Graphite is an important non-metallic mineral, which can be applied in many fields, such as optics, energy, aerospace, environment and new materials, after purification. Therefore, it is of great strategic significance for its processing and purification. Graphite ore is often associated with quartz, illite, kaolinite, sericite and a small amount of hemite, limonite, calcium carbide, calcite, etc., which need to be purified and applied. There are six common graphite extraction processes: selective flocculation, flotation, basic acid, acid leaching, chlorination and high temperature roasting.
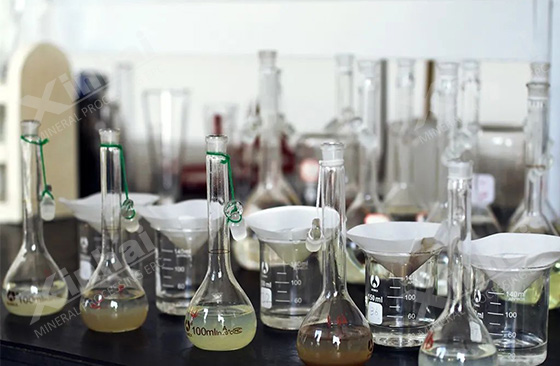
Use the table of contents below to navigate through the guide:
01Selective flocculation method for graphite extraction
To purify graphite ore by selective flocculation method, polymer flocculant should be added to the suspension containing two or more components, so that the flocculant can selectively adsorb some components in the suspension, and produce flocculation precipitation through the action of bridge chain, so as to achieve the purpose of component separation.
The main flocculants are sodium silicate, sodium hexametaphosphate, lignin starch. Carboxymethyl cellulose and water glass were used as dispersants, and cassava powder, acorn powder, sodium alginate and polyacrylamide were used as flocculants to purify graphite ore.
The selective flocculation and purification method of graphite ore are relatively simple, and the cost is low, but the fixed carbon recovery rate is low, only about 40%.
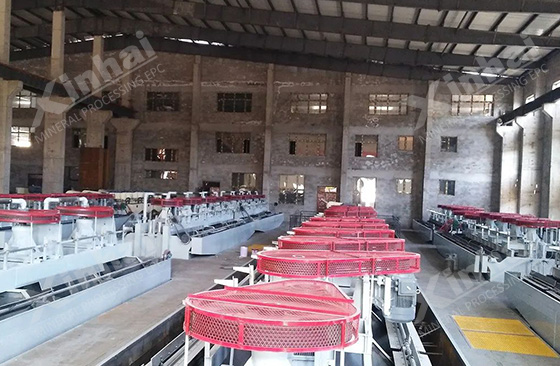
02Flotation method for graphite extraction
Flotation is a common method for graphite ore purification. It is mainly used by adding a series of flotation agents to enrich the selection of the target minerals at the gas-liquid interface, so as to realize the separation from the impurity minerals and achieve the purpose of purification.
Graphite itself has good natural buoyability and hydrophobicity, so conventional graphite ore can be purified by flotation process. In the purification process, in order to protect the large scales of graphite, the process of multiple stages of grinding, multiple separation and coarse concentrate regrinding and dressing is generally adopted.
The commonly used traps in graphite ore flotation method are mostly coal tar, pinol oil or butyl ether oil for foaming agent, and water glass and sodium fluorosilicate are mostly used for inhibitors.
The purification of graphite ore flotation method can make the graphite grade reach 80%~90%, or even about 95%, and this method has low drug consumption, low energy consumption and low cost. However, for the extremely fine silicate minerals and potassium, calcium, sodium, magnesium, aluminum and other compounds in graphite ore, the monomer dissociation can not be carried out in the grinding stage, and other processes need to be purified again after flotation.
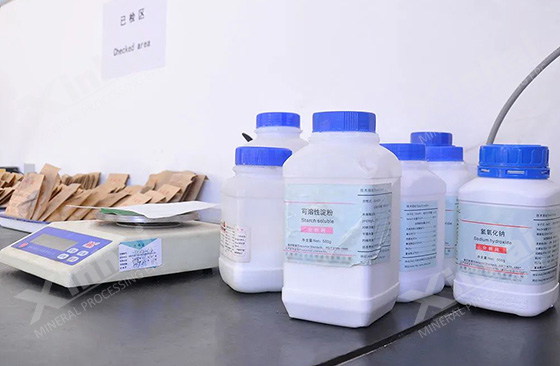
03Alkaline acid method for graphite extraction
Graphite purification by acid-alkali method is a mature process method, which can be divided into two processes: alkali melting and acid soaking.
Alkaline melting process: under high temperature conditions, the chemical reaction of molten alkali and graphite (silica, silica, quartz) to generate soluble salt, and then use washing method to remove impurities.
Acid immersion process: the acid reacts with metal oxide impurities to convert part of the impurities without reaction in the alkali melting process into soluble salt, and then the impurities are separated from graphite by washing method, so as to improve the purity of graphite.
The purification of graphite ore alkali acid method can make the graphite taste reach 99.5%, and the equipment is simple, low energy consumption and small one-time investment. However, the acid and base of this method will be highly corrosive to the equipment, and the wastewater after purification will be seriously polluted. In addition, there are also the disadvantages of graphite loss.
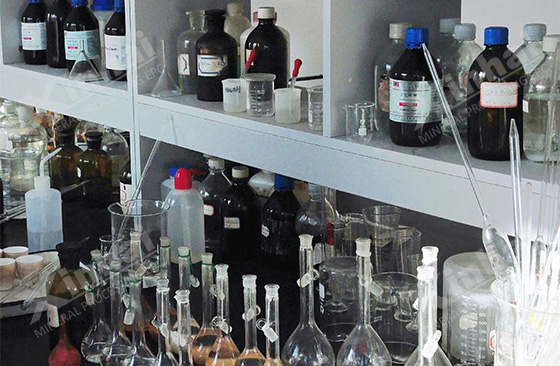
04Acid immersion method for graphite extraction
The acid used by acid immersion method is sulfuric acid, hydrochloric acid, nitric acid, hydrofluoric acid, etc. Among them, sulfuric acid and hydrochloric acid are more suitable for leaching acid, leaching ability. But some sulfates have less solubility, and hydrochloric acid is more expensive. Nitric acid oxidation and volatile is strong, see light is easy to decompose and easy to produce highly toxic photogas, easy to explode at high temperature. Hydrofluoric acid cannot undergo oxidation reaction or reduction reaction, and the focus is to effectively dissolve SiO2 and silicate. After fully mixing graphite and hydrofluoric acid, hydrofluoric acid will react with impurities in graphite to produce compounds and volatiles dissolved in water. And then by removing the soluble impurities by washing, high purity graphite can be obtained.
Hydrofluoric acid purification of graphite ore can effectively remove impurities in minerals and has low energy consumption. But this method is highly toxic, and the environmental pollution is larger.
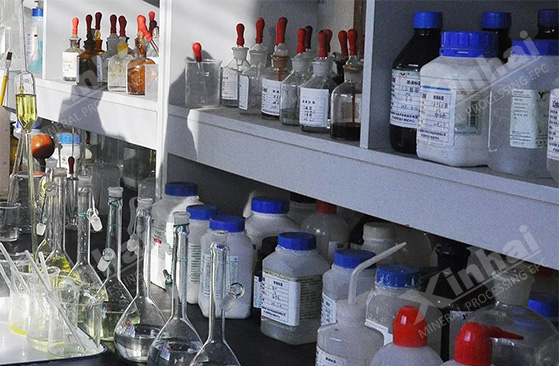
05Chlorination roasting method for graphite extraction
The purification of graphite ore by chlorination roasting method is mainly to add the appropriate amount of reducing agent in the graphite ore. Then in a specific atmosphere and equipment at high temperature roasting, so that the mineral valuable metal and chloride combination, into the gas phase or condensed phase metal chloride with low melting point boiling point, so as to precipitate and achieve effective separation from other components, to obtain high purity graphite.
Chlorination roasting method has high efficiency, low energy consumption and low cost. However, chlorine gas has strong corrosive and toxic properties, and causes great pollution to the environment.
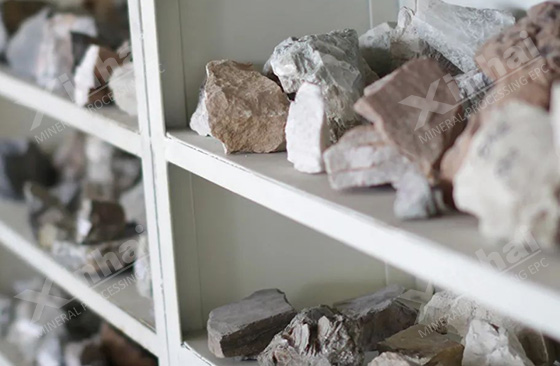
06High-temperature roasting method for graphite extraction
The melting point of graphite ore is very high (melting point is 3652℃, boiling point is 4250℃), which is much higher than other impurity minerals. The purification of graphite by high temperature roasting method is to use the difference of melting point of graphite to heat the graphite ore to 2700~3000℃, most of the impurities have been vaporized, so it can effectively separate graphite from impurities.
The high temperature roasting method can reach 99.99% or even higher, but the energy consumption is large, the requirements for equipment are very high, in addition, the purity of graphite raw ore has certain requirements.
These are the six common graphite ore extraction processes. As for which one to choose, it should be decided according to the nature of the graphite ore, the plant conditions, investment budget and other factors. It is suggested that when choosing the process, the graphite mineral processing test should be carried out first, and the graphite extraction process should be selected specifically through the test report, so as to strive for the ideal technical and economic benefits.