The type and composition of iron ore are crucial to the determination of the final beneficiation process. According to the different types of iron-containing minerals, iron ores with industrial value can be divided into: magnetite ore, hematite ore, limonite ore, siderite ore and mixed iron ore. Due to the different physical and chemical properties of these iron ores, the efficiency of separation and extraction of iron is also different. Therefore, it is particularly important to apply corresponding beneficiation processes for different types of iron ores, so as to ensure the improvement of iron recovery rate under the premise of economic and environmental protection. In the following, we will discuss the magnetic separation process and its application of various iron ores.
Use the table of contents below to navigate through the guide:
01Magnetic separation of magnetite ore
Magnetite belongs to skarn-type deposits, and the most effective method of beneficiation is magnetic separation. The magnetic separation process can be divided into one or two stages of dry magnetic separation to process medium or fine crushing products in preparation for subsequent concentration. Dry magnetic separation is mainly used to remove coarse tailings and obtain products suitable for concentration. After two or three stages of fine grinding, these products are subjected to two or three stages of wet magnetic separation to finally obtain concentrate. Wet magnetic separation generally uses permanent magnetic cylindrical magnetic separators, one or two stages of magnetic separators choose downstream flow, and three or four stages of magnetic separators choose semi-countercurrent type. The discharge products of the ball mill can be directly subjected to magnetic separation, and both countercurrent and downstream equipment can be used.
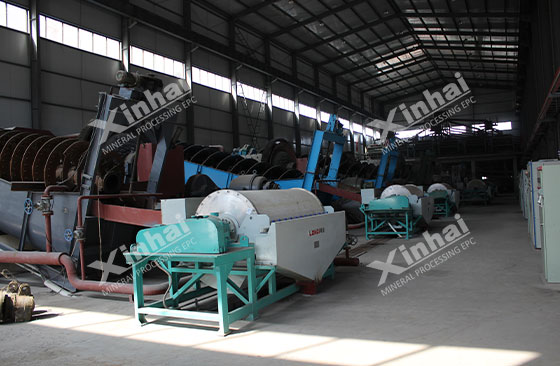
02Magnetic separation of magnetite quartzite ore
Magnetite quartzite belongs to sedimentary metamorphic deposits. At present, magnetic separation is widely used for separation at home and abroad. This type of ore occupies an important position in iron ore resources and is the main object of magnetic separation. The beneficiation process of magnetite quartzite usually adopts stage magnetic separation and stage grinding process. This process can effectively remove the monomer gangue, thereby reducing the subsequent grinding amount. The commonly used magnetic separation equipment is a cylindrical magnetic separator, and its bottom tank is designed as a countercurrent type or semi-countercurrent type to improve the separation efficiency.
03Magnetic roasting and weak magnetic separation of weakly magnetic iron minerals
Minerals such as hematite, limonite, siderite and pyrite have low magnetic properties, and weak magnetic separation methods are difficult to effectively recover these iron minerals. However, they can be converted into strongly magnetic iron minerals by magnetic roasting, and then recovered by weak magnetic separation. Magnetic roasting can be divided into reduction roasting, neutral roasting and oxidation roasting, among which reduction roasting is suitable for treating hematite and limonite. Neutral roasting is used to treat siderite. When siderite is heated to 300-400℃ without air or only a small amount of air, it can be decomposed into magnetite. Oxidation roasting is suitable for treating pyrite. When a large amount of air is introduced, pyrite will be oxidized into pyrrhotite in a short time. If the oxidation time is too long, pyrrhotite will become magnetite.
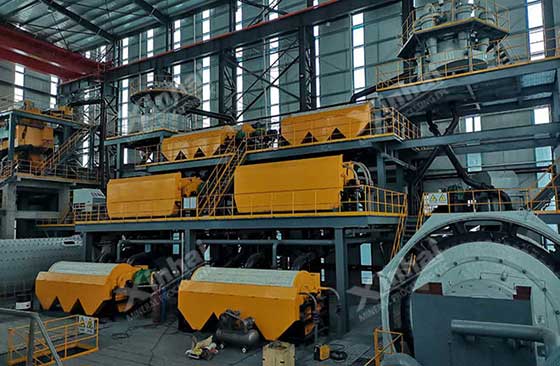
In addition to the three roasting methods mentioned above, there are also redox roasting and reduction-oxidation roasting. The reducing agent in the roasting process can be gas, liquid and solid. Commonly used in industry are coal gas, heavy oil and coal.
04Strong magnetic separation of weakly magnetic iron ores
With the continuous development and successful application of new strong magnetic separators, magnetic separation methods can now be used alone to process weakly magnetic ores, especially iron oxide ores, on a large scale. These strong magnetic separators can effectively separate weakly magnetic minerals and improve the recovery rate and purity of ores. However, in some cases, a single magnetic separation method may not fully meet the separation purposes and requirements, so it is particularly important to combine magnetic separation with other beneficiation methods. For example, combined with flotation or gravity separation processes, the separation process can be optimized according to the characteristics of different minerals, thereby improving the overall economic benefits. Through this combined beneficiation method, the advantages of each method can be fully utilized to achieve more efficient and comprehensive resource recovery.
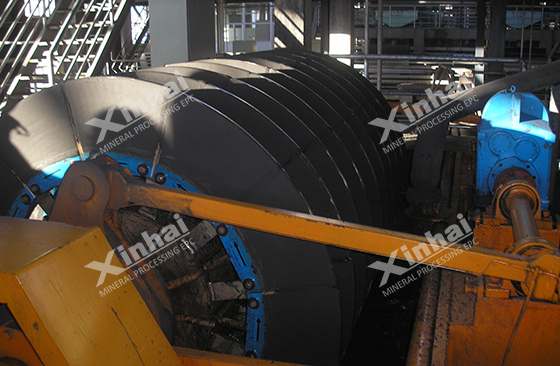
05Magnetic separation of vanadium-titanium magnetite
Vanadium-titanium magnetite ore belongs to the late magmatic segregation deposit, with unique ore particle size distribution characteristics and good magnetic properties, making it an ideal treatment object for magnetic separation process. The particle size of this type of ore is usually moderate and the distribution is clear, which means that valuable minerals can be separated from gangue more effectively during magnetic separation. In addition, the presence of vanadium and titanium not only increases the economic value of the ore, but also makes it show a stronger magnetic response during magnetic separation. In actual operation, the use of advanced magnetic separation equipment can further improve the separation efficiency and maximize the recovery of vanadium and titanium resources.
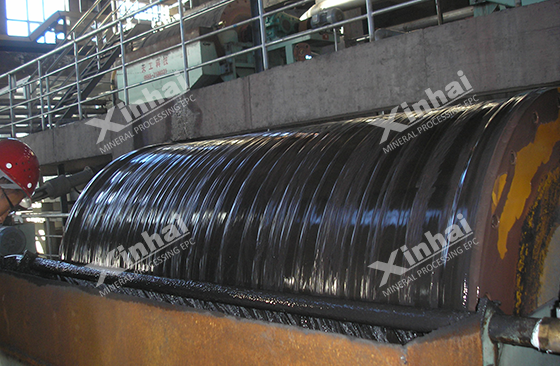
In summary, different types of iron ore have significant differences in beneficiation processes, and choosing the appropriate treatment method is crucial to improving iron recovery and resource utilization efficiency. From the magnetic separation of magnetite ore, the stage grinding of magnetite quartzite, to the magnetization roasting of weakly magnetic iron minerals, to the strong magnetic separation and efficient separation of vanadium-containing titanium magnetite, the rational application of these processes not only improves economic benefits , and also promotes sustainable development.