Oxide copper ore is an important component of global copper resources, accounting for a considerable proportion of copper reserves, especially in the upper part of many sulfide copper deposits, forming an independent oxidation zone. These ores have industrial mining value, but with the gradual depletion of easy-to-treat copper resources around the world, the proportion of difficult-to-treat oxidized copper ore resources has gradually increased, and the difficulty of processing has also increased. Therefore, how to develop and effectively utilize these difficult-to-treat oxidized copper ores has become the focus of research in the global mineral processing industry. Next, we will explore in depth the main types of oxidized copper ores, the difficulties in mineral processing, and the latest technological advances.
Use the table of contents below to navigate through the guide:
01Main types and characteristics of oxide copper ore

Oxide copper ore is usually distributed in the upper oxidation zone of the deposit. Affected by complex physical and chemical conditions, its mineral properties are relatively complex. The copper oxide ore in the oxidation zone has the characteristics of diverse mineral composition, fine particle size, and easy mudification, which increases the difficulty of mineral processing. In addition, the floatability of copper oxide ore varies significantly, which directly affects the mineral processing effect. According to different floatability, oxide copper ore can be divided into three types of ores: easy to select, medium to select and difficult to select. Easy-to-separate ores are easier to process through sulfide flotation, while difficult-to-separate ores are often difficult to effectively separate due to their strong surface hydrophilicity and close symbiosis between minerals and gangue, making ore separation more difficult.
02Main oxide copper ore and floatability analysis
There are many types of copper oxide minerals, and the floatability of different minerals varies significantly, which directly affects their mineral processing methods and effects. The following is a detailed analysis of the major copper oxide minerals and their floatability characteristics:
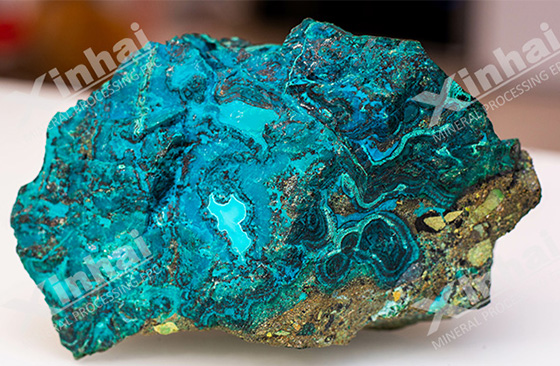
Malachite: Contains 57.5% copper, easy to select, adopts sulfide-xanthate flotation method, ammonium sulfate additive can stabilize the sulfide film and improve flotation effect.
Chrysocolla: Containing 36.2% copper, flotation is difficult and the pH value needs to be strictly controlled. Flotation can be improved by using xanthate flotation after partial sulfurization.
Azurite: Containing 55.3% copper, the flotation performance is better than malachite, but the sulfurization time is longer, and the effect is better after full sulfurization.
Cuprite: Containing 88.8% copper, its floatability is similar to malachite, its properties change greatly, and its sulfide flotation effect is better.
Black copper ore: contains 79.85% copper, is unstable, easily converted into malachite or azurite, and needs to be treated together with its conversion products.
Copper quartz, hydrocobaltite, and chlorantacite: have poor floatability, are easily soluble in water, and are often lost in tailings, increasing reagent consumption.
Pseudomalachite: contains 60.9% copper, and can be directly floated with fatty acid flotation agents, but the sulfide-xanthate method is ineffective.
Through the analysis of the main copper oxide minerals and their floatability differences, it can be seen that different types of copper oxide minerals require differentiated flotation processes and reagent combinations to improve mineral processing efficiency and reduce losses.
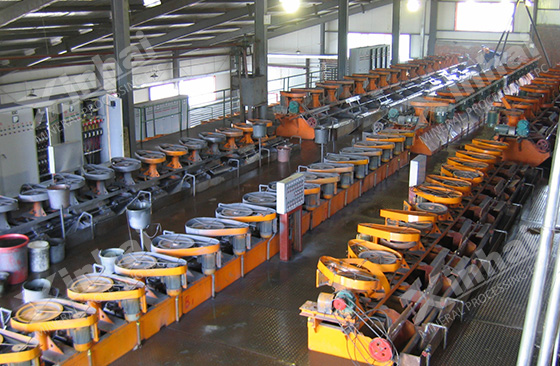
03Difficulties in the dressing of refractory oxide copper ore
Refractory oxide copper ores face many challenges in the dressing process:
1. Complex mineral composition and difficult to separate: Copper minerals and gangue minerals are closely coexisting, and the embedded particle size is fine, which increases the difficulty of mineral dissociation and separation.
2. Strong hydrophilicity of the mineral surface: The surface of oxidized copper minerals is hydrophilic, and flotation reagents are difficult to adhere to, which affects the reagent reaction effect and reduces the recovery rate.
3. High mud content affects equipment and flotation: High mud content is easy to clog equipment, interfere with the flotation process, and lead to insufficient contact between collector and mineral, and reduce the dressing efficiency.
4. Large loss of soluble minerals: Soluble oxidized copper minerals (such as gallstones) are easily soluble in water during flotation, causing losses, increasing reagent consumption, and reducing recovery.
These factors require continuous optimization of the dressing process of refractory oxidized copper ores to improve efficiency and recovery.
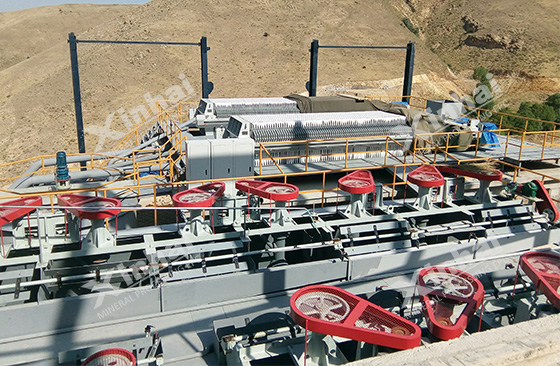
04Refractory oxide copper ore beneficiation process
For refractory copper oxide ores, the following are the current main mineral processing processes and technological developments:
1. Sulfide flotation method: The hydrophobicity of the mineral surface is improved through the sulfide process, thereby enhancing its flotation performance. This method can effectively improve the flotation effect of refractory ores.
2. Application of new collectors: The use of hydroxamic acid and fatty acid collectors can significantly improve the flotation efficiency of copper oxide ores. These new collectors are particularly effective on refractory minerals such as chrysocolla and azurite.
3. New flotation equipment: New equipment such as high-efficiency bubble flotation machines and air flotation columns improve the flotation efficiency of fine-grained minerals and solve the problem of difficulty in processing with traditional equipment.
4. Hydrometallurgical technology: When the flotation effect is not satisfactory, wet leaching technology (such as acid leaching or ammonia leaching) provides an effective way to recover copper, and is especially suitable for processing copper oxide minerals that are difficult to float.
These technological advances provide effective solutions for the development and utilization of refractory copper oxide ores.
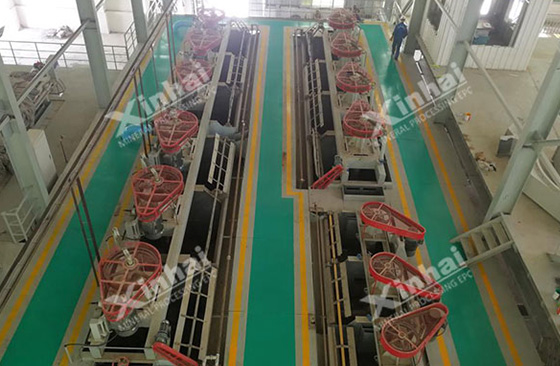
Through a detailed analysis of the main copper oxide minerals and their beneficiation difficulties, we can see that although these ores have significant differences in mineral composition and floatability, advances in modern technology and processes have provided effective solutions to these problems. means. Sulfide flotation, new collectors, advanced flotation equipment and hydrometallurgical technology are all constantly optimizing and improving the beneficiation efficiency and recovery rate of copper oxide ores. In the future, with the continuous innovation and application of technology, the ability to process refractory oxide copper ore will be further improved, contributing to the sustainable development of mining resources.