Along with the rapid development of the steel industry in China, and the accelerated exploitation and utilization of the iron mines, subsequently, iron tailings emissions have been increased greatly and large tailings stock. The tailings contain a low amount of iron, but it has great value in re-processing.
According to the statistics, the average grade of iron tailings in China is more than 11%. Due to extensive mining in the past, people prefer to develop rich mines rather than the poor. Calculated only by the average grade of total iron, there are 800 million tons of iron contained in China's iron tailings. That is a very precious wealth. With the increasing shortage of iron mineral resources and the increasing dependence on foreign countries, it is more important to strengthen iron tailings re-processing to recover iron under such circumstances.
Usually, according to different ore properties, different tailings treatment and recovery processes will be used for iron tailings re-processing. In general, iron tailings re-processing mainly includes the process of magnetic separation, gravity separation, flotation and combined separation methods.
Use the table of contents below to navigate through the guide:
01Iron tailings re-processing technology - the magnetic separation
For some iron tailings, iron exists in the magnetite and weakly magnetic hematite and limonite. Gangue minerals are mainly non-magnetic quartz, calcite and so on. The magnetic differences between them determine that the process of magnetic separation can be applied to recover the iron in the tailings.
Because of the fine particle size of iron tailings and few strongly magnetic minerals, the strong magnetism is usually used to collect weakly magnetic minerals in the process of iron tailings re-processing. The process is simple, which generally needs to go through 2-3 stages of magnetic separation. For example, high gradient magnetic separation is applied to pre-enrichment of magnetic minerals, and used in conjunction with the shaking table process or centrifugal separator process of the gravity separation to obtain the iron concentrates, titanium concentrates.
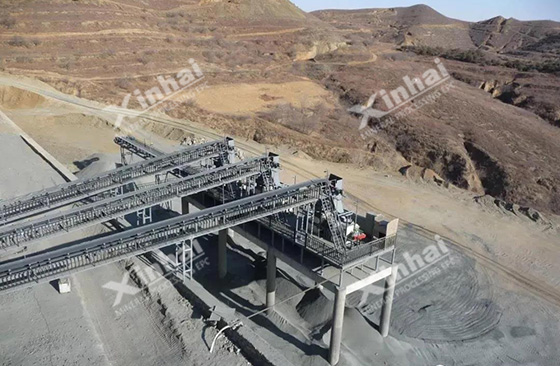
According to the properties of iron tailings, if people directly use magnetic separation, the recovery index will be not good enough. Fine grinding before the magnetic separation can dissociate the iron-containing mineral monomer, thereby the magnetic separation effect can be improved. The process of magnetic separation is simple, convenient, and doesn't produce additional pollution. So it has been widely applied to iron tailings re-processing.
02Iron tailings re-processing technology- the gravity separation
During the processing of gravity separation to recover iron from iron tailings re-processing, spiral chute is usually used for pre-discarding of iron tailings. The concentrate of the chute usually goes into the regrinding system to improve the dissociation degree of the target mineral for subsequent separation. The shaking table is usually applied to the reselection of strong magnetic concentrate to obtain high-grade concentrates. But with its small processing capability, it is generally not used for the separation of iron tailings. While using the shaking table, it is necessary to control the particle size of the selected ore as much as possible in order to achieve the ideal separation effect. When processing fine-grained minerals, the concentrate recovery rate of the shaking table is low. The centrifuge is often used in conjunction with a strong magnetic separator, suitable for the separation of fine-grained minerals, and the recovery rate of concentrate is high, which is suitable for the extraction of grade 35-45 iron inferior concentrate. However, the enrichment ratio will not be too large.
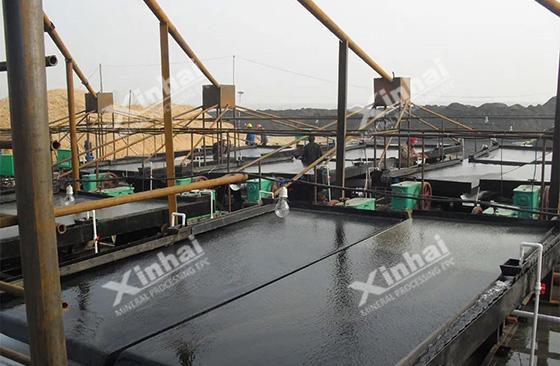
It is noteworthy that grading assignments often play a positive role during the process of gravity separation. Usually, before the gravity separation, it's necessary to finish grading assignments to improve the beneficiation index of iron tailings greatly.
03Iron tailings re-processing technology- the flotation separation
The recovery rate of iron in concentrate is low by the magnetic separation. The main reason is the current magnetic separation equipment is difficult to effectively recover fine or micro-fine magnetic iron-containing minerals. However, the flotation separation can separate the target minerals efficiently by means of chemical agents and mechanical adjustment according to the different surface properties of ores. This beneficiation method is widely used in the separation of fine and micro-fine materials. In recent years, it has been gradually applied to the recovery of iron in iron tailings.
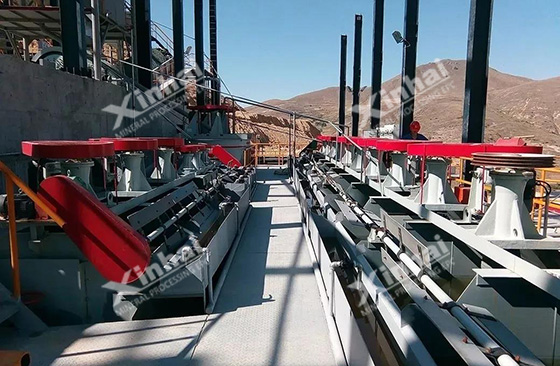
Several flotation separation methods are frequently used in iron tailings, such as anion positive flotation, anion reverse flotation and cation reverse flotation. The main component of anionic collectors is a fatty acid. Frequently-used anionic collectors include RA series and CY collectors. The main component of cationic collectors is the dodecylamine and other amines collectors, and GE series cationic collectors.
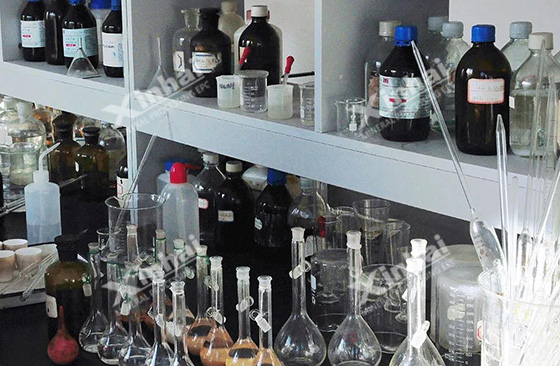
The anion positive flotation is applicable to the simple ore composed of iron oxide minerals. However, the mineral composition is complex and a large amount of mud exists in the iron tailings so that there will be a poor flotation index. The anion reverse flotation is to use activators (calcium ions) and other activated fatty acid collectors to separate the quartz gangue minerals completely. Meanwhile, iron-containing minerals in the iron tailings enter into the foam together, which reduces the recovery rate. But when using the cation reverse flotation, the iron-containing silicate and quartz enter into the foam together, which can get a high concentrate grade. The cation reverse flotation is suitable for the flotation separation of iron-containing ore with a more complex composition, but requires a high grade of minerals. Therefore, it's necessary to add an enrichment process before iron tailings start the flotation separation to achieve a better flotation index.
04Iron tailings re-processing technology- the combined separation methods
Sometimes, if applying a single magnetic separation to the iron tailings, the separation power of ultra-fine iron minerals is low after fine grinding, which will make it easy to lose fine iron minerals during the magnetic separation process and affects the grade and recovery of the final concentrate. Sometimes, if applying a single magnetic separation to the iron tailings, the positive flotation has poor adaptability to some iron tailings, and the reverse flotation has high requirements on the grade of selected iron tailings. Besides, the cost of medicine is high. Therewith, it is a good consideration to use the combined separation methods for the iron tailings re-processing.
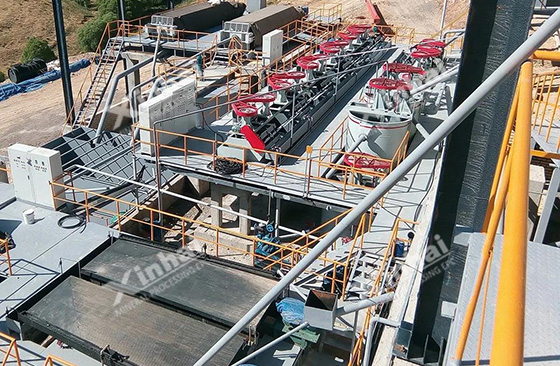
For the combined gravity-magnetic-flotation separation to recover the iron in the iron tailings, it usually takes the gravity separation as the pre-enrichment to improve the grade of minerals entering magnetic separation. Meanwhile, the pre-enrichment can also play the role of desliming and improve the recovery rate of magnetic separation. It takes the flotation separation as the supplementary measure to collect the conjoined objects not recovered in the magnetic separation to improve the whole recovery rate.
For the combined magnetic-flotation separation, it improves the grade of the mineral entering the flotation separation by making iron minerals complete the magnetic separation. At the same time, it can remove sludge and impurities, and optimize the flotation environment.
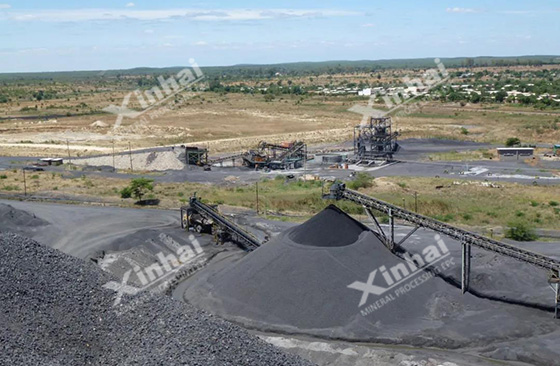
All the above is common methods of iron tailings re-processing: the magnetic separation, the gravity separation, the flotation separation and the combined gravity-magnetic-flotation separation. Among these, magnetic separation and gravity separation are the most common methods to reselect the iron tailings; the flotation separation is used for recovering ultra-fine iron tailings, but it is hard to operate, and the pharmacy system is complicated and costly.
In the actual production process, the choice of the iron tailings re-processing usually depends on various factors such as the mineral properties of iron tailings, processing plant conditions and investment budget. It's recommended to have a better understanding of iron tailings first, select the iron tailings re-processing through the mineral processing test report, and then customize the iron tailings re-processing equipment.