There are many types of iron ores in nature. The types of iron ores that have been widely developed and utilized mainly include magnetite ore, hematite ore, siderite ore and polymetallic complex iron ore. With the continuous development of mineral processing technology, the mineral processing technology for different types of iron ore has also undergone significant changes, and the mineral processing indicators have also increased accordingly. The following will introduce you to the above-mentioned iron ore beneficiation processes to help you better understand the iron ore separation process.
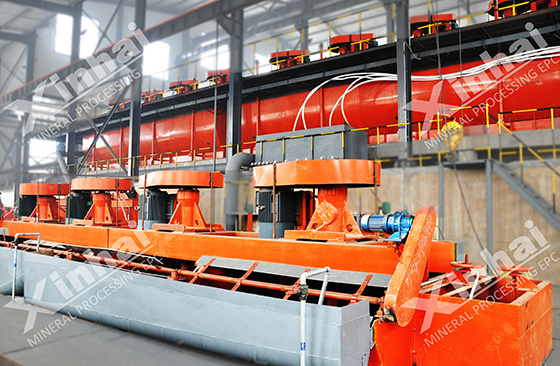
(iron ore flotation separation process)
Use the table of contents below to navigate through the guide:
01Magnetite ore beneficiation process
Magnetite ore processing is mainly based on weak magnetic field magnetic separation. However, with the continuous improvement of the quality requirements for iron concentrate, some adjustments need to be made to the original single weak magnetic field magnetic separation process. Whether it is a single weak magnetic field magnetic separation process or a weak magnetic field + reverse flotation process, both can achieve the purpose of increasing iron and reducing silicon. Adding a reverse flotation process to the weak magnetic field can effectively remove the fine-grained gangue minerals in the weak magnetic separation iron concentrate, reduce the silica content, and improve the quality of the final iron concentrate product.

(iron ore magnetic separation process)
02Hematite ore beneficiation process
The hematite ore beneficiation process currently used in the concentrator is mainly stage grinding - coarse and fine particle separation - gravity separation + weak magnetic separation + high gradient strong magnetic separation - reverse flotation process. This mineral processing technology has the following advantages:
① Using stage grinding, the iron minerals and gangue minerals that have been monomer dissociated can be separated in time under the conditions of coarse grinding particle size in one stage, thereby reducing the amount of secondary grinding.
② The final concentrate contains coarse-grained gravity-separated iron concentrate, which is beneficial to the dehydration treatment of later products.
③ The fine-grained part undergoes strong magnetic separation to remove a large amount of slime and qualified tailings, which can not only improve the grade of iron ore entering flotation, but also reduce the amount of feed for flotation operations, creating good separation conditions for reverse flotation.

(whole iron ore beneficiation processing line)
03Siderite ore beneficiation process
The grade of primary siderite is low, and it often coexists with limonite, hematite, chlorite, garnet and other ores. It also has poor selectivity, so the grade of the iron concentrate obtained by sorting is relatively low. The process adopted for siderite separation is roasting-weak magnetic separation-strong magnetic separation-reverse flotation.
After the raw siderite ore enters the screening machine to sort out powdered ore and lumped ore, the powdered ore undergoes one stage of closed-circuit grinding and fine screening for classification. The products above the screen undergo two stages of grinding and hydraulic classification. The qualified grade is mixed with the products under the screen. A strong magnetic roughing process and a second strong magnetic sweeping process produce part of the final concentrate (strong magnetic concentrate).
The lump ore is screened twice to obtain products with a particle size greater than 75mm and products with a particle size between 15-75mm. These products enter the large and small shaft furnaces for roasting and dry pre-selection before being sent to the main factory. The pre-selected unqualified products will be sent to the main factory after secondary roasting and dry selection to remove the waste rocks. The qualified roasted ore undergoes a stage of closed-circuit grinding, a stage of magnetic dehydration tank, and a stage of magnetic separation, and then the first stage of magnetic separation rough concentrate is classified. The sieved product undergoes a stage of closed-circuit grinding, a stage of magnetic dehydration tank, and a stage of magnetic separation to obtain weak magnetic separation iron concentrate 1 . The product on the screen goes through the second stage of closed-circuit grinding, secondary magnetic dewatering tank, and secondary magnetic separation to obtain weak magnetic separation iron concentrate 2. The two parts of weak magnetic separation iron concentrate are combined and fed into the cation reverse flotation system, and the other part of the final concentrate is produced after further desiliconization.
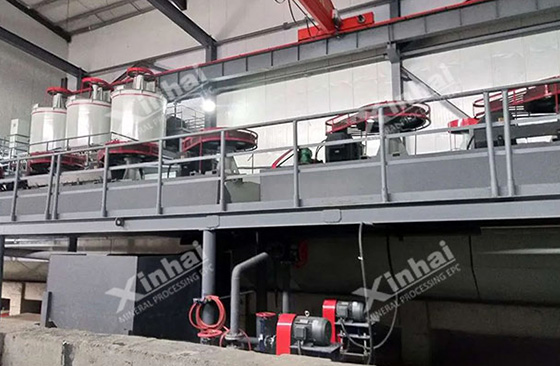
(flotation separation method for iron ore processing)
04Polymetallic iron ore beneficiation process
Polymetallic iron ores mainly include vanadium-titanium magnetite ore, Bayan Obo rare earth-containing iron ore, copper-tin-bismuth magnetite ore, boron-mafic ore, etc.
1. Beneficiation process of vanadium-titanium magnetite ore: In production, the combined magnetic and flotation process is often used to comprehensively recover vanadium-titanium magnetite ore. Magnetic separation is mainly used to recover vanadium-containing magnetite, and then titanium concentrate and sulfur concentrate are obtained through gravity separation, strong magnetic separation, flotation and electric separation. With the gradual rise of rotary hearth furnace direct reduction technology, vanadium-titanium is obtained. Direct reduction of magnetite and comprehensive utilization of vanadium and titanium resources provide feasible ways. The rotary hearth furnace has the characteristic that the charge and the furnace bottom are relatively stationary, which can greatly reduce the degree of expansion and powdering of vanadium titanium magnetite pellets, and can well meet the requirements for the reduction characteristics of vanadium titanium magnetite.
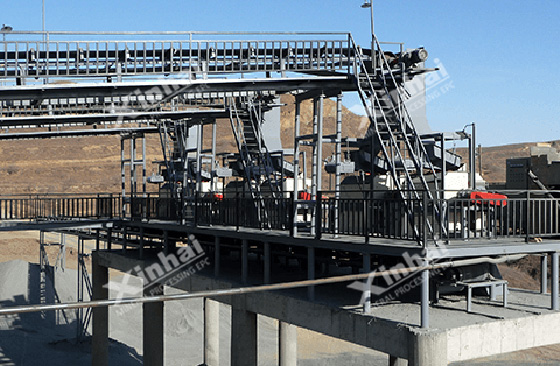
(magnetic separation method of iron ore)
2. Separation process of rare earth-containing iron ore: When processing this kind of ore, weak magnetic separation-strong magnetic separation-flotation process is often used.
3. Beneficiation process of copper-containing magnetite ore: raw ore is continuously ground in two stages. Grind to -0.074mm, accounting for 75%, and then carry out copper-sulfur mixed flotation. The flotation tailings are subjected to three magnetic separations to obtain a final iron concentrate with a grade of 64%~65%. The production capacity of the concentrator is 1.2 x106tpa iron concentrate.
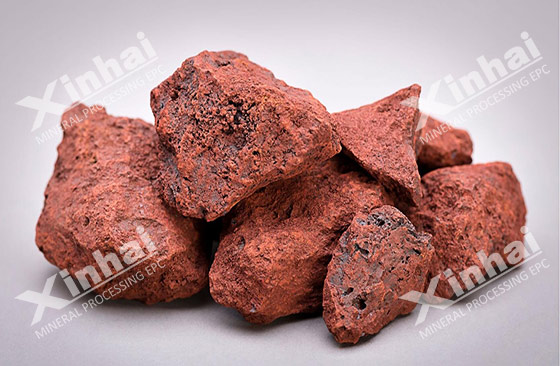
(iron ore)
The above is a brief introduction to several iron ore beneficiation processes. In actual production, the process should be designed and adjusted according to the characteristics of the ore and the production requirements of the beneficiation plant, and the design process and equipment operation should be improved as much as possible, thereby improving the efficiency of the beneficiation plant, concentrate recovery rate and overall economic benefits of mineral processing.