As an important chemical mineral raw material, phosphate ore is the main source of phosphate and elemental phosphorus. With the continuous exploitation of phosphate resources, high-grade and easy-to-dress phosphate mineral resources are gradually decreasing, and the development and utilization of medium- and low-grade phosphate resources have become an inevitable trend in the phosphorus chemical market. In this context, flotation is one of the most effective methods for phosphate enrichment. Although the price of phosphate has fallen in recent years, the cost of flotation technology remains high. Therefore, reducing the cost of flotation technology and reagents is of great significance to the sustainable development of the phosphate flotation industry. At the same time, selecting the most reasonable and effective beneficiation process for different types of phosphate resources and developing new and efficient phosphate ore flotation collectors are effective ways to improve the utilization rate of phosphate resources.
Use the table of contents below to navigate through the guide:
01Application of flotation method in different types of phosphate ore
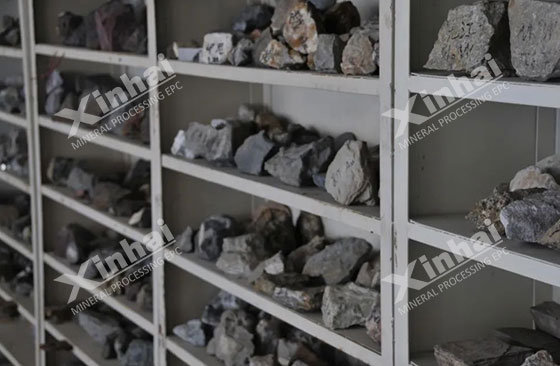
Different types of phosphate ore resources have great differences in the choice of flotation technology, which mainly depends on factors such as the mineral composition, embedded particle size and occurrence state of the ore. The following are several common phosphate rock types and their corresponding flotation methods:
1. Fine-grained phosphate mineral:
Due to the small size of the mineral particles, it is difficult for traditional flotation methods to effectively separate fine-grained phosphate rock. For this type of phosphate rock, microfine flotation technology is an effective method. This technology can significantly improve the recovery rate of fine-grained phosphate rock through ultra-fine grinding and an appropriate combination of chemicals.
2. High-silicon phosphate ore:
Phosphate ore containing a large amount of silicate impurities requires effective desiliconization during flotation. Common methods include reverse flotation, which first floats out silicate minerals and then recovers phosphate minerals. In addition, the selection of appropriate desiliconization agents can improve the desiliconization effect.
3. Phosphate ore containing carbonate impurities:
For phosphate ore containing carbonate impurities, an acid flotation process is often used. By adjusting the pH value of the flotation tank to an acidic environment and using a special collector, phosphate minerals and carbonate minerals can be effectively separated.
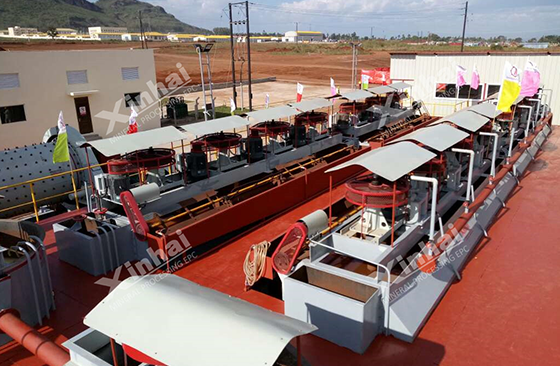
02Selection of collectors for phosphate ore flotation
Flotation collectors are one of the most important reagents in the flotation process, and their selection directly affects the flotation effect and cost. Different types of phosphate ores require different combinations of collectors. The following are several common flotation collectors and their applications:
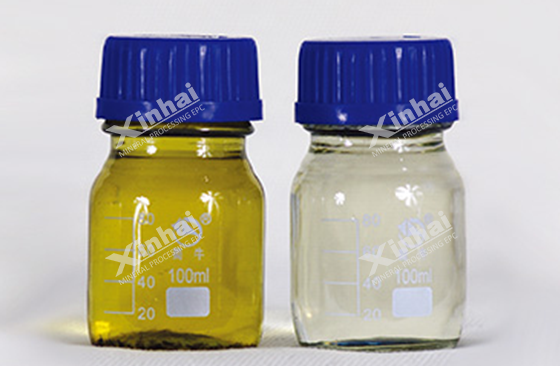
1. Fatty acid collectors:
This is the most commonly used phosphate ore flotation collector with good selectivity and collection capacity. Common fatty acid collectors include oleic acid and stearic acid. This type of collector has a strong affinity for phosphate minerals, but a weak affinity for silicate and carbonate minerals, and is suitable for the flotation of general phosphate ores.
2. Amine Oxide Collectors:
Amine oxide collectors are commonly used in the reverse flotation process of silicon-containing phosphate ore. They can selectively adsorb on the surface of silicate minerals, causing them to float, thereby achieving the separation of phosphate minerals and silicate minerals.
3. Mixed Collectors:
Mixed collectors are a mixture of two or more different types of collectors, designed to combine the advantages of each to improve the flotation effect. For example, the combination of fatty acids and amine collectors can improve the recovery rate and selectivity of phosphate ore.
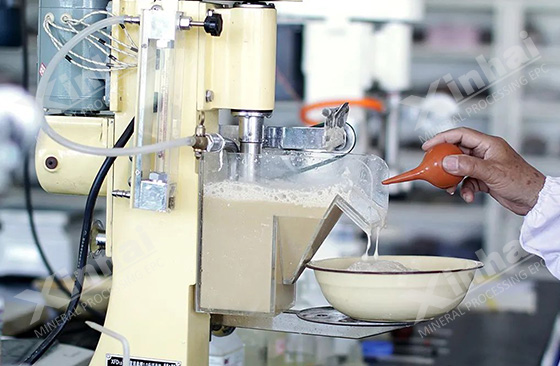
03R&D of new high-efficiency phosphate ore flotation collectors
In order to improve the utilization rate of medium and low-grade phosphate rock resources, it is necessary to develop new and efficient flotation collectors. These new collectors should have the following characteristics:
1. High selectivity: able to effectively separate phosphorus minerals and other impurity minerals in complex mineral systems.
2. High collection capacity: The recovery rate of phosphorus minerals can be significantly improved even at low concentrations.
3. Environmentally friendly: It causes little environmental pollution after use and is easy to handle and degrade.
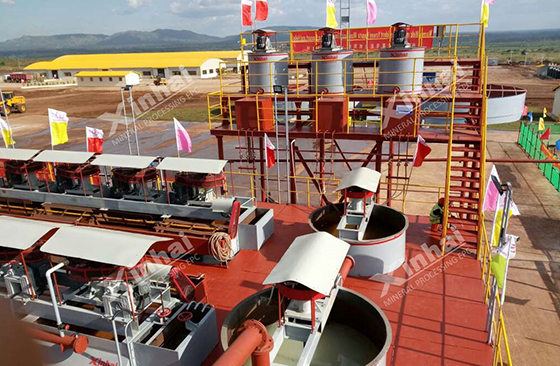
In short, selecting the most reasonable and effective flotation process for different types of phosphate ore resources and developing new and efficient flotation collectors are important ways to improve the utilization rate of phosphate rock resources and achieve sustainable development of the phosphorus chemical industry. . By continuously optimizing flotation process parameters and reducing flotation costs, we can occupy a favorable position in the future development of phosphate mineral resources and ensure the long-term development of the phosphate rock flotation industry.