Fluorite mineral (also known as fluorspar) is a non-metallic mineral whose main component is calcium fluoride (CaF2). Due to its good transparency, fluorescence characteristics and low melting point, it is widely used in optics, metallurgy, chemical industry and other fields. Since fluorite often coexists with minerals such as quartz and calcite, the ore properties are relatively complex. In order to improve the grade and recovery rate of fluorite ore, a scientific and reasonable mineral processing process is very important. Fluorite mineral beneficiation process usually includes crushing, grinding and classification, flotation separation, concentration and dehydration, and tailings treatment. It aims to obtain high-grade fluorite concentrate through efficient processes to meet the needs of various industrial fields.
Use the table of contents below to navigate through the guide:
01Fluorite mineral crushing and screening
The crushing and screening process of fluorite ore is an important step before beneficiation, which aims to reduce the particle size of the ore, increase the exposed area of the mineral, and facilitate subsequent grinding and grading operations. First, the mined ore is crushed to a particle size of 5-20 cm using a jaw crusher, and then a cone crusher is used for two or three crushings to further reduce the ore particle size to 0.8-2 cm to meet the grinding requirements.
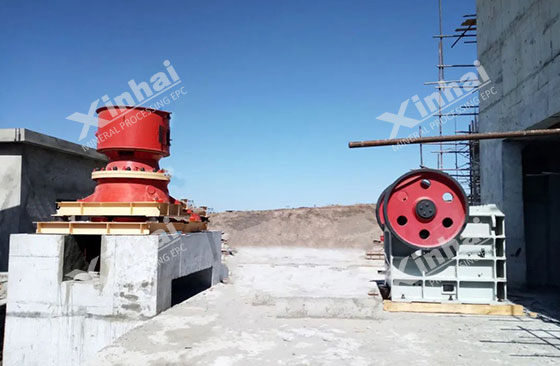
In the screening stage, the equipment selection depends on the mud content and moisture content of the original ore. If the mud content is high (5%-10%) and the moisture content exceeds 5%-8%, it is necessary to add ore washing operations to the process, and it is recommended to use a drum screen for screening to reduce blockage; if the ore has a low mud content and little moisture, a circular vibrating screen can be used for efficient screening.
02Fluorite mineral grinding and classification
Grinding is to further refine the crushed fluorite ore to a particle size suitable for flotation, usually using grinding equipment such as ball mills. In fluorite mineral beneficiation, one or two stages of grinding processes can grind the ore to the required particle size. The one-stage grinding process has a simple structure, less equipment, and low investment. It is suitable for scenes with a particle size requirement of 0.2-0.15 mm (60%-79%-200 mesh) and is often used in small mines. The two-stage grinding process is suitable for scenes with higher fineness requirements (such as 80%-200 mesh), especially for medium and large mines. It can effectively perform coarse and fine grinding to obtain products with uniform particle size and less over-crushing. In the grinding process, in order to ensure that the ore reaches the appropriate fineness and reduce energy consumption, it is necessary to reasonably control the grinding time and grinding medium.
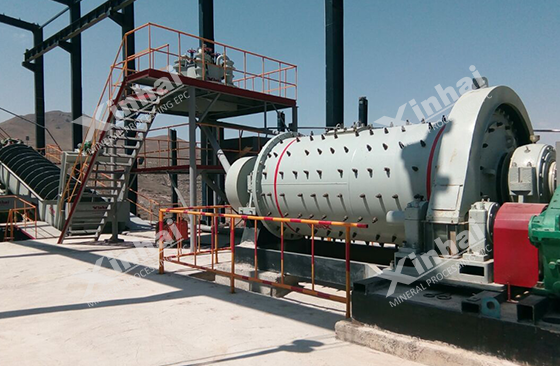
In the classification stage, a spiral classifier or hydrocyclone is used to classify the grinding products. The coarse particles return to the grinding circuit, and the fine particles enter the sorting operation to improve the flotation separation effect.
03Fluorite mineral flotation separation
Fluorite mineral is an easy-floating ore. Its flotation process is based on the difference in floatability between fluorite and gangue. By adding flotation agents, fluorite and associated gangue minerals (such as quartz, calcite, barite and sulfide) are effectively separated. Usually, multiple selection processes are used: roughing is used for preliminary separation, scavenging is used to recover valuable minerals in tailings, and selection is used to further improve the concentrate grade. Generally, at least three selections are performed to ensure that the fluorite concentrate grade reaches more than 97%. Depending on the nature of the ore, the following flotation processes are often used:
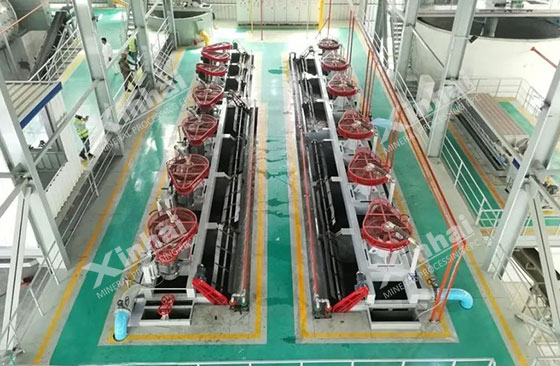
01 Separation of fluorite and calcite
Oleic acid is generally used as a collector to float fluorite, and a small amount of aluminum salt is added to activate fluorite, and dextrin is used to inhibit calcite. For fluorite ores containing complex gangue such as calcite, limestone, and dolomite, tannin extract or lignin sulfonate is more effective. During the flotation process, the pH value of the ore pulp is adjusted and water glass, sodium hexametaphosphate, lignin sulfonate, etc. are used to inhibit calcite. At the same time, oleic acid or fatty acids are used as collectors for fluorite to achieve the separation of fluorite and calcite.
02 Separation of fluorite and quartz
Fatty acids are used as collectors for fluorite, water glass is used as a quartz inhibitor, and sodium carbonate is used to adjust the pulp to pH 8-9. The amount of water glass needs to be controlled. A small amount can activate fluorite, but it does not inhibit quartz enough; excessive amounts will inhibit fluorite. In order to reduce the amount of water glass and enhance the inhibition of quartz, multivalent metal ions (such as Fe³⁺, Al³⁺), including alum or aluminum sulfate, can be added. For quartz-fluorite ores, sodium carbonate is often used to adjust to an alkaline environment to prevent multivalent cations in the water from activating quartz, and an appropriate amount of water glass is added to inhibit silicate gangue.
03 Separation of fluorite and barite
Generally, fluorite and barite are mixed and floated first, and then separated. Oleic acid is used as a collector and water glass is used as a depressant in the mixed flotation stage. When separating mixed concentrates, positive flotation or reverse flotation can be used to obtain fluorite concentrate. Dextrin or tannin combined with iron salts are often used to depress barite, and oleic acid is used to float fluorite; or hydrocarbon sulfate is used to float barite, and the remaining in the flotation tank is the fluorite concentrate.
04 Separation of fluorite mineral and sulfide ore
For fluorite ore containing sulfide ore, xanthate collectors are usually added to float the sulfide ore first, and then fatty acid collectors are used to float the fluorite. In order to improve the quality of the concentrate, a small amount of sulfide mineral inhibitor can be added during the fluorite flotation process to inhibit the residual sulfide ore.
04Fluorite mineral concentration and dehydration
The fluorite concentrate after flotation contains a high amount of water, and usually needs to be dehydrated through concentration and filtration for subsequent processing and transportation. The concentration stage is carried out by a concentrator, which uses gravity sedimentation to separate the solid particles and water in the pulp, so that the solids are deposited at the bottom and the clean water is discharged.
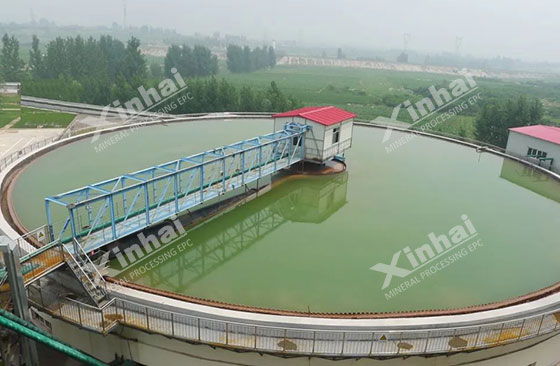
The concentrated concentrate pulp is further dehydrated by filtration. Filtration equipment such as vacuum filters, filter presses and centrifugal filters, etc., use filter cloth or filter paper to intercept solids and discharge water to reduce the moisture content of the concentrate to the required level. Some high-demand concentrates also need to be dried to reduce the moisture content to below 0.5% to meet process requirements such as the production of hydrofluoric acid.
05Fluorite mineral tailings treatment
The treatment of fluorite tailings is an important part of the mineral processing process. Through the steps of tailings concentration, dehydration and stockpiling, as well as resource utilization such as building materials or filling materials, it aims to reduce environmental pollution and improve the comprehensive utilization rate of resources. At the same time, gravity separation, magnetic separation and other methods are used to further recover useful minerals in the tailings to achieve the dual goals of environmental protection and efficiency.
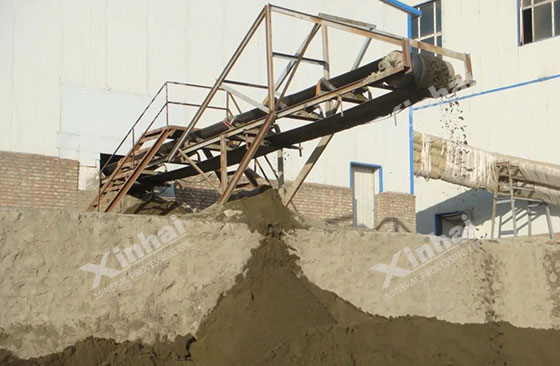
In actual mineral processing plants, there are many types of fluorite mineral and associated minerals. Therefore, although the principle process is similar, the process plan cannot be simply copied, and mineral processing tests need to be carried out before design. Through experimental analysis, the mineral processing process suitable for the characteristics of the ore is determined to obtain an ideal return on investment.