With the advancement of industry and technology, ore beneficiation technology has become increasingly important in the utilization of copper resources. Copper, as an important non-ferrous metal, is widely used in electronics, construction, manufacturing and other fields. Therefore, the mineral processing efficiency and environmental protection of copper ore have become particularly important. Flotation is one of the commonly used methods for copper ore beneficiation. During the mineral processing process, the flotation efficiency of copper ore will be affected by the pH value of the slurry, the type and amount of collectors, and the type and amount of inhibitors. In order to better optimize copper ore flotation process and improving mineral processing efficiency, it is necessary to understand how these factors affect the flotation process. The following will introduce you to the factors affecting copper ore flotation from these aspects.
Use the table of contents below to navigate through the guide:
01Effect of pH value on copper ore beneficiation
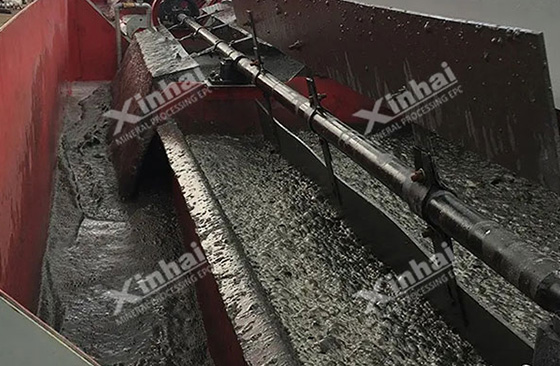
The pH value of the slurry will affect the charge state of the mineral surface, which in turn affects the adsorption of the collector and the stability of the bubbles. Generally speaking, neutral or weakly alkaline slurry is more beneficial to the emergence of copper minerals. Under acidic conditions, oxidation reactions will occur on the surface of copper minerals, which will affect the effect of the agent on the mineral surface and reduce the leaching of copper minerals. Therefore, during the flotation process of copper minerals, the pH value of the slurry should be strictly controlled to ensure that it is within a suitable range to achieve efficient copper ore beneficiation.
02Types of collectors for copper ore beneficiation
The collector is mainly used to change the properties of the ore surface so that it adsorbs with the bubbles to achieve the separation of useful minerals and gangue minerals. Because different collectors have different flotation effects on minerals. Therefore, choosing the appropriate collector can help improve the flotation efficiency of copper minerals. The following are some common types of copper ore collectors:
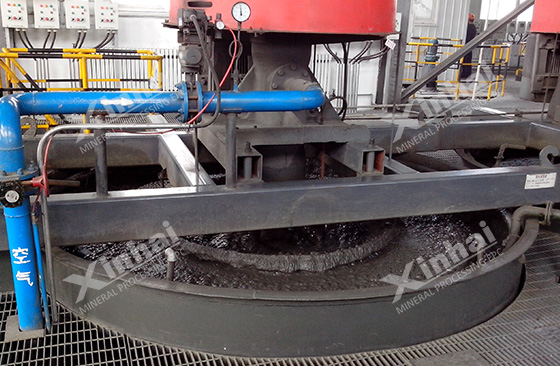
1. Xanthate: It is a natural polymer organic compound that is often used to treat non-copper sulfide minerals, such as copper oxide ore. Its main function is to form complexes on the surface of copper oxide minerals, change the surface properties of minerals, and promote the attachment of copper oxide minerals to flotation foam.
2. Diphenyl diphosphonic acid disulfide: It is an organic collector, often used in the flotation of copper sulfide minerals, such as chalcopyrite. This collector can be adsorbed on the surface of copper sulfide minerals, making the minerals more hydrophilic and conducive to the adhesion of bubbles.
3. Xanthone: Xanthone compounds, such as ethylthionyl diethyl diphosphonate (ETDTP), are the most commonly used collectors of sulfide minerals and are suitable for the flotation of copper sulfide minerals such as chalcopyrite. . They can form hydrophilic sulfide ions in the ore slurry, thereby promoting the attachment of copper sulfide minerals to the foam.
03Effect of collector dosage on copper ore beneficiation
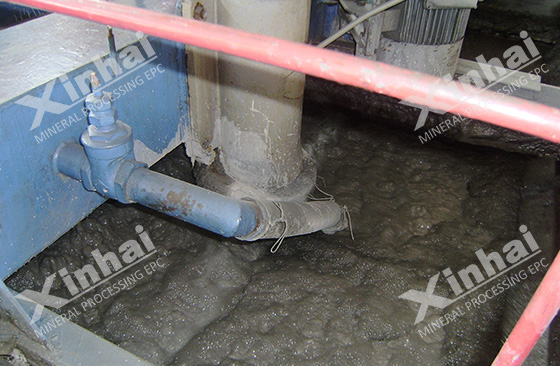
In addition to selecting the appropriate type of collector, the amount of collector should also be strictly controlled. An appropriate amount of collector can promote the generation and stability of bubbles and improve the interaction between ore and bubbles. Excessive collector will not only cause a waste of chemicals, but may also cause bubble instability and reduce mineral processing efficiency. In actual production, mineral processing experiments are usually required to determine the appropriate type of collector and dosage, which can improve flotation efficiency and avoid resource waste.
04Types of inhibitors for copper ore beneficiation
In the copper ore flotation process, in order to inhibit the floating of certain gangue minerals, inhibitors need to be added to improve the flotation efficiency of useful minerals. The type of inhibitor added needs to be based on the characteristics of the inhibited ore. Here are some common inhibitor types:
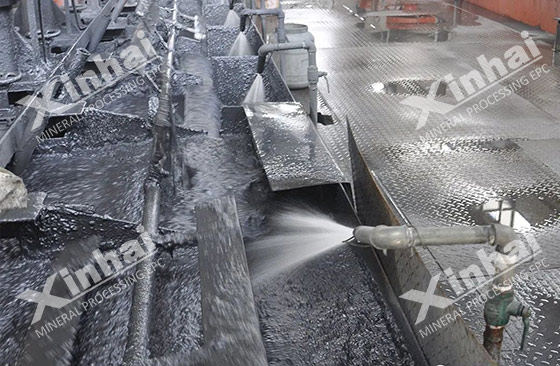
1. Sulfide inhibitor: In the flotation of chalcopyrite, sulfide inhibitors are sometimes needed to inhibit the flotation of sulfide minerals such as pyrite. Such inhibitors react with the surface of sulfide minerals and reduce their flotability, thus increasing the flotation selectivity of copper minerals.
2. Silicate inhibitors: In copper ores, there may be silicate minerals with high iron content, such as iron silicide. These minerals can interfere with the flotation of copper minerals. Silicate inhibitors, such as oxalic acid and phosphates, can be used to inhibit the flotation of these minerals.
3. Oxalic acid and phosphate: Oxalic acid and phosphate are used to inhibit the flotation of some oxidized minerals. These inhibitors can form complexes with the surface of some oxidized minerals, reducing their adhesion to flotation foam.
05Effect of inhibitor dosage on copper ore beneficiation
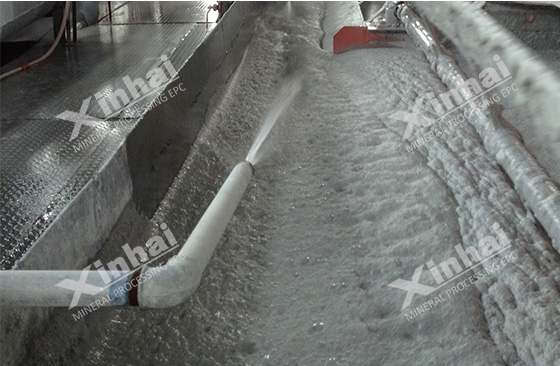
Similar to collectors, the dosage of inhibitors needs to be precisely controlled. A moderate dosage of inhibitor can effectively inhibit non-valuable minerals and improve the flotation efficiency of valuable minerals. However, excessive use of inhibitors may affect the flotation of valuable minerals, thereby reducing the overall separation efficiency. Therefore, in the process of copper mineral beneficiation, rationally adjusting the dosage of inhibitors and finding the balance between inhibition and flotation is of great significance for optimizing the beneficiation process.
In summary, the pH value of the slurry, the type and amount of collector, and the type and amount of inhibitors are the key factors affecting the copper ore beneficiation process. Through in-depth study and precise control of these factors, an efficient and environmentally friendly copper mineral beneficiation process can be achieved. In order to scientifically and reasonably control these factors, Xinhai Mining recommends conducting mineral processing test analysis of ores. The mineral processing plan designed based on the results will improve the quality of the concentrate products and the production efficiency of the processing plant.