Iron is the main impurity ore for purification and whitening of kaolin. Its occurrence state is diverse, often in the form of hematite, pyrite, siderite, limonite, anatase, ilmenite and other minerals, and sometimes contains mica, tourmaline, etc. Therefore, iron removal is the main measure for kaolin whitening. You will learn from the following common kaolin iron removal methods, which can effectively remove iron minerals from kaolin mines and improve the whiteness of kaolin.
Use the table of contents below to navigate through the guide:
01Kaolin magnetic separation method for iron removal
Magnetic separation can be used to treat almost all kinds of kaolin with iron impurities. Magnetite and ilmenite strong magnetic minerals can be directly removed by conventional magnetic separator equipment. Weak magnetic minerals such as hematite, siderite and limonite can be removed by high gradient magnetic separator. Weak magnetic minerals such as mica and tourmaline need to be converted into strong magnetic iron oxide by roasting method, and then iron is removed by magnetic separation method.
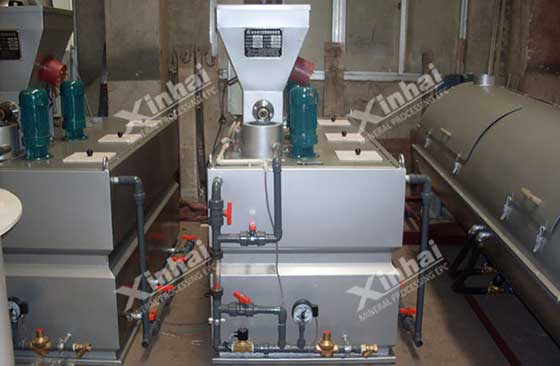
02Kaolin flotation method to remove iron
Flotation is mainly used to remove titanium-iron impurities in kaolin. There are two main flotation methods: carrier flotation and direct flotation.
Carrier flotation: Kaolin with very fine impurity mineral particles can be removed by carrier flotation. Common carrier minerals can be calcite or silica sand. The dosage of carrier minerals is generally 10% to 20% of the weight of kaolin. In the flotation process, sodium silicate is used as dispersant, ammonium hydroxide and caustic soda are used as pH adjusters, and tar oil, fatty acid and petroleum calcium sulfonate are used as collectors. These agents can help complete the flotation titanium removal operation. However, flotation has many disadvantages. For example, the hydrophobization of the carrier requires a large amount of chemicals, and the flotation process can only be effective when the slurry concentration is low. Additionally, residual chemicals and carrier minerals in the clay are detrimental to the final product.
Direct flotation: Direct flotation is mainly used to remove kaolin containing anatase impurities. It is characterized by high-energy scrubbing when the solid concentration is 40% to 60% in the presence of dispersant and pH adjuster. Anatase and hematite are dissociated from kaolin minerals, and then a small amount of activator and fatty acid collector are added. Selective agglomeration of anatase covered by a collector is formed under high shear stirring conditions. Then the pulp is diluted to 15%~20% solids, and then flotation is carried out to remove impurities.
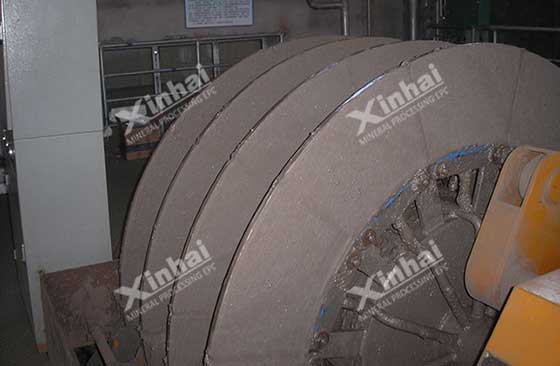
03Kaolin coagulation/flocculation method for iron removal
Kaolin coagulation or flocculation method is mainly to remove iron and titanium impurities in kaolin. When pH=8~11, adding alkaline metal ions (such as calcium ions, manganese ions, etc.) to the kaolin slurry can selectively coagulate iron and titanium impurities. Weak anionic polyelectrolytes are then selectively flocculated to obtain high-quality kaolin concentrates.
04Kaolin acid leaching method for iron removal
The acid leaching method uses an acid solution to convert insoluble compounds in kaolin into soluble compounds, thereby realizing the separation of kaolin and iron impurities. Generally, heated acid leaching is often used. After the pulp is heated to a certain extent, the H+ in the acid is replaced by the ferric ions. At this time, soluble iron compounds are formed and enter the solution to complete the iron removal operation. Commonly used acid solutions are sulfuric acid, hydrochloric acid and oxalic acid.
05Kaolin oxidative leaching method for iron removal
The oxidative leaching iron removal method uses a strong oxidant to oxidize insoluble ferrous iron (such as pyrite) into water-soluble ferrous ions in an aqueous medium. In a strong acidic medium, when the pH is high, ferrous iron may become insoluble ferric iron. At the same time, the ferrous ion will lose its solubility and realize the separation of kaolin and iron impurities. Commonly used oxidants are sodium hypochlorite, hydrogen peroxide, potassium permanganate, chlorine, ozone, etc.
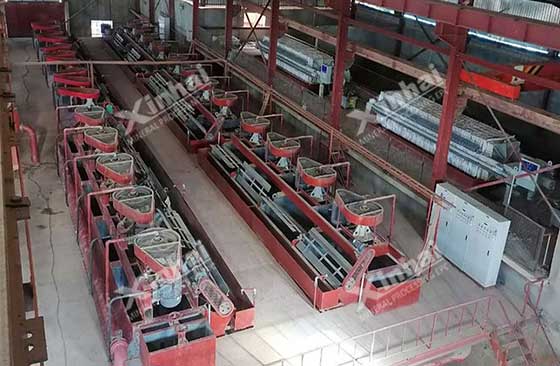
06Iron removal by kaolin reduction leaching method
The method uses a reducing agent to reduce insoluble ferric iron (such as limonite) into soluble ferrous iron. After filtering and washing, the ferrous iron is removed with the filtrate to achieve the effect of iron removal. Commonly used reducing agents are hydrosulfite, sodium borohydride and acid-soluble hydrogen.
The above are several common methods for removing iron from kaolin. There are many types of iron impurities in kaolin, so the beneficiation methods used are different. Xinhai suggests to conduct mineral processing test on kaolin first. After analyzing the properties of impurity ore through experiments, a reasonable mineral processing process and a complete set of beneficiation equipment are designed to achieve an ideal return on investment.