Fluorite ore often coexists with minerals such as quartz, calcite, barite and sulfide. Flotation is often used to process fluorite ore at home and abroad, especially for the separation of high-purity fluorite powder. Quartz-type fluorspar ore adopts the process of primary grinding, roughing and tailing, regrinding of coarse concentrate, and multiple selections. However, some problems often occur during the flotation of fluorspar concentrate, such as extremely fine-grained sludge hindering the flotation process, difficulty in flotation of fine-grained minerals, and the treatment of medium ore. Let's take a look at the impact of these problems and how to solve flotation problems to improve fluorite flotation efficiency.
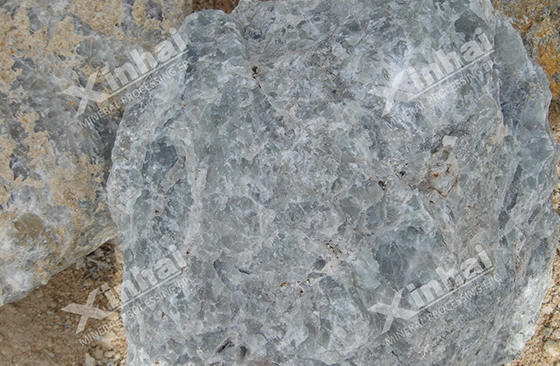
Use the table of contents below to navigate through the guide:
01Effect of extremely fine-grained slime on fluorite flotation
The extremely fine-grained sludge produced during fluorite flotation will affect the flotation efficiency. For example, it is easy to adsorb on the surface of coarse-grained minerals, destroying its selectivity, or it is easy to adsorb more mineral processing agents, thereby reducing the slurry concentration and causing mineral separation. difficulty. In order to avoid the impact of these slimes on flotation, their generation should be prevented or reduced. Commonly used methods are as follows:
1. Reduce and prevent the generation of sludge: adopt a multi-stage grinding + stage beneficiation process, and select correct and efficient grinding and classification equipment to improve grinding and classification efficiency.
2. Eliminate the harmful effects of mineral mud: water glass, soda, caustic soda and other agents can reduce the flocculation cover of mineral mud. At the same time, a segmented dosing method is adopted to reduce the harmful effects of large amounts of adsorbed chemicals by sludge.
3. Carry out desliming process in advance: The ground raw ore is deslimed before flotation and discarded as tailings. When the content of useful components in the slime is high, flotation or hydrometallurgy treatment can be performed after desliming to improve mineral utilization. Commonly used desliming methods include classifier desliming and hydrocyclone desliming.
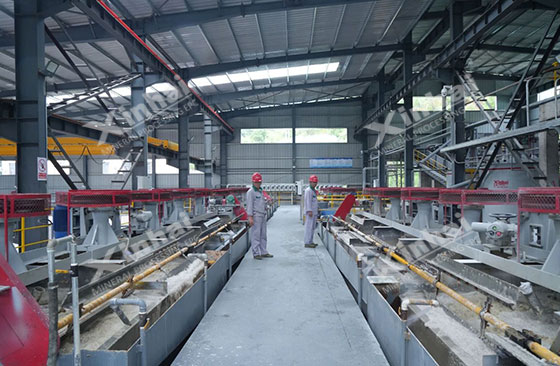
02Reasons for the difficulty in fine-grained fluorite flotation
1. Fine-grained minerals have a large specific surface area, and the surface energy will increase significantly. Non-selective mutual coagulation is prone to occur between mineral surfaces under certain conditions. The surface energy of fine-grained minerals is large, and their selective adsorption properties will become worse, affecting the flotation effect. These reasons will make it difficult to sort fine-grained minerals.
2. The smaller size of fine-grained minerals reduces the possibility of collision between these minerals and bubbles. At the same time, due to the small mass of fine-grained minerals, it is difficult to overcome the resistance between the mineral particles and the bubbles and adhere to the bubbles, making it difficult to float out the fine-grained minerals.
The technological measures to solve the problem of fine particle fluorite flotation are as follows:
1. The purpose of using selective flocculation and flotation technology is to selectively flocculate the target mineral or gangue fine mud, and then separate it by flotation method.
2. The use of carrier flotation can allow mineral particles of general flotation size to be used as carriers, and the fine particles of the target mineral will cover these carrier particles and float up. The carrier can use similar minerals or different minerals. For example, pyrite can be used as a carrier to float fine gold, and calcite can be used as a carrier to float fine iron and titanium impurities in kaolin.
3. Using agglomeration flotation, after the fine-grained minerals are treated with a collector, neutral oil is added to form an oily foam with minerals. The collectible agent and neutral oil can be first formulated into an emulsion and then added to the slurry to optimize the mineral processing process. Neutral oil and collector can also be added to the high-quality slurry respectively, stir vigorously for a period of time and then scrape out the upper foam. The agglomeration flotation method is mainly used for the separation of fine-grained manganese ore, ilmenite and apatite.
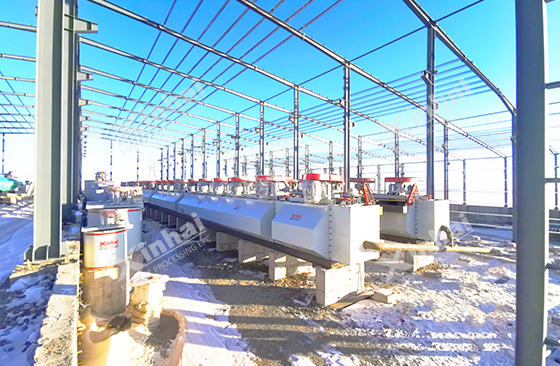
03Choose a reasonable fluorite ore treatment method
The treatment of medium ore in the fluorite flotation process is also very important. During the flotation process, the selected tailings and swept concentrates are collectively referred to as middlings. The conjoint content, the floatability of useful minerals and the requirements for concentrate quality will all affect the choice of mid-mine treatment methods. Medium ore processing plan is as follows:
1. Sequential return of medium ore: The sequential return of medium ore can process medium ore composed of monomer dissociated mineral particles. When mineral floatability is generally required and high recovery rates are required, the medium ore sequential return method can also be used. Adopting this method can reduce the chance of medium ore undergoing re-selection and avoid the loss of useful minerals.
2. Regrinding of medium ore: Medium ore with a large number of contiguous bodies needs to be regrinded. The regrinding process can be carried out separately, or it can be returned to the first stage of grinding. When there are still some monomer dissociated mineral particles in the medium ore, these mineral particles need to be returned to the classification operation for processing first. When the surface of the medium ore needs mechanical scrubbing, it also needs to be returned to the mill for reprocessing.
3. Separate flotation of medium ore: Although the medium ore is not contiguous, the ore has the characteristics of complex dissipation, many difficult-to-float ore particles, and contains a lot of mud. If the flotability is greatly different from that of the original ore. Therefore, it is not feasible to return to the front process. The job is not feasible. In this case, the medium ore needs to be flotated separately.
4. Other treatment methods: When the effect of flotation separation alone is not good, you can choose to use chemical beneficiation methods.
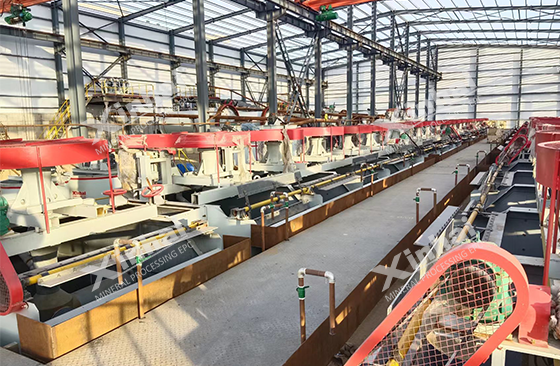
There are many factors that affect fluorite flotation, among which the more important ones are: grinding fineness, slurry concentration, prescription, aeration and stirring, flotation time, and flotation process. In addition, water quality and slurry temperature also have a greater impact on flotation. In order to ensure the normal progress of the flotation process, it is necessary to operate according to the nature of the ore and production requirements, while maintaining the relative stability of the flotation process.