At present, with the depletion of high-grade gold reserves, the research on middle and low grade, refractory gold ores and the enhancement of traditional techniques used for the extraction of gold have become the mainstream trend of gold extraction in the world. Gold ore has a high mining value, the processes used for the extraction of gold is complex, and the gold extraction processes are also different.
The common processes used for the extraction of gold mainly include cyanide gold extraction, flotation and gravity separation. Next, we will explain to you the gold extraction processes.
Use the table of contents below to navigate through the guide:
01Extraction of gold by the cyanide gold extraction process
Cyanide gold extraction is one of the main methods for the extraction of gold. Generally, the cyanide gold extraction process can be divided into two types: agitation cyanide gold extraction process and percolation cyanide gold extraction process. Among them, the agitation cyanide gold extraction process is mainly used to treat the flotation gold concentrate, or all-slime cyanidation. The percolation cyanide gold extraction process is used to deal with low-grade gold-containing oxidized ore. At the same time, in view of the disadvantages of the sodium cyanide and the current environmental protection requirements, the researchers have successfully developed a non-toxic gold leaching agent to replace sodium cyanide for extraction of gold. The method of application is the same as that of sodium cyanide, but its recovery is faster, the leaching rate is higher, and the cost is lower.
1. Agitation cyanide gold extraction process
The agitation cyanide gold extraction process mainly includes two kinds of gold extraction processes. One is the cyanidation - zinc replacement process (CCD process and CCF process), in which the gold is extracted by zinc powder (silk) displacement precipitation after the continuous countercurrent washing. Another is an unfiltered carbon in pulp process (CIP process and CIL process), in which the gold is extracted by the adsorption of activated carbon directly from cyanidation pulp without filtration washing.
① Extraction of gold by cyanidation - zinc replacement process
The extraction of gold by the cyanidation-zinc replacement process (CCD process and CCF process) is used for the treatment of gold-bearing pregnant solution after cyanide leaching. The working principle is to use the zinc powder (silk) as the reducing agent to replace the gold and silver from the leaching liquid. This gold extraction process mainly includes reverse washing, solid-liquid separation, leaching liquid purification, deoxidation, zinc powder (silk) replacement.
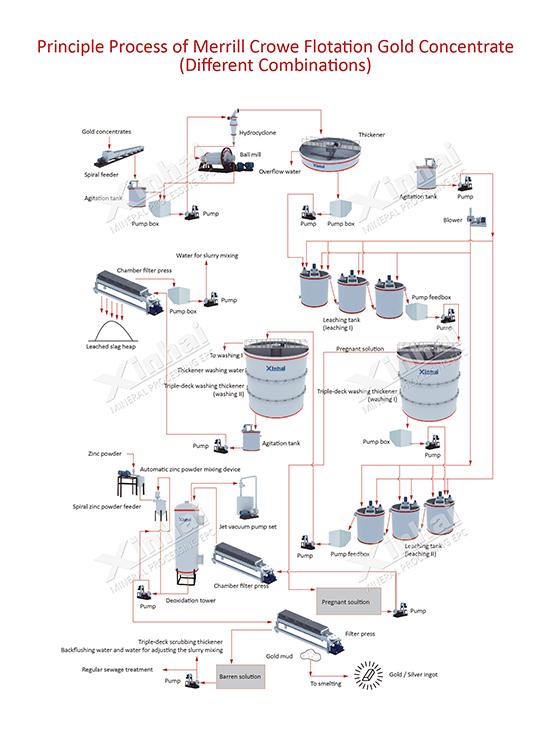
◆ Reverse washing, solid-liquid separation: Separate the pregnant solution (leaching liquid) from the solid.
◆ Leaching liquid purification: Remove the suspended matter in the pregnant solution (leaching liquid), so that the gold-bearing pregnant solution in the replacement operation can reach a clear and transparent state.
◆ Deoxidation: Remove the dissolved oxygen from the pregnant solution (leaching liquid).
◆ Zinc powder (silk) replacement: Use the zinc powder (silk) to replace the precious metal in the pregnant solution (leaching liquid) to form gold (silver) mud.
② Extraction of gold by carbon in pulp process
Extraction of gold by carbon in pulp process (CIP process and CIL process) is to put the activated carbon into the cyanide pulp, adsorb the dissolved gold on the activated carbon, and then extract the gold from the activated carbon. This gold extraction process mainly includes the preparation of leaching raw materials, agitation leaching and countercurrent carbon adsorption, gold loaded carbon desorption, electrodeposition electrolysis, smelting ingot, carbon regeneration.
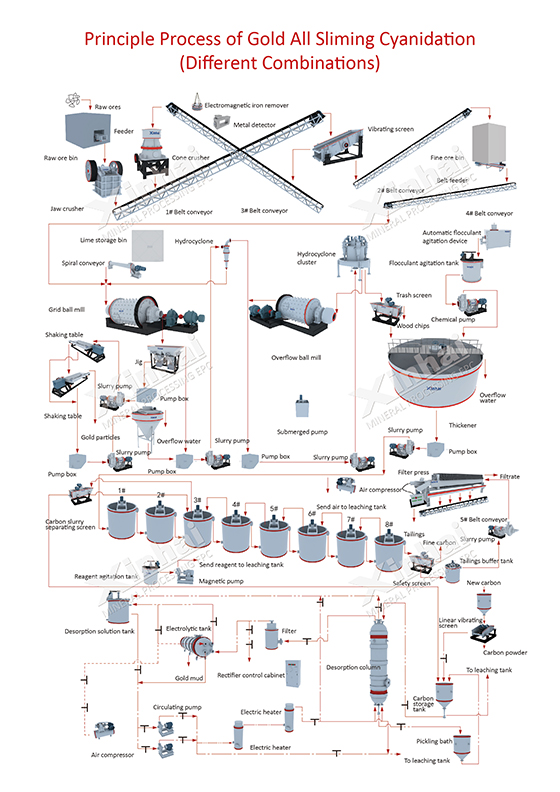
◆ Preparation of leaching raw materials: When the gold is extracted by carbon in pulp process, the leaching materials include physical crushing, grinding and classification. In general, the overflow fineness of grinding and classification is mostly -200 mesh, accounting for 85-95%.
◆ Chip removal: The chips and sundries in the pulp are easy to cause the block of pipe and screen, and also easy to absorb the gold in the pulp and mix it into the rich carbon, so they must be removed before leaching operation. If necessary, the pulp shall be concentrated and the disincrustant shall be added. The disincrustant can also reduce the scaling on the surface of activated carbon and screen. In general, the chip removal operations shall be carried out in the grinding process, respectively in the overflow position of first and second grinding and classification. The chip removal equipment often adopts the intermediate frequency linear vibrating screen, spiral screen and cylinder screen can also be applied in the first time of chip removal operation. The opening size of the trash screen shall be as small as possible under the premise that the screen surface does not run.
◆ Thickening before leaching: When the overflow concentration of grinding and classification is mostly 18-22%, it is suitable to leach directly, and the pulp must be concentrated. It is suggested to use the high efficient thickener with a small area and high thickening efficiency.
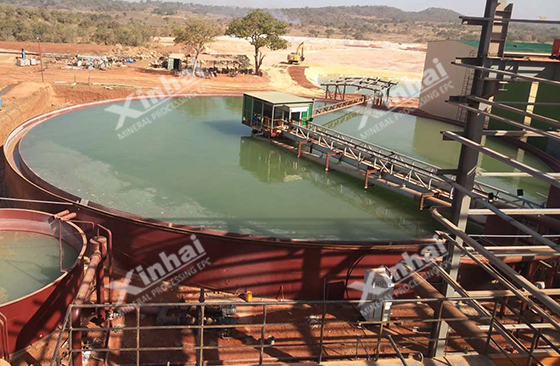
◆ Agitation leaching and countercurrent carbon adsorption: In thegold CIP process, the leaching and adsorption are two independent operations. In the adsorption operation, the leaching process has been basically completed, and the size, number and operating conditions of the adsorption tank are determined by the adsorption parameters. In the gold CIL process, the leaching and adsorption are carried out simultaneously. In general, the leaching operation takes a longer time than the adsorption operation, so the size, inflation and dosing of the leaching tank are determined by the leaching parameters. In order to increase the concentration of dissolved gold in the front adsorption tank and increase the leaching time at the same time, 1-2 stages of pre-leaching operation are usually added before leaching and adsorption both together.
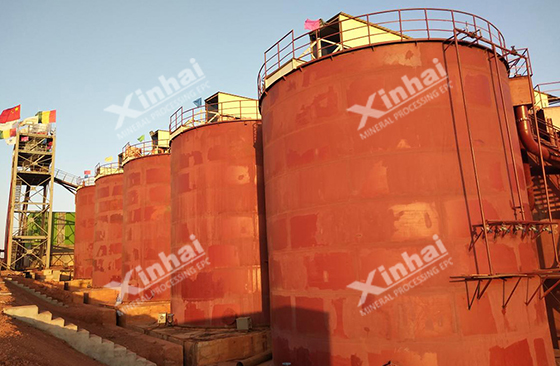
◆ Gold-loaded carbon desorption, electrodeposition electrolysis: The gold- loaded carbon and ore pulp are lifted to the carbon separation screen (generally the linear vibrating screen) through the carbon pump or air lifter, then washed with clean water on the screen to separate the carbon from the ore pulp. The gold-bearing carbon enters the storage tank, and the ore pulp and washing water enter the first adsorption tank. At present, the common desorption method for gold-bearing carbon is high temperature and high-pressure desorption method, that is, Au(CN)2- is replaced by adding anions that are easy to be absorbed by activated carbon in the desorption system, realizing the desorption of gold. The pregnant solution obtained from the desorption of gold-bearing carbon is recovered by ionization to obtain solid gold.
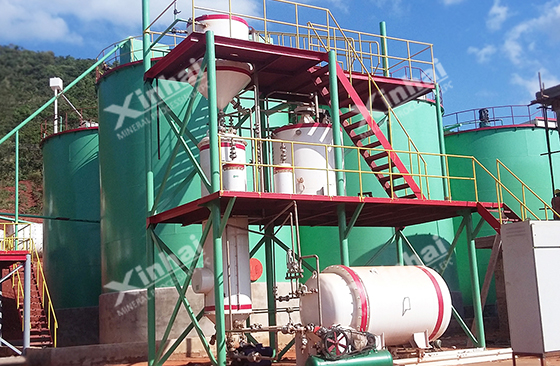
◆ Smelting ingot: After pickling and removing impurities, the gold mud can be directly smelted into gold ingots. By hydrometallurgy, the purity of gold ingots can reach over 99.99%.
◆ Carbon regeneration: After the adsorption and desorption, the activated carbon needs regeneration to restore its good adsorption performance. Generally, the activated carbon after desorption is first pickled to remove the carbonate and other accumulations. After several times of use, the adsorption activity of carbon shall be restored by the thermal activation, and then it can be recycled. The main equipment includes activated carbon regeneration kiln, water quenching trough, fine carbon separation screen.
③ Extraction of gold by cyanidation - ion-exchange resin adsorption process
The ion-exchange resin adsorption process is basically similar to the carbon in pulp leaching and adsorption process. The difference is to change the carbon to ion exchange resin. This gold extraction process includes the gold-loaded resin desorption electrolysis, smelting ingot, resin regeneration.
◆ Gold-loaded resin desorption electrolysis: The gold loading resin and pulp are lifted to the resin separation screen (generally the linear vibrating screen) through the pump or air lifter, then washed with clean water on the screen to separate the carbon from the ore pulp. The gold-bearing resin enters the resin storage tank, and the ore pulp and washing water enter the first adsorption tank.
The cleaned gold-loaded resin is fed into the desorption column, and the desorption solution is added. Under 36 hours at the temperature of 40-60°C, the pregnant solution after the desorption is put into the electrolyzer, and the gold mud is recovered by the ionization method.
◆ Smelting ingot: After pickling and removing impurities, the gold mud can be directly smelted into gold ingots. By hydrometallurgy, the purity of gold ingots can reach over 99.99%.
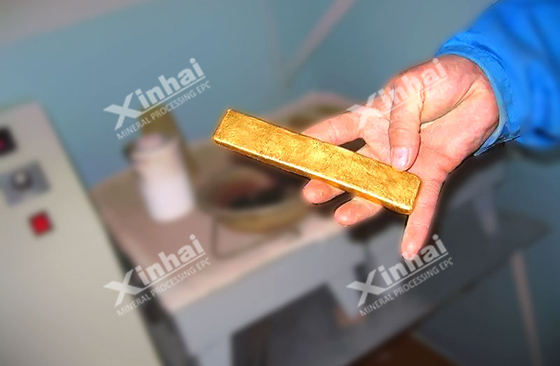
◆ Resin regeneration: After the desorption, the resin needs regeneration to restore its good adsorption performance. Add the sodium hydroxide solution, agitate and soak for 12 hours intermittently, remove the soaking solution, rinse with water until be neutral, and then use the resin again.
2. Percolation cyanide gold extraction process
Percolation cyanide gold extraction process is also one of the cyanide leaching processes. Based on the cyanide solution permeating through the ore layer, the gold in the gold-bearing ore can be leached, which is suitable for placer and porous materials.
There are two kinds of percolation cyanide gold extraction processes: pool leaching and heap leaching. The leaching solution is percolated, then the activated carbon or zinc powder (silk) replacement is used to extract the gold.
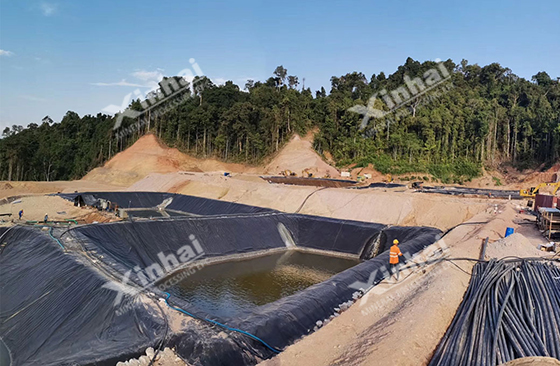
① Pool leaching
The percolation leaching is usually carried out in a leach tank, which usually includes wood tank, iron tank, or cement tank. The bottom of the pool is horizontal or slightly inclined in a round, rectangular, or square shape. The tank is equipped with a false bottom made of perforated acid-resistant plate, which is covered with a press cloth, and the press cloth is covered with the grid with wooden or corrosion-resistant metal strips. When leaching, the ore is placed in the pool, and the leaching agent is added above the pool, the leaching liquid flows out from the false bottom part. The false bottom is used to filter and support the ore.
The leaching time not only depends on the dissolution rate of mineral by solvent, but also depends on the permeability rate of solvent in the material layer. And the permeability rate mainly depends on the loading height, porosity, silt content, leaching agent viscosity and material characteristics.
② Heap leaching
The raw ore is transferred to the ore mining yard prepared in advance or the waste rock or low-grade ore, then the cyanide leaching liquid spray or infiltrate the ore, the solution produces the percolation leaching when it passing through the ore. After many times of leaching liquid cycling, repeat spray, the leachate is collected, then the activated carbon or zinc replacement is used to extract the gold, and the lean solution returns to the heap leaching for recycling.
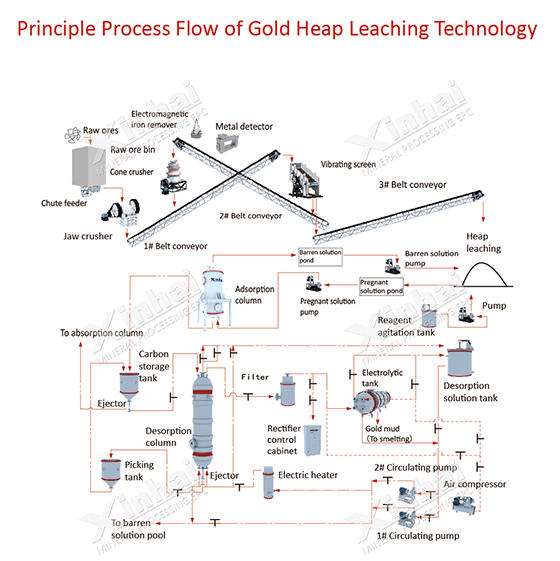
The heap leaching sites are usually located in the hilly areas with a gentle slope (natural gradient 5-15), which is close to the stope and convenient for transportation. Firstly, clean the weeds, floating soil and tamping, then build a foundation with a gradient of around 5˚, the height on both sides slightly lower in the middle, so that the leaching fluid can be concentrated into the storage tank. The storage yard is covered with a geotechnical film to prevent leakage. Soil banks of 0.4 meters are built around the yard and used as drains to prevent rainwater from flowing into the yard. A large lean ore with 0.3 m thick is deposited before the ore is piled.
The heap leaching method has low production cost and can be put into production quickly. Besides, the scale of heap leaching can be large or small, and the amount of ore in each heap can reach hundreds of tons. Heap leaching or granulation heap leaching can be used after ore crushing to a certain size.
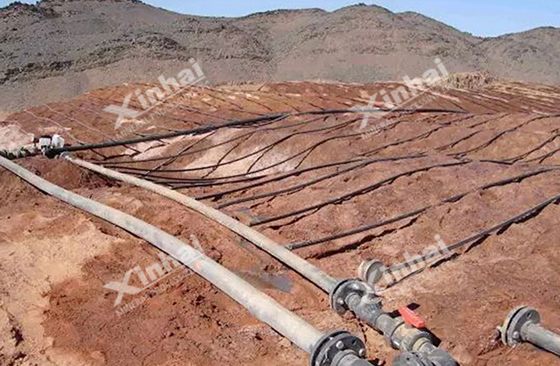
02Extraction of gold by the gold flotation process
The flotation process is a separation method that is widely used in the extraction of gold, often used for gold-bearing handling sulfide minerals with high flotability. This gold extraction process is to float the gold into copper, lead concentrate, and then extract the gold from these concentrates. Therefore, it is a more economical and reasonable process for the extraction of gold ore with non-ferrous metals. This gold extraction process can realize the comprehensive utilization of metal, and enrich the gold as much as possible into the sulfide minerals.
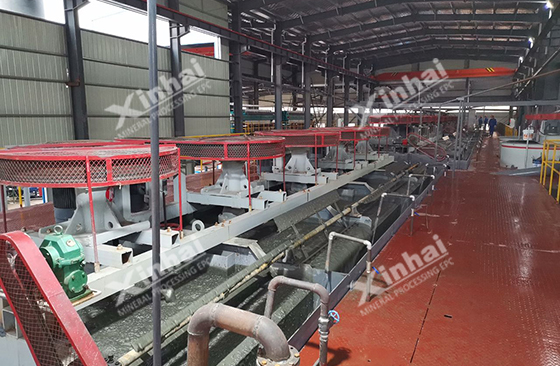
In order to improve the return rate of investment, the gold flotation process can also be used as the combined process with other mineral processing processes to achieve more impressive results for different types of gold ores.
1. Flotation - cyanide leaching of concentrate
This process for the extraction of gold often adopts xanthate as the collector, terpenic oil as the foaming agent. The gold concentrate is floated by the weakly basic pulp in the flotation machine. Then, the flotation concentrate is sent to cyanide leaching, the gold is dissolved by the cyanide, the complex compound enters the solution, and the gold mud is obtained by the zinc powder replacement. Finally, the pure gold is obtained by the pyrometallurgy of gold mud.
2. Flotation – concentrate thiourea leaching process
For vein gold ores with high arsenic and sulfur or high carbonaceous mud, gold sulfide concentrate can be obtained by the flotation method, and then the gold is recovered by the concentrate thiourea leaching process.
The extraction of gold by the thiourea leaching process is a new gold extraction process with low toxicity. The thiourea acid solution has the fast speed of gold and silver dissolution, low toxicity and easy to regeneration. The components, such as antimony, arsenic, copper, sulfur, are not sensitive to thiourea leaching, but can affect the cyanide gold extraction process. Therefore, thiourea leaching can be used to extract the gold and silver from gold-bearing ores that are difficult to be processed by the cyanide gold extraction process. At the same time, the time of thiourea leaching is generally much shorter than that of cyanide leaching.
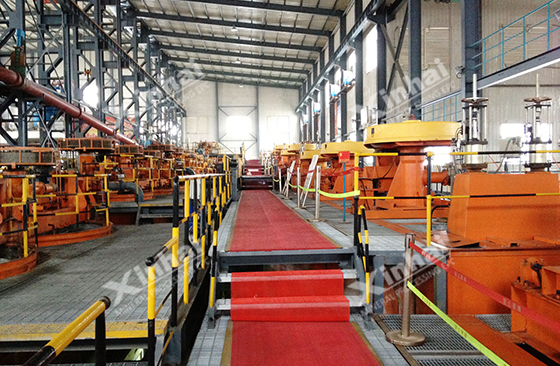
3. Flotation - concentrate roasting - high acid washing - cyanide leaching
For flotation concentrate containing high arsenic and sulfide, the cyanide tailing is floated first, the impurities, such as sulfur, iron, arsenic, are enriched into the concentrate, which becomes the refractory high sulfur arsenic concentrate, cannot be processed by the cyanide leaching directly. Therefore, the flotation concentrate is sent to oxidizing roasting to remove the sulfur and arsenic. The calcine has a loose structure, which is more beneficial to the gold and silver leaching. Then, using the high acid pretreatment washing, most impurities can be dissolved by the acid, and removed by the washing, which guarantees the cyanide leaching rate, enriches the gold grade effectively.
03Extraction of gold by the gravity separation process
With the help of the dielectric fluid and the combined force of various mechanical power, the gravity separation process uses the differences in mineral density and particle size to form the appropriate loose stratification and separation conditions, thus obtaining the products with different density and different particle sizes. Because most gold-bearing ores contain a certain amount of coarse-grain free gold (+0.1mm), it is difficult to be recovered by flotation and hydrometallurgy. Therefore, the gravity separation process is mostly used to separate the alluvial gold and to recover the monomer dissociated coarse grain gold before and after the flotation and leaching of the vein gold ore. In general, the lower limit of the particle size of gold extraction by the gravity separation process is 0.01mm.
1. Alluvial gold gravity separation process
① Extraction of gold by jigging
The main equipment used in the gravity separation by jigging is the jig. The jigging process is to mix the mineral particles with different specific gravity and stratify them according to the specific gravity in the variable speed medium flow with vertical movement. The minerals with small specific gravity are in the upper layer, while the minerals with large specific gravity are in the lower layer. The layered materials are discharged separately by means of machinery and water flow. Extraction of gold by jigging used for gold recovery is suitable for separation of coarse mineral particles (any raw mineral materials except for superfine material mineral), the range of beneficiation size is from 50 mm to 0.074 mm. For the placer gold ore, the lower limit of beneficiation size is 0.04 mm if the proportion difference is equal to or larger than 1.25, and the ore achieves the monomer dissociation. The extraction of gold by jigging used for gold recovery is featured with simple process operation, large equipment processing capacity, which is widely applied in the roughing gold extraction.
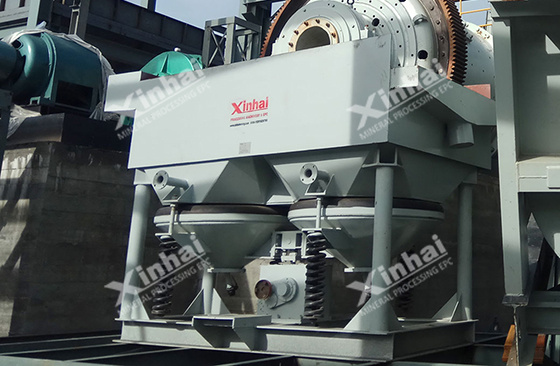
② Extraction of gold by shaking table
The extraction of gold by shaking table used for gold extraction is suitable for processing the minerals with fine particles. According to the different particle sizes, the ore can be divided into a coarse sand bed, fine sand bed and slurry bed. The coarse sand bed is suitable for the material particle size between 2.0 mm to 0.5 mm, the fine sand bed is suitable for processing material particle size between 0.5 mm to 0.074 mm, the slurry bed is suitable for processing the material particle size between 0.074 mm to 0.037 mm.
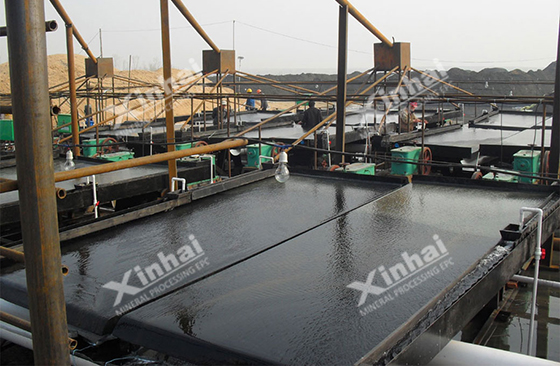
The feed size of the extraction of gold by shaking table is generally between 3mm-0.019mm. This gravity separation process is featured with stable and reliable gold extraction, clearly visible ore belt distribution, higher rich ore ratio than other methods, easy to manage and the required ore can be separated at once.
③ Extraction of gold by spiral chute
The main equipment used in the extraction of gold by spiral chute is the spiral chute, which is a separation equipment with the help of ramp flow. The material particles settle on the different zone of chute under the joint force of water flow, mineral gravity, frictions between mineral grain and chute bottom. The particles with a small proportion are taken away by the water flow, and the particles with a large proportion are left.
The spiral chute is suitable for the treatment of micro-grained materials with low mud content. The particle size range is 0.6 mm-0.03mm. Gravity separation by spiral chute used for gold recovery is featured with simple structure, large processing capacity and low comprehensive cost.
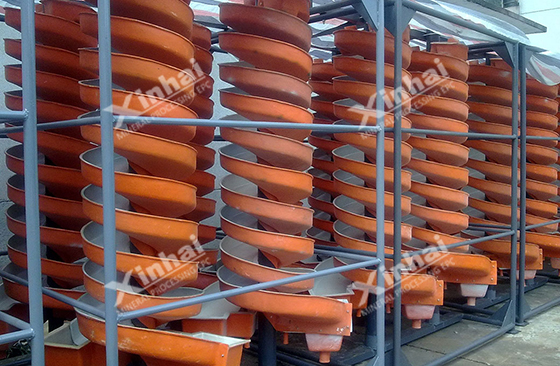
2. Vein gold gravity separation process
The gravity separation process is seldom used alone in the vein gold extraction plant, but as a part of the combined gold extraction process. Generally, in the grinding and classification circuit, the combination of jig, spiral chute and shaking table recover the dissociated coarse monomer gold in advance, so as to facilitate the subsequent flotation or cyanidation operations and obtain the qualified gold concentrate. This gold extraction method is widely used in small gold mines.
① Gravity separation – cyanide gold extraction process
This gold extraction process is suitable for the treatment of gold oxide ore in quartz vein. The gold is extracted by the gravity separation process, the obtained concentrate is sent to cyanidation. Or the raw ore can be processed by gravity separation directly, and the tailings and classified ore is processed by cyanidation respectively.
② Gravity separation - flotation process
This gold extraction process adopts the gravity separation to recover the coarse gold, the flotation process to deal with tailings. This gold extraction process is suitable for the ore treated by a single flotation process, gold-containing oxidized ore and associated free gold ore, it can obtain a higher recovery rate than that of a single flotation process.
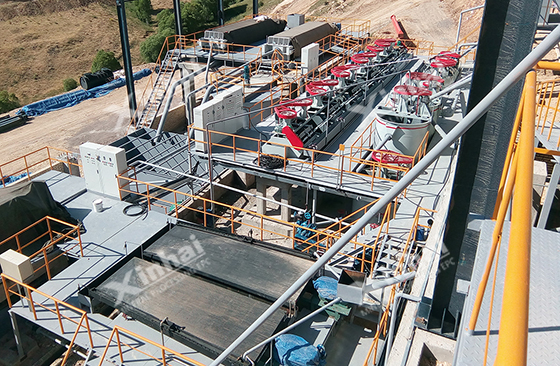
③ Flotation – gravity separation process
This gold extraction process gives priority to the flotation process, which is suitable for the gold ore that has a close symbiosis with sulfide, and can only be recovered by smelting method. Besides, it is also suitable for the gold-bearing quartz vein ore with uneven distribution, which can obtain a higher recovery rate than that of a single flotation process.
In the closed-circuit grinding system of rock gold extraction plant, the coarse grain gold is easy to be concentrated in the circulating material or embedded in the lining plate (or medium) of the ball mill, resulting in the loss of gold. Moreover, the gold grains have great toughness and are not easy to be finely ground in the grinding process. The cyanide leaching process belongs to the diffusion control process, and this part of gold dissolves slowly, which is easy to cause incomplete leaching of gold ore, thus remaining in the cyanide tailings. Therefore, the gravity separation process is mostly used to recover this part of coarse gold in advance in the grinding process.
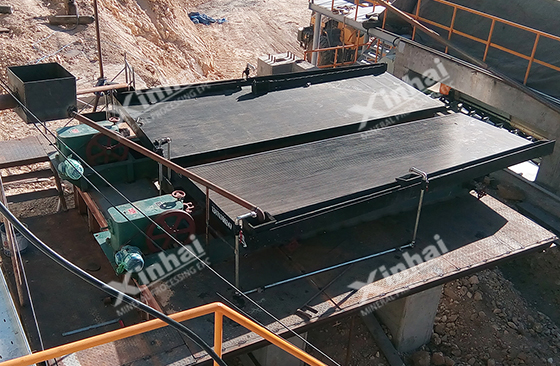
For the extraction of gold by the gravity separation process, the alluvial gold ore is processed by the gravity separation process to separate gold and heavy placer minerals. While the load gold mines are mostly processed by flotation, gravity separation, cyanidation and other combined mineral processing processes. It is suggested to adopt stage grinding, stage separation process as far as possible, so as to recover the coarse gold timely.
Gold mineral resources are very precious. In order to separate the gold ore reasonably, the process used for the extraction of gold ore is very important. If you want to extract the gold ore more economically and environmentally, the mineral processing test must be carried out first, which can analyze the nature of the ore comprehensively and obtain the scientific beneficiation test report, thus to determine the process used for the extraction of gold ore.