Manganese is a common metal mineral in nature. There are over 150 kinds of manganese minerals in nature. While the valuable manganese minerals are only a small part of them, mainly including pyrolusite, psilomelane, etc. According to the different methods in extraction of manganese, the manganese ores can be divided into 5 types: manganese oxide ore, carbonate manganese ore, iron-manganese ore, manganese iron ore, multiple-metal composite manganese ore. Because of the different types of deposits and ore characteristics, the processing flow is different in the extraction of manganese. In this article, we will take you to understand processing methods and equipment in the extraction of manganese.
Use the table of contents below to navigate through the guide:
01Manganese oxide ore extraction method
Manganese oxide is the majority of valuable manganese ores. The manganese oxide ores on the surface ground often emerges a large amount of mud in the extraction of manganese. However, there are many manganese minerals in mud. Therefore, the extraction of manganese mud is also an important part. On this classification basis, according to the manganese content and mineral impregnation particle size, the manganese oxide ores can be divided into massive disseminated manganese-rich ore, small and granular disseminated poor manganese ore, and micro-granular disseminated poor manganese ore.
1.Massive disseminated manganese-rich ore
The manganese content is higher, and the feeding size is between 40-75mm. Simple ways can easily be carried out in the extraction of manganese. Through screening or gravity separation, high-grade manganese concentrate can be recovered. Therefore, the common methods in the extraction of manganese include dense-media process, jig process, shaking table process.
Required equipment: vibrating screen, jig, shaking table.
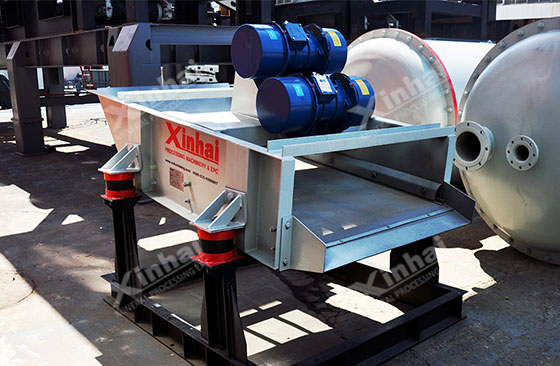
2.Small and granular disseminated poor manganese ore
The manganese content in this kind of manganese ore is usually under 30%, and the manganese minerals are in small size with a large amount of mud. The processing method is more complex in the extraction of manganese. For the manganese is weakly magnetic, this kind of manganese ore usually recover through gravity separation - magnetic separation - flotation combined processing flow. Part of mud with manganese minerals is recovered through washing first, and recover manganese through jig gravity separation - strong magnetic separation - flotation combined processing flow in the extraction of manganese.
Required equipment: magnetic separator, jig, flotation cell
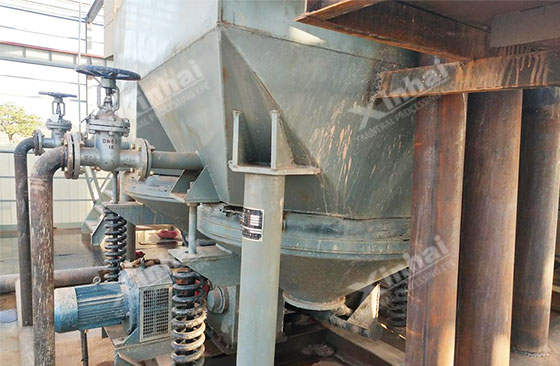
3.Micro-granular disseminated poor manganese ore
The manganese content of this kind of manganese ore is lower than 15%, and fine granularity and evenly embedded. The single mechanical processing method is hard to recover manganese mineral from this kind of ore. Chemical leaching or mechanical processing - chemical leaching combined processing technology is used in the extraction of manganese.
02Carbonate manganese ore extraction method
In carbonate manganese ore, the manganese minerals mainly exist in manganese carbonate, and micro grain size mosaic. Flotation is the main processing technology in extraction of manganese for this kind of ore. However, there are still problems such as a large amount of metal loss and large reagent consumption. Therefore, strong magnetic separation or gravity separation need to be used with flotation in the extraction of manganese.
Required equipment: flotation cell, magnetic separator, gravity separator.
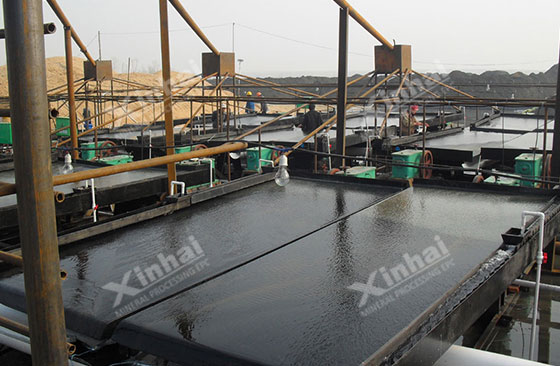
03Iron manganese ore extraction method
Manganese is the main valuable metal in iron-manganese ore. The total content of manganese and iron is over 30%. Compared with manganese oxide, iron manganese is more difficult to process. The difficulty is the separation of iron and manganese. In production, washing - jig gravity separation - roasting magnetic separation is to recover iron concentrates and manganese concentrates. Manganese concentrates with 5% iron can be recovered. And the recovery rate is up to 75.5%.
Required equipment: Linear vibrating screen, jig, cylinder washing machine.
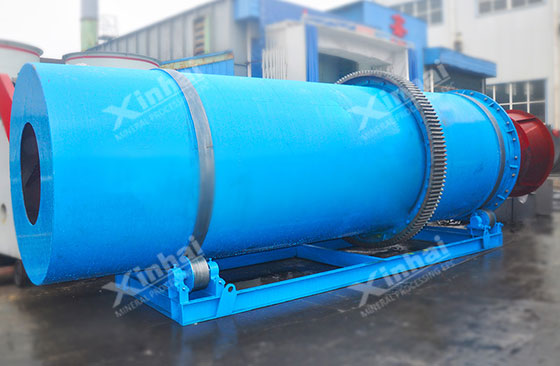
Manganese iron ore extraction method
The manganese content is low, only 5%-10% in this kind of ore. At the same time, fine grain size and close symbiosis of iron and manganese minerals are the characteristics. Chemical leaching is the common processing technology in the extraction of manganese. The recovery index is obviously better than traditional mechanical processing technology.
Multiple-metal combined manganese ore extraction method
Besides manganese minerals, there are also iron, lead, zinc, magnesium, aluminum, copper, silver minerals, which exist mainly in the oxide. Manganese has a close symbiosis with silver, iron and other minerals. According to this kind of ore, strong magnetic separation, gravity separation, flotation are used in the extraction of manganese. The mud with manganese minerals are sorted through washing and screening first, and then other valuable minerals are recovered.
In summary, we can find that, for the special characteristic of manganese ores, many manganese minerals are in the mud. It is an important part of manganese recovery in the extraction of manganese. Therefore, mud recovery needs to pay attention to. To guarantee the predicted manganese recovery rate and efficiency, it is suggested to consult with manufacturers with mineral processing quality, choosing reasonable manganese extraction flow according to the scientific mineral processing experiment report, customizing manganese processing equipment.