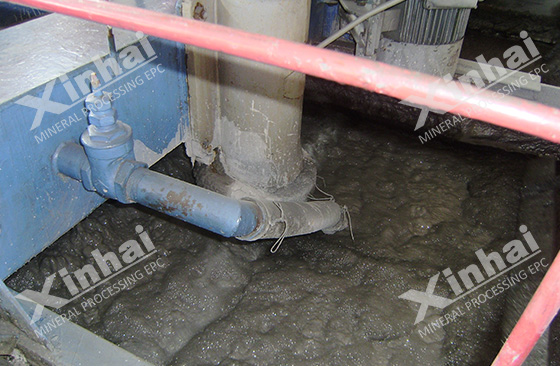
03Control the pH value of silver ore slurry
When the silver ore beneficiation process proceeds to the flotation process, the pH value of the pulp is one of the important factors affecting the flotation effect. During flotation, it is often necessary to add several regulators to the pulp to inhibit certain minerals and achieve effective separation of metal minerals. However, some regulators such as lime and cyanide can inhibit silver minerals, so these regulators should be avoided as much as possible during silver ore flotation. After research, the suitable pulp pH value for silver ore flotation is 6-8, so the pH value of the pulp should be controlled to be neutral or weakly alkaline during the beneficiation process.
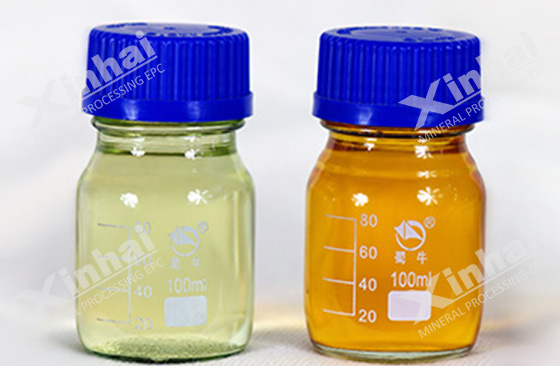
04Select the appropriate silver ore flotation agent
In addition to the process flow, grinding particle size and pulp pH value, beneficiation reagents are also one of the factors that affect the recovery rate of silver ore. Collectors commonly used for silver and silver-loaded gold metal sulfide minerals are: butyl ammonium black drug, aniline black drug, ethyl xanthate, butyl xanthate, ethyl thiocarbamate, etc. Silver minerals have a large specificity, and the stability of the attachment on the air bubbles during flotation is poor and easy to fall off. Therefore, more than two collectors need to be mixed to improve the effect of the agents on silver minerals and carrier minerals. But ylammonium black drug and xanthate combination, aniline black drug and xanthate combination are commonly used collector combinations in mineral processing plants. In addition, adding appropriate regulators and inhibitors to the pulp can create good conditions for collectors to function.
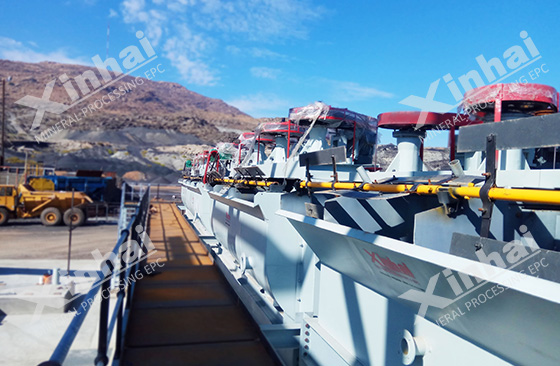
05Use efficient silver ore beneficiation equipment
In actual production, most ore concentrators will adopt new high-efficiency and energy-saving flotation equipment. The performance and quality of flotation equipment can directly affect the beneficiation index of silver ore. Silver minerals have a large specificity and are not firmly attached to the flotation bubbles. Therefore, the agitation intensity and gas filling volume of the flotation machine should be appropriate to facilitate the enrichment of silver mineral concentrates. Adopting a new type of flotation machine is an effective way to improve the recovery rate of silver ore beneficiation. In order to control the flotation process conditions, the concentrator can use an automatic dosing machine, which can automatically adjust and control the amount of dosing.
The above are the five major ways to improve the recovery rate of silver ore flotation beneficiation. There are many other influencing factors in the process of beneficiation of silver ore. Therefore, Xinhai Mining recommends the beneficiation plant to conduct beneficiation test analysis in advance to determine the appropriate beneficiation process plan and indicators, so as to improve resource utilization and return on capital.