In the development of modern mineral resources, the efficient recovery of fine-grained lead-zinc ore has become an important issue in mineral processing technology. As the particle size of lead-zinc ores becomes increasingly refined, it is difficult for traditional flotation processes to effectively recover fine-grained minerals, which forces researchers to explore more advanced mineral processing technologies, such as hydrophobic flocculation flotation, composite activated hydrophobic flocculation flotation and carrier flotation. These technologies can not only improve the recovery rate of lead-zinc ore, but also have significant advantages in chemical consumption and production costs, representing a new direction in the development of lead-zinc ore beneficiation technology.
Use the table of contents below to navigate through the guide:
01Floc flotation of fine-grained lead-zinc ore
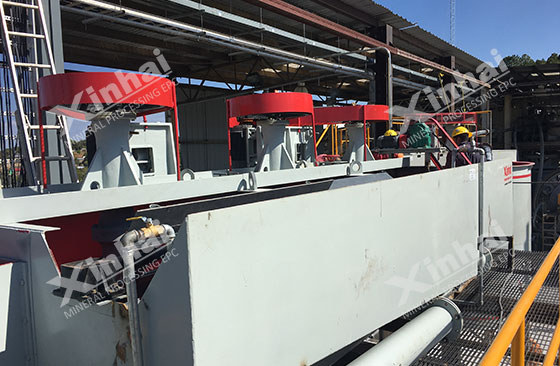
In the floc flotation process of fine-grained lead-zinc ore, hydrophobization is the key factor in the formation of flocs. Collectors, such as butyl xanthate, amyl xanthate and octyl xanthate, can promote the formation of hydrophobic agglomerates of -5μm galena particles, but these agglomerates usually have problems of uneven size and poor stability, especially for overfine particles, the flocculation effect is poor. By adding non-polar oil, the hydrophobic flocculation effect can be enhanced and the agglomeration effect can be improved. The fine-grained gangue minerals and ore mud in the slurry are dispersed with high-efficiency dispersants and pH adjusters, and then the fine-grained lead-zinc ore is selectively hydrophobically agglomerated using xanthate collectors and non-polar oil. Under appropriate mechanical stirring intensity, hydrophobic agglomerates with larger apparent particle size and certain mechanical strength can be formed, thereby enhancing the flotation effect of fine-grained lead-zinc minerals. Floc flotation usually requires the hydrophobization conditions on the surface of the ore particles to be met, and non-polar oil needs to be added to ensure good flotation effect.
02Composite activated hydrophobic floc flotation of lead-zinc ore
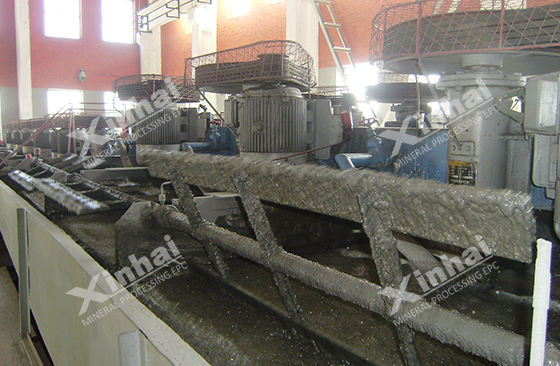
The composite activated hydrophobic floc flotation of lead-zinc ore utilizes the differences in the surface physical, chemical and thermodynamic properties between useful minerals and gangue minerals. By adding ionic inorganic or organic polymers to the pulp, the pulp is kept in a stable dispersed state, and inorganic salts or surfactants are used to eliminate the contamination of soluble salts (such as Ca²⁺, Mg²⁺, Fe³⁺) and ore mud on the mineral surface activity in the pulp, thereby enhancing the selective adsorption capacity of the mineral surface. Next, a mixture of emulsified xanthate and non-polar oil is added to make the lead-zinc mineral selectively hydrophobic to form active hydrophobic clusters. Mechanical activation energy is introduced in a specific slurry tank or high-speed agitator to overcome the potential barrier between particles and further enhance the formation of hydrophobic clusters. Finally, through conventional flotation, these hydrophobic clusters are effectively separated from the dispersed gangue minerals, thereby improving the recovery efficiency of lead-zinc ore.
03Lead-zinc ore carrier flotation
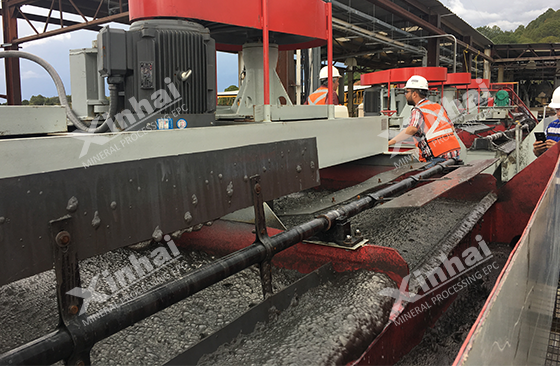
The carrier flotation of lead-zinc ore is based on the conventional flotation process, with coarse-grained materials as carriers and an appropriate amount of collector added to make the fine lead-zinc ore particles and the carrier fully hydrophobic at the same time. Since hydrophobic fine-grained minerals tend to adhere to hydrophobic coarse particles, the fine particles of lead-zinc ore selectively cover the surface of the carrier, or adhere to the coarse ore particles that are easy to float through the principle of hydrophobic aggregation. Then, the bubbles float the carrier together with the attached fine-grained lead-zinc minerals to the surface. The carrier can be the same type of lead-zinc minerals or different types of minerals. By controlling the particle size range and proportion of these carriers, the effective recovery of fine-grained lead-zinc minerals can be achieved without affecting the floatability of the carrier itself, thereby improving the recovery efficiency of lead-zinc ore.
04Development direction of fine-grained lead-zinc ore beneficiation
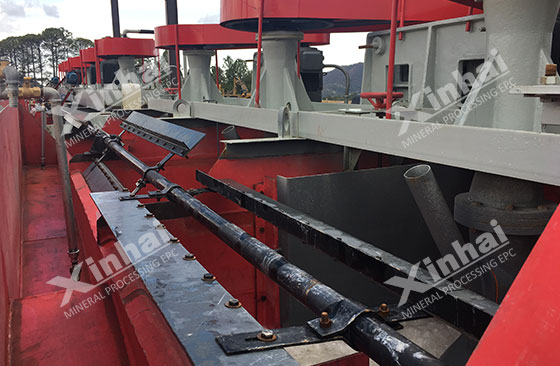
1. Hydrophobic floc flotation and carrier flotation: Due to their low chemical consumption and high metal recovery rate, these two methods show significant advantages in the comprehensive recovery of fine-grained lead-zinc ores and have become important directions for future process development.
2. Low-cost, high-efficiency leaching process: For fine-grained lead-zinc ores that require desliming for efficient separation, when the mud flotation effect alone is not satisfactory, low-cost, high-efficiency, and low-pollution methods should be explored. leaching process to solve the problems of long flotation process, large investment and high operating costs.
3. Research and development of special agents: With the development of cross-disciplines, the development of special agents that can enhance the surface hydrophobization of fine-grained lead and zinc minerals is the focus of future research.
4. Development of large-scale high-efficiency flotation equipment: With the increase in demand for lead and zinc and the decline in ore quality, the development of large-scale flotation equipment for efficient recovery of fine-grained lead-zinc ores will help simplify the mineral processing process and improve lead-zinc resources. Recovery rates are of great significance.
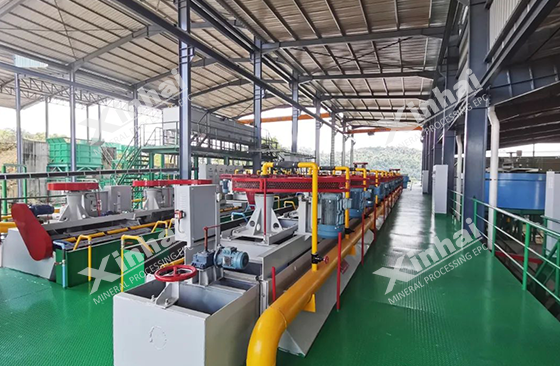
In short, the recovery efficiency of fine-grained lead-zinc ore is directly related to the utilization rate of resources and the economic benefits of mineral processing. By developing new special reagents, optimizing mineral processing processes, and adopting efficient large-scale equipment, the flotation recovery technology of fine-grained lead-zinc ore has been continuously improved. This not only provides technical support for the effective utilization of mineral resources, but also points out the direction for the future mineral processing technology of lead-zinc ore, which has important practical significance and broad development prospects.